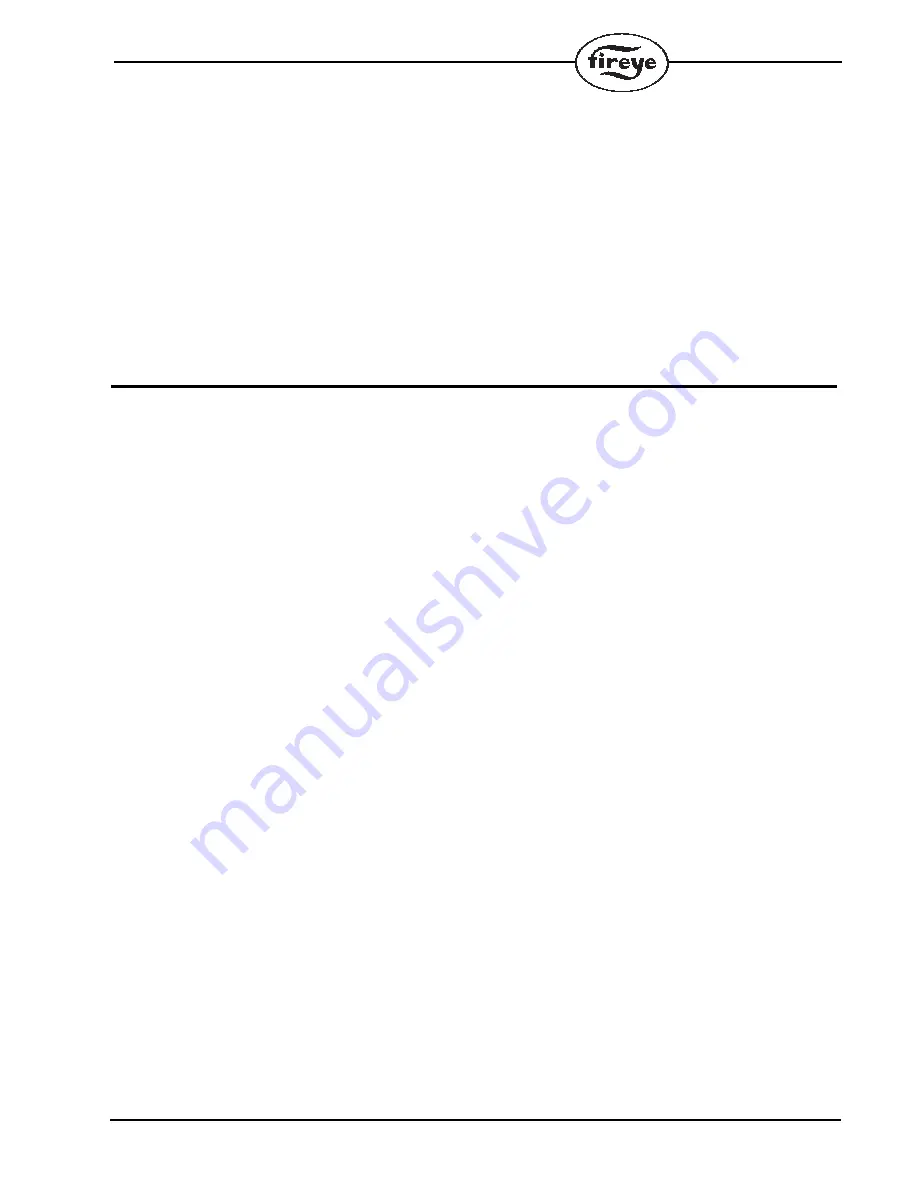
15
®
3.
Fuel Valve End Switch Interlock
: This is generally an integral switch mounted on the main
fuel valve and activated by the valve stem. It is connected between Terminal 3 & 13. The fuel
valve end switch interlock prevents a burner start-up if the valve stem is not in the “valve
closed” position.
4.
Purge Interlock
: Generally a firing rate motor linkage position switch or a differential air-pres-
sure switch, that proves a maximum purge air flow rate. It is connected between Terminals D
and 8. The purge interlock proves that the purge air flow rate is at maximum during the purge.
5.
Running Interlocks
: These generally are air flow switches, high and low fuel pressure
switches, oil temperature switches, atomizing media pressure switches, and excess smoke den-
sity controls. These interlocks prove proper conditions for normal operation of the burner. They
are wired in series and connected between Terminals 3 and P.
6.
Low Fire Start Interlock
: Generally a firing rate motor linkage position switch or a damper
position switch, will prove both the linkage and dampers are in their proper positions to begin
burner light off. This switch is connected between Terminals M and D.
IMPORTANT INFORMATION — PLEASE READ CAREFULLY
DETECTING AIR FLOW SWITCH (3-P) CLOSED AFTER START
In code 39 programmers and above, the method used to detect the air flow switch closed at the
beginning of a cycle has been changed to avoid any nuisance lockouts. Currently, after the operating
control closes, the programmer waits 10 seconds for the air flow switch to close and if not closed
will go into lockout. The EP programmers utilize the open damper switch interlock, D-8, to deter-
mine the wait time for the air flow switch to close. If, at the start of a cycle after a blower turns on,
the D-8 interlock is detected as closed, most likely indicating a jumped high fire switch, the pro-
grammer allows 20 seconds for the air flow switch to close. Alternatively, at startup, if the D-8 inter-
lock is open, indicating the firing rate motor is at the low fire position and the damper is closed, the
programmer will not check for the air flow switch closed until 10 seconds after the open damper
switch has closed and the purge period has begun. This means the programmer will send the mod
motor to the high fire position, forcing the high fire damper switch to close, and will then begin its
10 second timer to check for the air flow switch to close.
EP160 - DIP SWITCH 1
When used in conjunction with Nexus PPC5000, dip switch 1 in the UP position provides a 3 second
delay between burner cycles. This time period is used to de-energize the blower motor, terminal M.
This allows sufficient time for the PPC5000 to realize a new cycle is beginning and it can reset its
operating parameters accordingly.
Refer to the specific programming bulletin for additional information regarding dip switch settings.