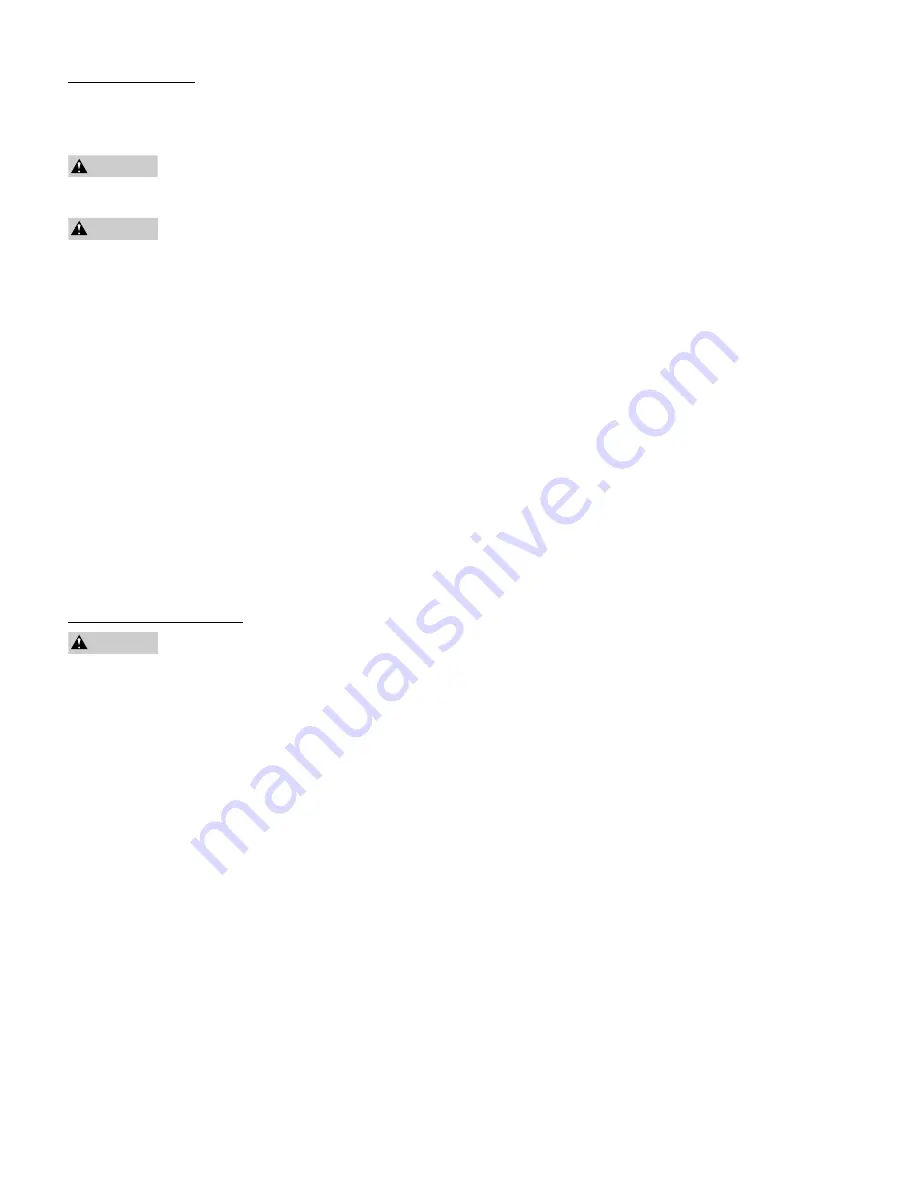
MAINTENANCE
LUBRICATION
The pump requires only water for lubrication and must
never be run dry.
CAUTION
Running the pump dry may cause damage
to the pump and system components.
WARNING
Before disconnecting pump, be sure fuse
box leads are disconnected or power is turned off. After
reassembling the pump, refer to priming instructions
before running.
DRAINING
If your pump must be drained for service or to prevent
damage from freezing, remove the drain plug from the
pump case.
NOTICE: While this will drain the pump, it will not
necessarily drain all other parts of the piping system.
If there are any concerns with the proper procedure
or necessity of draining the suction plumbing,
contact your contractor.
All piping and water tanks exposed to freezing weather
should be drained. If there are any concerns with the
proper procedure to drain the systems pressure tank,
contact the tank manufacturer for assistance.
PUMP DISASSEMBLY
WARNING
Before disconnecting pump, be sure fuse
box leads are disconnected or power is turned off at
the breaker box. After reassembling the pump, refer to
priming instructions before running.
DISASSEMBLY
If you experience problems with your pump,
determine the trouble from the service check list (see
TROUBLESHOOTING below). If the shallow well jet
nozzle needs cleaning, it can be accessed through the
¼” inline plug on the shallow well injector housing bolted
to front of the pump. If you need to service the impeller,
motor or seal, use the following procedure, going as far
as needed to correct the problem:
1.Disconnect the power to the unit.
2.Disconnect the pump from the piping system at the
piping unions. If there are no piping unions in your
plumbing system the discharge line will have to be cut.
3.Remove the suction flange and base from the front of
the pump by unscrewing the four 3/8”-16 bolts.
4.Remove the rubber grommet from the eye of the
diffuser.
5.Unscrew the three socket head screws that hold the
diffuser inside the pump case, and remove the diffuser.
6.Remove the stainless steel floating eye seal from the
eye of the impeller.
7.Remove the cover from the opposite end of the motor
and hold the shaft with a 7/16” open end wrench. The
motor shaft is flatted behind the centrifugal switch, close
to motor end bell. The open end wrench can be inserted
down onto the shaft from behind the motor overload.
8.Unscrew the impeller from the motor shaft by grasping
the OD of the impeller with a gloved hand and rotating
counterclockwise.
9.Remove the rotating portion of the shaft seal from the
motor shaft.
10.Remove the motor from the bracket by unscrewing the
four 3/8”-16 bolts.
11.Tap the stationary portion of the seal out of the pump
bracket with a flat bladed screwdriver.
12.Reassemble in reverse order. Clean the seals and
the sealing surfaces in the pump case. Lightly lubricate
the rubber part of the seals with silicone grease to aid in
assembly. DO NOT lubricate the carbon or ceramic faces
on the shaft seal.