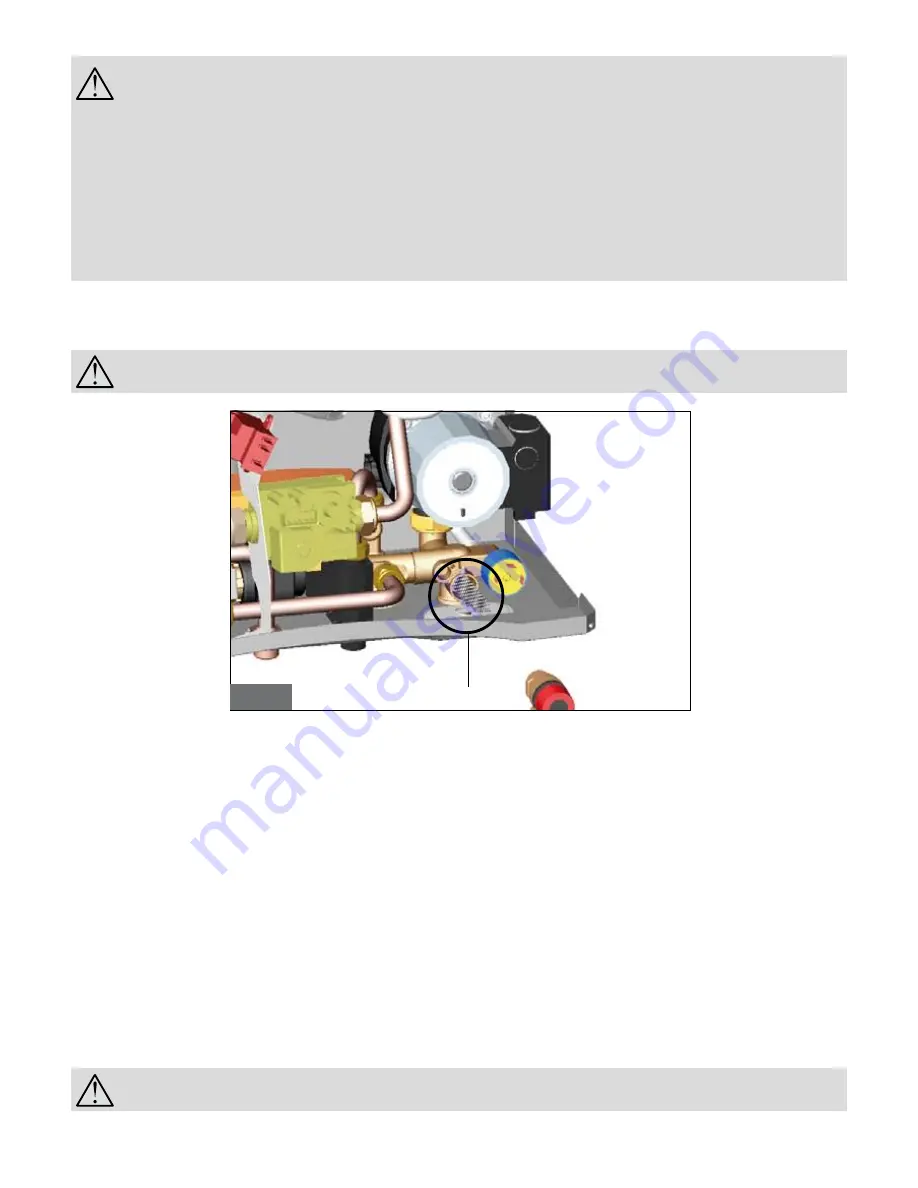
23
3.2.4.
Installing the boiler
Before connecting the boiler to CH and DHW networks, clean the pipes carefully.
Prior to operate a NEW system eliminate any metallic leftover during manufacturing and welding process, and any oil or
grease deposits, which might reach the boiler and damage it or alter its operation.
Prior to operate a MODERNIZED system (addition of radiators, boiler replacement, etc.), clean it throughout so as to remove
possible sludge and foreign particles.
In order to clean the system, employ non acid product available on the market. Do not use solvents as they could damage
system components.
Furthermore, in the central heating system (either new or modernized), it is always advisable to add to water, with adequate
concentration, suitable products inhibiting corrosion in multi-metal systems, which produce a protective film on internal
metal surfaces.
Manufacturer shall not be held responsible in case of harm to people and/or animals, or property damage due to failure in
adhering to the above stated instructions.
The boiler is fitted with a filter (fig. 11) whose function is to prevent the main heat exchanger pipes from obstructing, due to deposits that may form
in the heating system.
Such filter is not sufficient to prevent deposits of such materials to form inside the boiler. To this purpose, please note that:
For all boiler installation types, it is necessary to install a filter which can be inspected (Y-shaped type) with Ø 0.4mm-mesh
span, on the return pipe before the boiler.
In order to install the boiler proceed as follows:
• affix the template (fig. 10) to the wall;
• drill two 12 mm Ø holes in the wall to accommodate the boiler support bracket wall plugs;
• arrange air intake/flue gas system path in the wall as needed;
• secure boiler support bracket to the wall by means of the wall plugs supplied with the boiler;
• position gas supply network coupling
G
, water mains supply coupling
F
(KC and KR models),
RB
secondary return from the boiler (only KRB
model), DHW flow coupling
C
(only in KC model),
MB
secondary flow to the boiler (only KRB model), CH flow coupling
M
, and CH return coupling
R
, as shown on the template (refer to its lower area);
• provide a system for relieving condensates (S in fig. 10) and an outlet for the 3-bar safety valve (SV in fig. 6);
• position the boiler to the supporting bracket on the wall;
• connect the boiler to network pipes by means of the coupling kit supplied with the boiler (refer to 3.2.9. paragraph);
• connect the boiler to pipe for condensate discharge (refer to 3.2.9. paragraph);
• provide a system for relieving the 3-bar safety valves;
• connect the boiler to the air intake and flue gas exhaust system (refer to 3.2.6. paragraph and following);
• connect electric power supply, room thermostat (when available) and other available accessories (refer to the following paragraphs).
3.2.5.
Boiler room ventilation
The boiler has sealed combustion chamber. Combustion air is not drawn from boiler room, therefore specific recommendations need not to be
applied concerning the boiler room or openings and ventilation provided to the boiler room.
It is mandatory to install the boiler in an adequate room following laws and standards applicable in the country of
installation, which are considered as fully transcribed in this manual.
fig. 11
Filter
Содержание TAHITI CONDENSING IST 03 C 298 - 02
Страница 1: ...IST 03 C 298 02 INSTALLATION USE AND MAINTENANCE TAHITI CONDENSING GB...
Страница 22: ...22 fig 10...
Страница 42: ...42...
Страница 43: ...43...