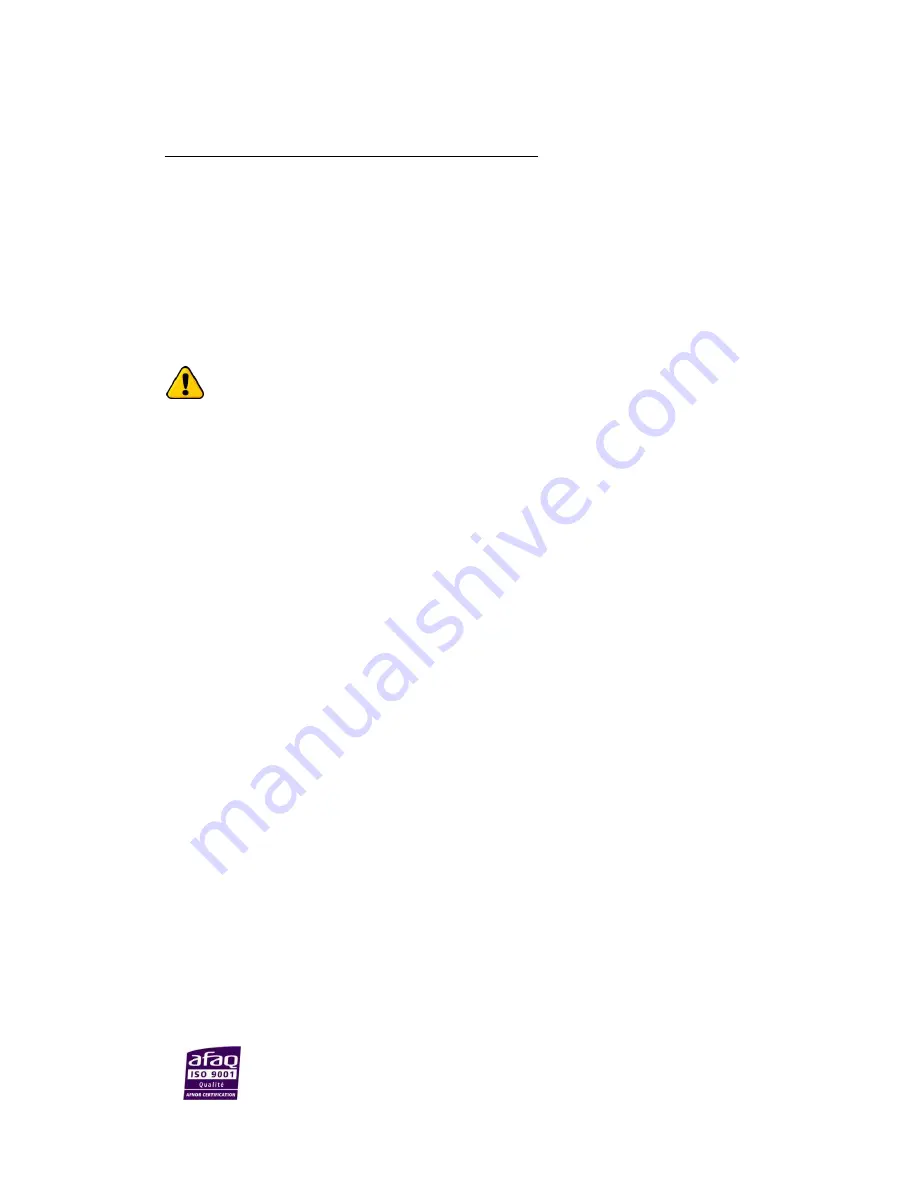
Page - 16
FLUIGENT
Siège social : Biopark
–
1 mail du Professeur Georges Mathé
–
94800 Villejuif
–
France
Tel : +331 77 01 82 68
–
Fax : +331 77 01 82 70
www.fluigent.com
SA à Directoire et Conseil de Surveillance au capital de 141 284.95
€
- Siret : 487 636 409 00038
–
N°TVA UE/EU VAT Number : FR 53 487 636 409
6.
Start working with the Flow-Rate Platform
6.1
Quick start procedure
Here is a quick setup guide to remind you the main steps to get your Flow-Rate Platform up and running.
1.
First, you may want to integrate the different FLOW UNIT to your microfluidic system, with the right
fittings. See §4.2 how to do it.
2.
Then, connect the FLOW UNIT models to the FLOWBOARD. See §5.2 how to do it.
3.
Then connect the FLOWBOARD and the computer with the USB cable. See §5.2 how to do it.
4.
To finish start the software (FRP SFP or MAESFLO) installed on your computer (user manual)
You can now use your Flow-Rate Platform for your application.
DO NOT FORGET TO CLEAN AND RINSE YOUR FLOW UNIT AFTER USE
(See §7 how to do it.)
6.2
Use at high temperature and high flow-rate
The Flow Units can be used in a large range of temperature, but some elements need to be taken into account:
-
The Flow Units include temperature compensation between 10°C and 50°C. However, as the
temperature deviates from 20°C, the absolute accuracy may acquire an additional error of
typically 0.1% of the measured flow rate per °C.
For example the L Flow Unit model at 50°C has a specified error of 5% + 30*0.1% = 8% of the
measured value.
-
Between 50°C and 80°C the Flow Unit will still be operational and the repeatability will still be
excellent. However, we give no more guarantee for the absolute accuracy of the calibration.
In order to get a correct reading from the sensor, it is crucial to have the liquid temperature and ambient
temperature the same (within ± 3°C). At low flow rates this
o ’t e a
problem, because the liquid adapts to
the ambient temperature very quickly. At higher flow rates (for L and XL Flow Unit models) this is important.
6.3
Use a XL Flow Unit
The o i atio of differe t para eters a lead to u a ted eha iors a d surprisi g easure e ts. It’s
related to the formation of localized vortex and arise from a combination of the following facts:
-
The decreased viscosity of liquid at elevated temperatures (for example for water at 40°C the viscosity
is about half the one at 20°C)
-
The combination of small ID tubing (for example 500 µm ID tubing) with the 1.8 mm ID sensor.
The transition from the small ID tube to the larger ID sensor may lead to a jet at high flow speeds and low
viscosity, see the following sketch. Such a jet is inherently unstable, which can lead to strong fluctuations at
high flow-rates and temperatures. The phenomenon is also strongly dependent on the exact geometry of the
arrangement. A bending of the tube on the inlet side may generate a stationary vortex and the fluid in
proximity to the sensor chip may actually be flowing backward, see the next sketch: