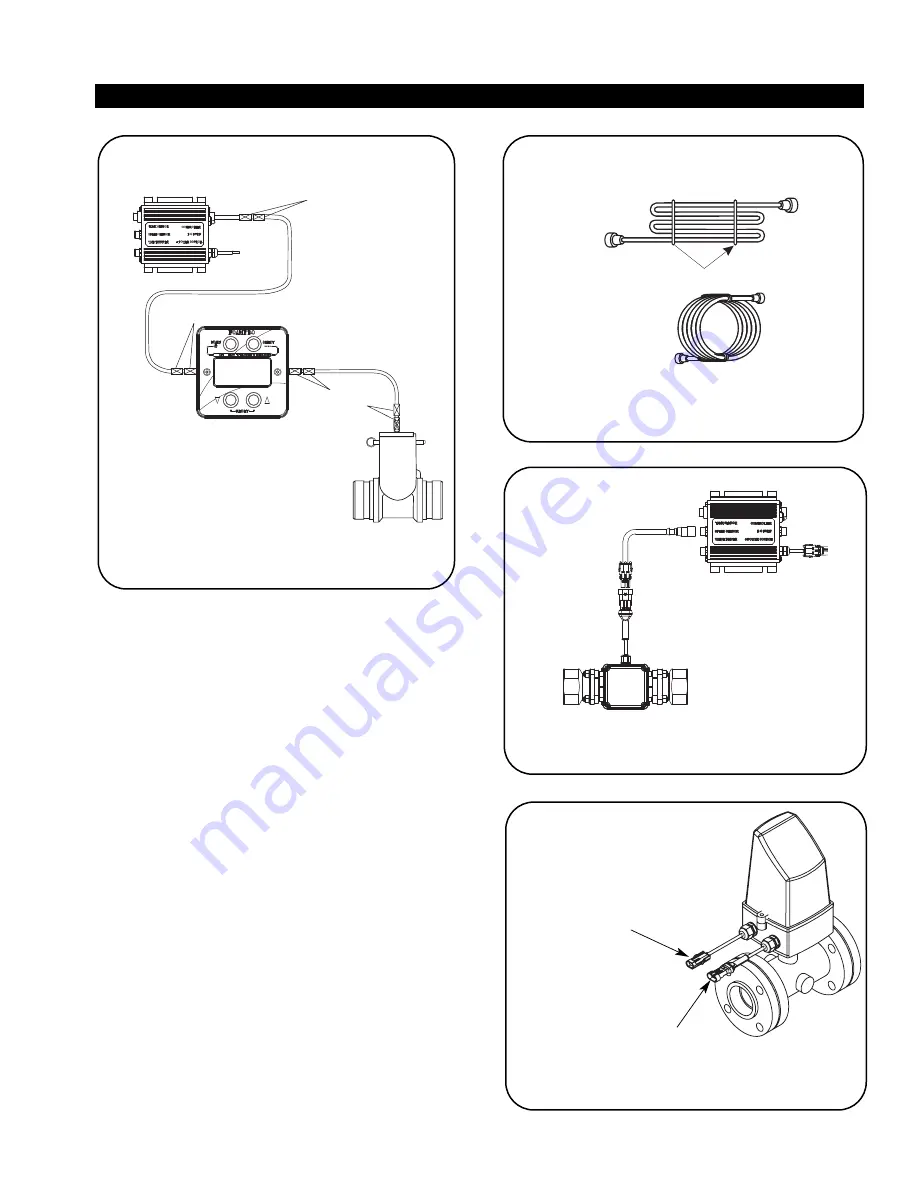
27
Installation and Operation Manual
AccuMax SP
Foam Discharge Flowmeters
The system foam flowmeters used on the AccuMax
single point systems are to be installed per the
instructions on page 21.
The electrical connections for the 3020 thru the 3150
systems are shown in Fig 9-9. The 3-pin molded end
connects to the hydraulic driver box in the “SPEED
SENSOR” position. The other end with the AMP
connector attaches to the flowmeter.
The connections for the foam flowmeter used on the
3300 system are shown in Fig 9-10. The 3-pin molded
end connects to the hydraulic driver box in the
“SPEED SENSOR” position. The other end with the
AMP connector attaches to the flowmeter. This foam
flowmeter will also need a separate power and ground
line that will connect with the 2-pin Weatherpak
connector as shown in Fig 9-10. The wiring on the
power connection is: PIN A to + power, PIN B to
ground. Be sure to install a 5 amp fuse to the + power
supply.
Figure 9-7 RFI/EMI Bead Installation
Figure 9-8 Extra Cable Storage
Hydraulic Motor-Driven
Foam Pump Driver Box
Large
Beads
Large
Beads
Control
Cable
Control
Cable
Flowmeter
Cable
Small
Beads
Flowmeter
Digital Display
Control Module
Modular Cable
Modular Cable
Wire Ties
DO
DON’T
Figure 9-9 3020 thru 3150 Foam Flowmeter
Connections
Figure 9-10 3300 Foam Flowmeter Connections
2-pin Weatherpak
connector for power and
ground.
Pin A + 12 or 24 VDC
Pin B Ground
3-pin AMP connector for
connection to driver box