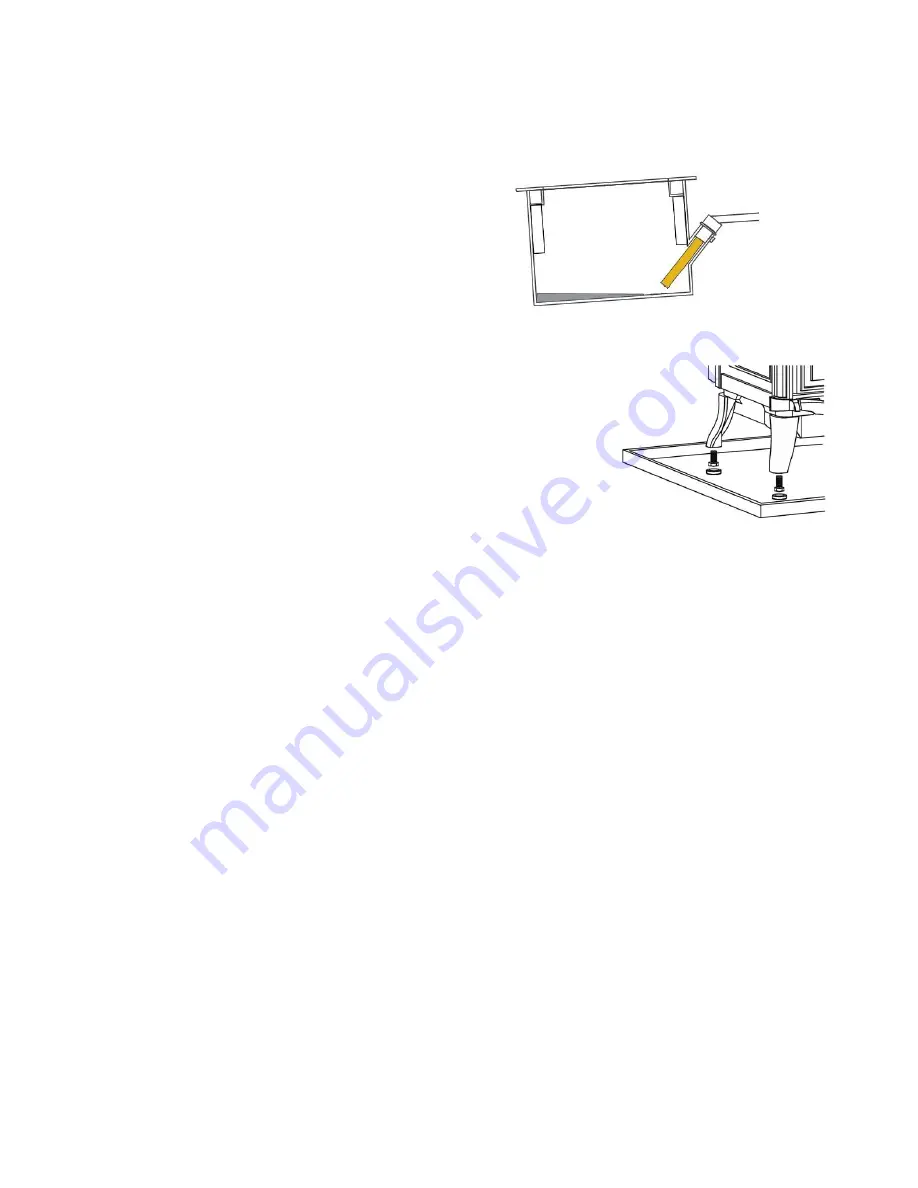
Electric Ignition
The electric ignition system operates by heating a ceramic electric heating element positioned 2mm from the bottom
of the burner. Oil entering the burner is heated to its ignition temperature by the heating element. The element is
energised for the period that the ignition button is pressed, between 30 seconds and a minute.
Common reasons for ignition to fail
Electrical cable not connected.
Oil supply switched off.
Burner has large amount of oil in the base.
Stove not level.
Igniter leads at the control box poorly connected.
Ceramic element touching the base of the burner.
Stove and burner must be level
If the oil burner is not level as oil enters for ignition it will flow away from the
igniter. This oil will build up until it finally reaches the igniter. This will result in long
ignition times and excessive oil at ignition.
Adjust the levelling feet in the legs of the stove.
Excessive oil will cause large flames, soot and very noisy operation.
Oil Metering Valve
The oil metering valve is set to give the correct flow rates before being fitted to the stove and will not normally require
further adjustment. Any but a small adjustment should be regarded as an indication of a fault of the fuel supply, or of
a flue system giving an incorrect negative pressure within the stove, and these should be examined thoroughly before
attempting to re-calibrate the oil metering valve.
The oil metering valve performs three operations within its main body; it regulates with a float valve the depth of oil
held, it meters with an adjustable outlet the fuel supplied to the burner, and its safety float valve will isolate the fuel
should the levels within the valve body become too high.
The safety float will cause the arming lever to “trip” whenever the fuel levels become too high, but
severe vibration
can cause ripples on the fuel surface to lift the float, and because of this it is possible for the vibration set up by heavy
passing traffic to shut off the valve.
Having “tripped”, resetting the arming lever may need to be done several times
before the fuel level within the valve falls sufficiently to allow reliable operation.
The firing rate of the burner is regulated by the oil metering valve and having set the extremes of low and high firing
as detailed in the commissioning instructions, the firing rates are proportioned as indicated by the indices 1-6 on the
valve top when aligned to by the control knob.
Most common problems
The oil control is a very reliable control system. If a problem with the oil flow is suspected it is very unlikely to be the
control valve.
The most common reason for poor flow rates will be air trapped within the oil supply pipe or the oil valve float control
stem. If an air lock is suspected the oil line should be disconnected from the oil valve and at least 1 litre of oil allowed
to flow after no air is present.
If an air lock is suspected in the oil control valve, remove the top plate mounting screws and press the float assembly
to the base of the oil control for 4-5 seconds, this will fully open the oil level inlet needle releasing trapped air.
Содержание Burgundy
Страница 13: ...Toby valve CI valve...
Страница 21: ...Fault Finding Flow Charts...
Страница 23: ...Dwyer 460 flue draught gauge recommended Flame burning only from inlet port...
Страница 25: ......
Страница 27: ...Service Record Year Date Company Engineer Tel No Parts replaced 1 2 3 4 5 6 7 8 9 10...