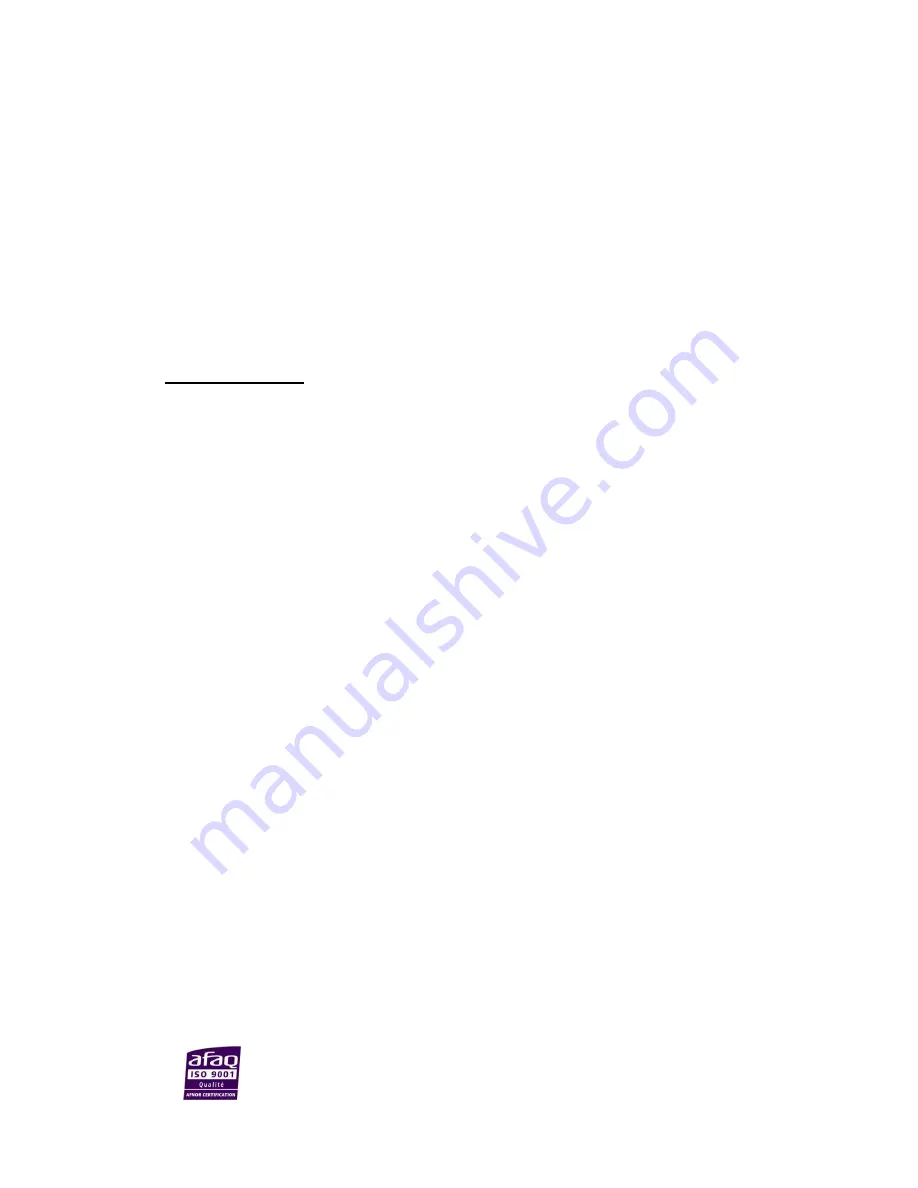
Page - 20
FLUIGENT
Siège social : Biopark
–
1 mail du Professeur Georges Mathé
–
94800 Villejuif
–
France
Tel : +331 77 01 82 68
–
Fax : +331 77 01 82 70
www.fluigent.com
SA à Directoire et Conseil de Surveillance au capital de 141 284.95
€
- Siret : 487 636 409 00038
–
N°TVA UE/EU VAT Number : FR 53 487 636 409
7.1.5
Cleaning Methods that are not recommended
In general,
any cleaning by mechanical means should be avoided
. Never
e ter the se sor’s flo path ith
sharp objects that could scratch the glass surface.
Furthermore, no abrasives or liquids containing solids that can grind the surface clean should be used. Anything
that affects the glass wall will cause deviations in the measurement performance or permanently damage the
sensor.
Strong acids and bases should also not be used to clean the sensor
. Acids can sometimes be used in low
concentration and at low temperatures. Before using the acid check how compatible it is with borosilicate 3.3
glass (Pyrex® or Duran®).
.
8.
Dual calibration
8.1
Principle of single and dual calibration
The different FLOW UNIT models are calibrated to provide an accurate reading when used with the
corresponding fluid, water or isopropyl alcohol.
For the FLOW UNIT models XS/XL, only one single calibration for water is available. For the FLOW UNIT models
S/M/L, two calibrations are available: Water and Isopropyl alcohol.
The FLOW UNIT can be used to handle different fluids not originally calibrated for. When possible, select a
standard calibration field that most closely matches your fluid. For example, water calibration can be used for
water based solution and isopropyl alcohol calibration for hydrocarbons or oil. The calibration can be selected
and switched in the software (see the corresponding user manual).
In order to obtain accurate flow-rates for alternative fluids, it is necessary to use correction factors (scale
factor), to convert the displayed value into the actual value. The scale factor can be added in the software (see
Custom scale factor in the corresponding user manual). Adding the scale factor ensures that the flow sensor
reading is now accurate for the target fluid.
The following section explains how you can calculate this scale factor and shows an example with a fluorinated
oil: FC-40.
8.2
Example of calibration: FC-40
A method for providing a known flow-rate is required to work out the scale factor for the selected fluid. This
could be a syringe pump, a peristaltic pump or a pressure regulator delivering fluid onto a precision balance
with volume calculated from known density.
Here is an example using MFCS
TM
-EZ, a fast and stable pressure-based flow controller delivered by FLUIGENT.
The aim of this FASTAB
TM
technology is to pressurize a reservoir containing the fluid of interest to be injected
through the microfluidic system. For more information about the MFCS
TM
-EZ, please visit us at
www.fluigent.com.