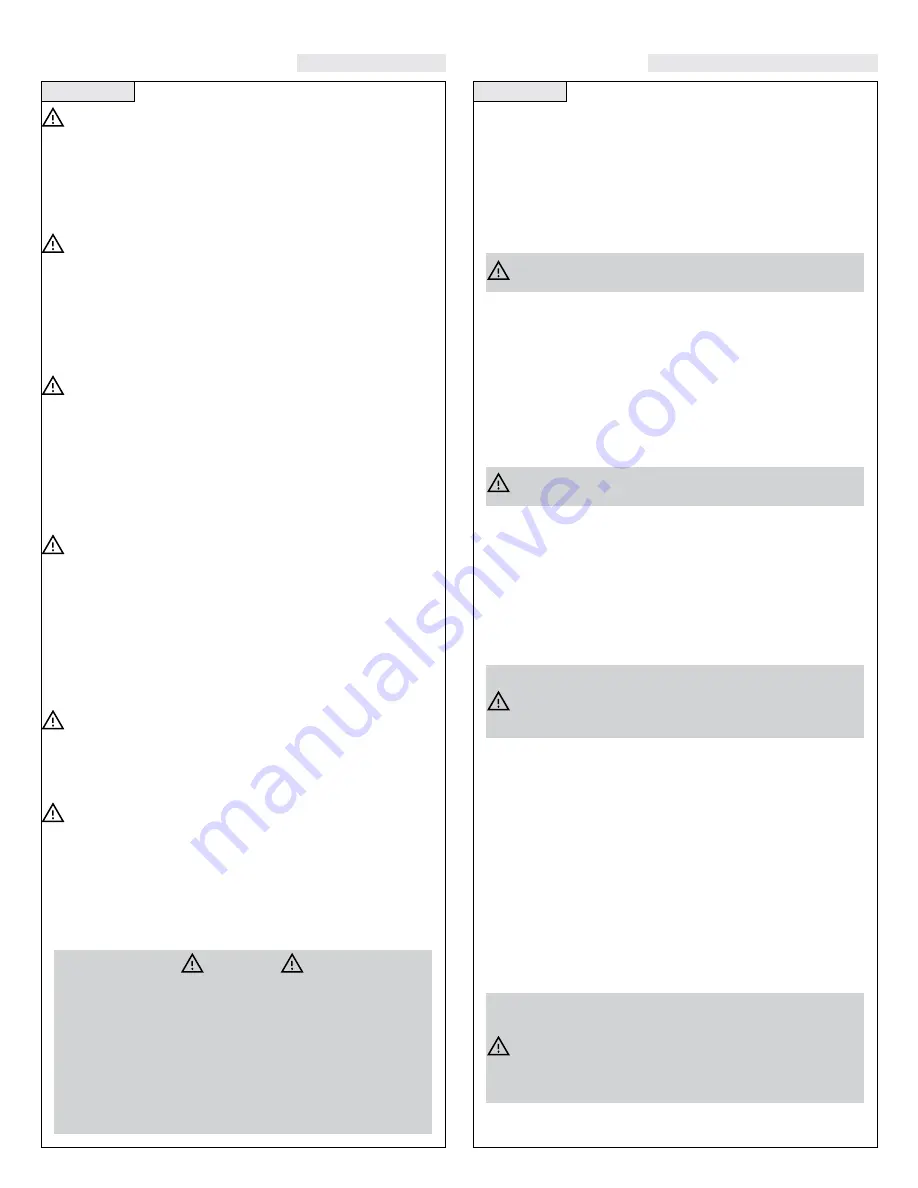
Step Three
Step Four
SAFETY PRECAUTIONS
INTRODUCTION
About this Manual:
PLEASE READ THE ENTIRE MANUAL PRIOR TO
INSTALLING OR USING THIS PRODUCT. This manual
includes information on all models of Flowline Switch-Tek™
Powered Level Switches: LZ12, LU10, LP15, LP10 and LO10
series. Please refer to the part number located on the switch label
to verify the exact model which you have purchased.
User’s Responsibility for Safety:
Flowline manufactures a wide range of liquid level sensors and
technologies. While each of these sensors is designed to operate in
a wide variety of applications, it is the user’s responsibility to select
a sensor model that is appropriate for the application, install it
properly, perform tests of the installed system, and maintain all
components. The failure to do so could result in property damage
or serious injury.
Proper Installation and Handling:
Because this is an electrically operated device, only properly-
trained staff should install and/or repair this product. Use a proper
sealant with all installations.
Note: Always install the 3/4” Viton
gasket with all versions of Switch-Tek™ with metric threads. The
G threaded version will not seal unless the gasket is properly
installed.
