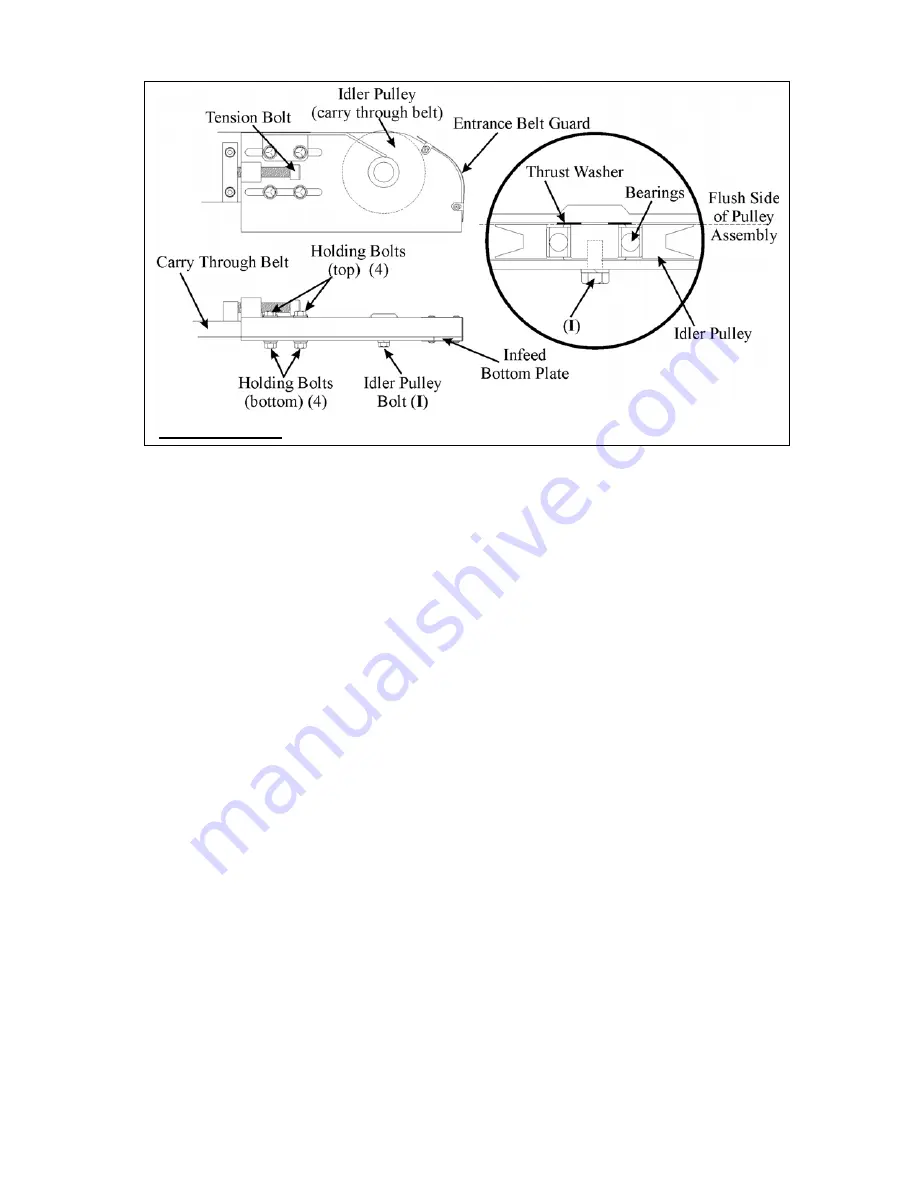
FISCHBEIN
®
Co. MODEL PBC-6000™
OPERATOR’S MANUAL
REV. D 2005-03
40
4.
Loosen, but do not remove, the four top holding bolts and four bottom holding bolts for the
fixed and swing channel infeeds.
5.
Turn the tension bolt to reduce the tension in the carry through belts.
6.
Remove the four bottom holding bolts from the fixed and swing channel infeeds.
7.
Remove the idler pulley bolt (
I
) from the bottom of the infeeds. The infeed bottom plate can
now be removed from the assembly.
8.
Turn the tension bolt enough to remove the carry through belt.
9.
Carefully remove the pulley from its shaft. Be sure to remove the old thrust washer from
between the pulley and the top plate of the infeed.
10. The new pulley comes with the bearing presses in place and a thrust washer. Install the thrust
washer on the shaft first.
11. Install the pulley on the shaft with the flat (flush) side against the thrust washer (up). The
bearing is pressed into the pulley so that it is flush with the pulley surface on one side and
extending beyond the face of the pulley (slightly) on the other side. If the pulley is not
installed correctly, the pulley will rub against the infeed plates.
12. Put the carry through belt on the pulley and turn the tension bolt enough to hold the belt on
the pulley.
13. Install the infeed bottom plate using the four bottom holding bolts and the idler pulley bolt
(
I
). The holding bolts should hold the plate in position and allow the infeed assembly to
move. The idler pulley bolt (
I
) can be tightened, but not so much to prevent the pulley from
freely rotating.
Illustration 8.16
Содержание PBC-6000
Страница 69: ...FISCHBEIN Co MODEL PBC 6000 OPERATOR S MANUAL REV D 2005 03 72 this page left blank...
Страница 71: ...FISCHBEIN Co MODEL PBC 6000 OPERATOR S MANUAL REV D 2005 03 75 this page left blank...
Страница 73: ...FISCHBEIN Co MODEL PBC 6000 OPERATOR S MANUAL REV D 2005 03 78 this page left blank...
Страница 75: ...FISCHBEIN Co MODEL PBC 6000 OPERATOR S MANUAL REV D 2005 03 81 this page left blank...
Страница 77: ...FISCHBEIN Co MODEL PBC 6000 OPERATOR S MANUAL REV D 2005 03 84 this page left blank...
Страница 79: ...FISCHBEIN Co MODEL PBC 6000 OPERATOR S MANUAL REV D 2005 03 87 this page left blank...
Страница 81: ...FISCHBEIN Co MODEL PBC 6000 OPERATOR S MANUAL REV D 2005 03 90 this page left blank...