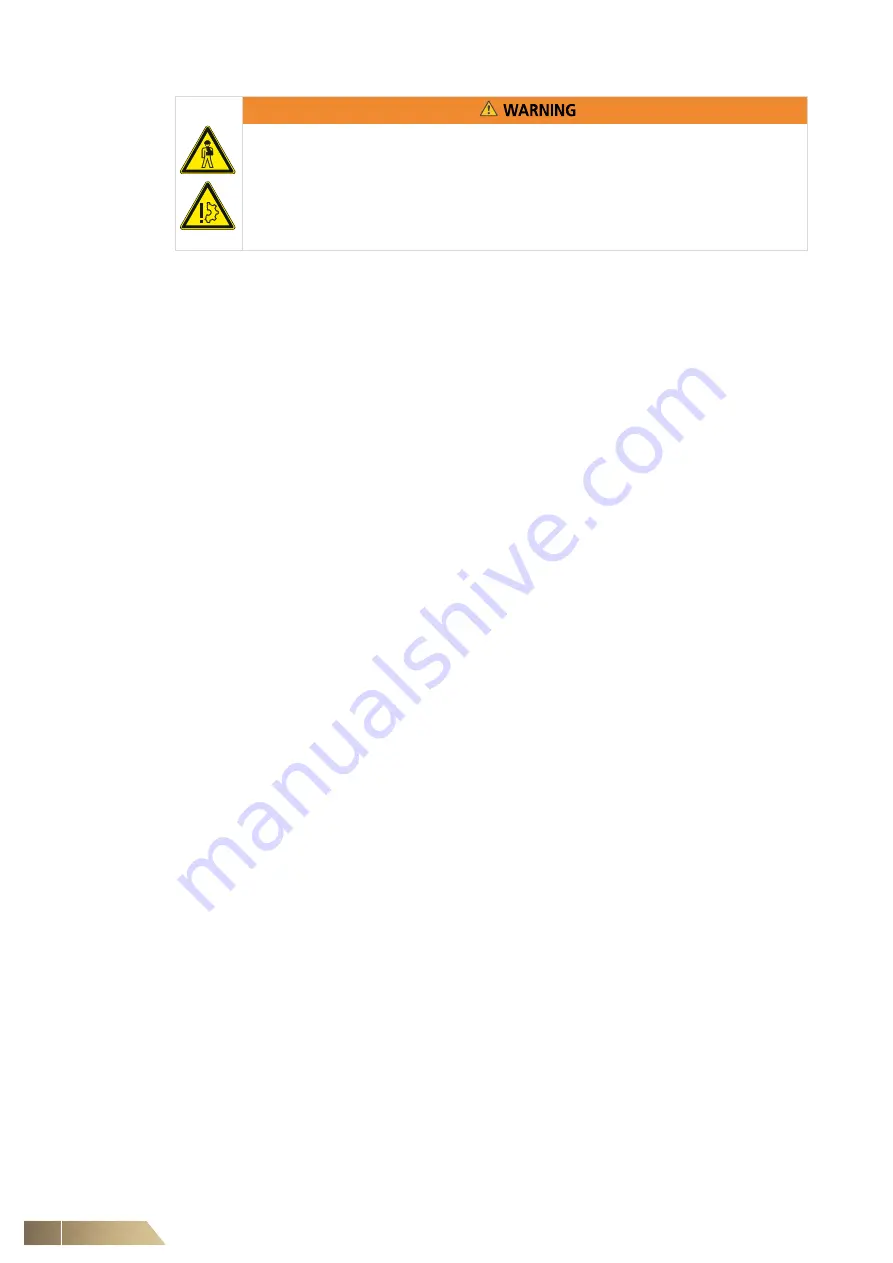
Safety and User Instructions
Row
-DENCO
20
FläktGroup DC-2014-0106-GB 2019-02/R3 • Subject to modifications
4.8
Safety devices
Depending on the unit equipment, the following components are secured:
– Padlock in the door-stop device (TAS) on each door
– Locks of switch cabinet
– The panels and doors with lockable handles
– Fan chambers are secured by door protection grilles
– V-belt drives are secured by belt guards
Ensure by others on site that the contact protection for intake and discharge fittings is
provided.
4.9
Modifications and changes
Changes, alterations or modifications of the unit are not allowed. Tampering with the
unit or its misapplication will invalidate the CE conformity and void warranty.
If delivered units are disassembled by others on-site, the factory warranty is rendered
invalid. In this case professional services by FläktGroup should be arranged in
advance.
4.10 Spare parts
Only original FläktGroup spare parts are allowed, since FläktGroup is not liable if third-
party spare parts are used.
4.11 Disposal
Equipment, operating supply materials, components and filters must be disposed of
according to the material type in a safe and environmentally friendly manner.
4.12 Selection and qualification of personnel
Ensure that every person working on the unit has read and understood entire operation
manual. Please read this document fully before commencing any work, and not while
performing a task.
All jobs must only be carried out by qualified licensed staff or other individuals with
proper professional training and experience in the following areas:
– Occupational health and safety regulations
– Accident prevention regulations
– Directives and recognized codes of practice
All jobs with the refrigeration circuit shall be performed only by certified and licensed
staff in accordance with the valid EG Regulation 842/2006 Article 5, EG Regulation
303/2008 Article 4 and 5 as well as "Ordinance on climate protection against changes
caused by release of certain fluorinated greenhouse gases" Article 5, passed by the
German parliament.
All skilled staff must be able to assess the entrusted work and must be able to recog-
nize and avoid all associated dangers.
Personal Injury and Damage to the Unit!
It is not allowed to operate FläktGroup units:
– in areas subject to explosion risk
– in environments with strong electromagnetic fields
– in environments with high levels of air contamination
– in environments with corrosive and/or aggressive air
Содержание Row-DENCO DRC 020
Страница 1: ...Row DENCO OPERATION MANUAL ...