Never overtighten the sensor within the fitting, beyond a
maximum of 80 inch-pounds torque. Always check for leaks prior
to system start-up.
Material Compatibility:
The LU10, LP10 and LO10 series sensors are available in two different
wetted materials. Models L_10-1__5 are made of Polypropylene(PP).
Models L_10-2__5 are made of Perfluoroalkoxy(PFA). The LZ12
series is made of made of Ryton® (40% glass filled) and the LP15
series is made of PP. Make sure that the model you have selected is
compatible with the application liquid. To determine the chemical
compatibility between the sensor and its application liquids, refer to an
industry reference such as the Compass Corrosion Guide (available
from Compass Publications, phone 858-589-9636).
Wiring and Electrical:
The supply voltage used to power the sensor should never exceed
a maximum of 36 volts DC
(30 VDC for LZ12 series)
. Electrical
wiring of the sensor should be performed in accordance with all
applicable national, state, and local codes.
Flammable, Explosive and Hazardous Applications:
Only the LU10-___5 series switch is rated for use in hazardous
locations. Refer to the Certificate of Compliance for all applicable
intrinsically safe ratings and entity parameters. Refer to the
National Electric Code (NEC) for all applicable installation
requirements in hazardous locations. DO NOT USE THE LZ12,
LP15, LP10 OR LO10 SERIES GENERAL PURPOSE SWITCH
IN HAZARDOUS LOCATIONS.
WARNING
The rating for the relay is 60 VA.
Flowline’s Switch-Tek™ level switches are not recommended
for use with electrically charged application liquids. For most
reliable operation, the liquid being measured may need to be
electrically grounded.
Always install the 3/4” Viton gasket with all versions of the
powered sensors with metric threads. The G threaded version
will not seal unless the gasket is installed properly.
Vibration Switch:
The Tuning Fork vibration switch operates at a nominal frequency of
400 Hz. As the switch becomes immersed in a liquid or slurry, a cor-
responding frequency shift occurs. When the measured frequency
shift reaches the set point value, the switch changes state indicating
the presence of a liquid or slurry medium. For optimum performance
and proactive maintenance, the sensor automatically adjusts for coat-
ing, and if necessary, outputs a preventative maintenance alarm.
Do not squeeze the forks together. Doing so could damage
or break the sensor and void the warranty.
When powering up the LZ12, the start-up procedure requires the
switch to cycle through a wet condition for 1/2 second in order to
determine an initial resonance.
Ultrasonic Switch:
The Ultrasonic level switch generates a 1.5 MHz ultrasonic wave
from a miniature piezoelectric transducer located on one side of the
gap in its sensing tip. Another piezo transducer located on the other
side of the gap acts as a microphone, picking up the sound. When
liquid enters the gap in the sensing tip, the audio level changes.
The sensor should be installed so that the liquid will drip out
of the gap when the sensor becomes dry.
Optic Switch:
The Optic Leak Detector use principles of optical refraction to detect
the presence or absence of fluid. A pulsed infrared light beam is
internally generated by a light emitting diode and aimed at the slanted
optical tip of the sensor. If the tip is dry, the light beam bounces at a
90 degree angle to a receiving photo transistor, indicating a dry condi-
tion. If the tip is immersed in liquid, the light beam will refract out
into the liquid instead of being reflected to the photo transistor, indi-
cating a wet condition.
The Optic Leak Detector can not detect the presence or
absence of specular application liquids that reflect light
(such as milk), or viscous liquids (such as paint) that form a
coating on the sensor tip.
SuperGuard Capacitance Switch:
The SuperGuard level switch generates a pulse-wave radio frequency
signal from the capacitance electrode located in the sensing tip of
each sensor. When liquid comes into contact with the sensing tip, the
capacitance as measured by the sensor changes based on the dielectric
constant of the liquid. The guard circuit rejects the negative effects of
coating buildup on the probe by eliminating the coating signal path
between the active and reference electrodes.
Intrusive RF Capacitance Switch:
The Intrusive RF Capacitance level switch generates a 300 kHz pulse-
wave radio frequency signal from the capacitance electrode located in
the sensing tip of each sensor. When liquid comes into contact with
the sensing tip, the capacitance as measured by the sensor changes
based on the dielectric constant of the liquid.
The sensor’s operation may vary based on the dielectric
properties of various application liquids. The LP15 & LP10
series sensor is factory-calibrated to be used with liquids
with a dielectric value between 20 and 80. Liquids with a
dielectric constant less than 20 will not be detected by
an LP15 & LP10 series sensor, as factory calibrated.
Spec Tech Industrial Electric www.spectechind.com
888-773-2832
Spec Tech Industrial Electric www.spectechind.com
888-773-2832