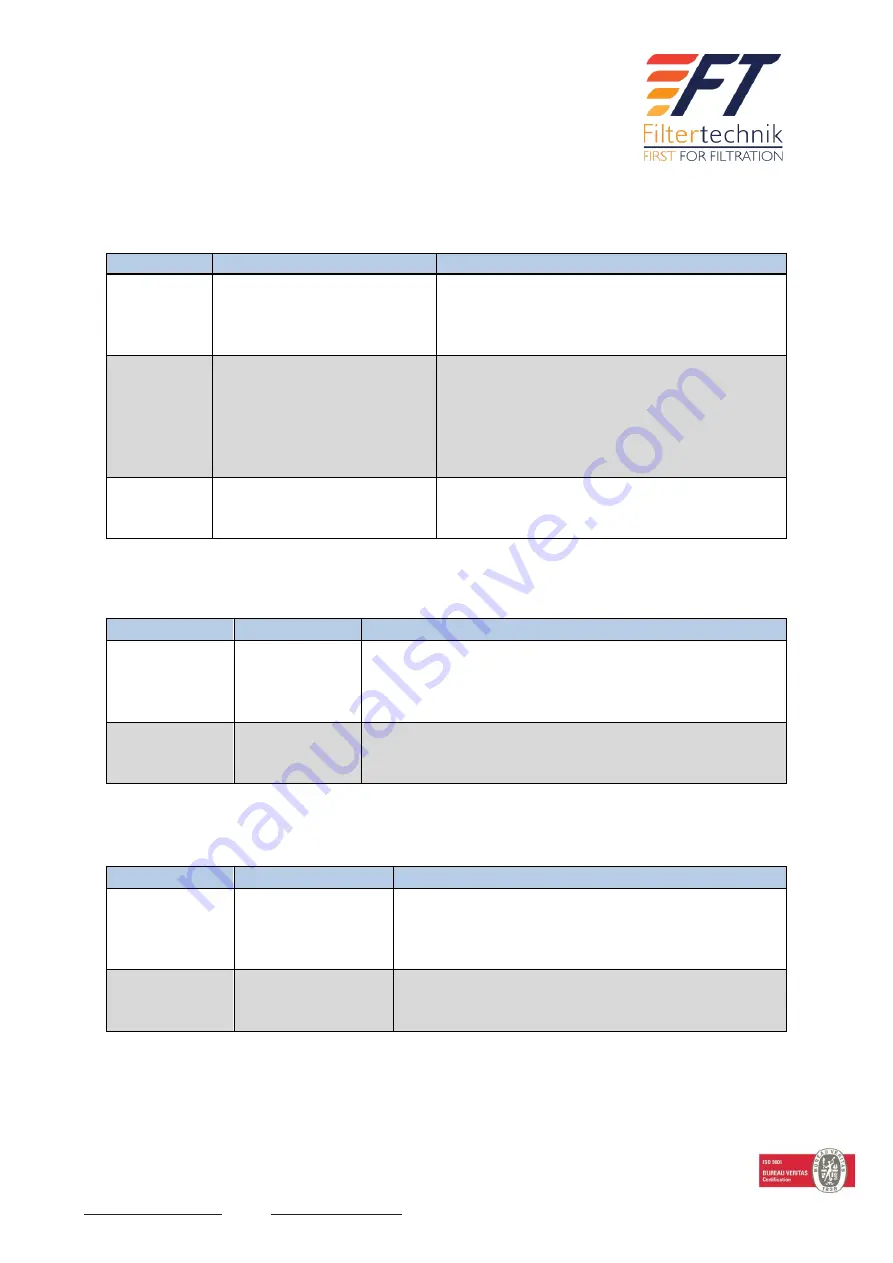
Fax:
+44 (0)115 986 8875
Web:
Tel:
+44 (0)115 9003 600
Filtertechnik
1 Central Park, Lenton Lane, Nottingham, NG7 2NR
Registered in England No: 03969985 VAT No: 760 821 731
Certification No. UK002838
20 of 26
Troubleshooting
General Operational Errors
Problem
Possible Cause
Solution
Unit will not
switch on.
Fully discharged battery.
Connect to the mains and fully charge the unit.
If the LED switches still fail to illuminate there
could be an electrical fault or damage to the
battery pack from over discharge.
Unit will not
prime.
Internal tubing/pump gears
are dry.
High viscosity fluids.
Restriction in the
suction/discharge lines.
Go into the settings for priming to increase the
pump speed.
Raise the height of the fluid sample to gravity
assist, or create a vacuum using a hand operated
thief pump to pull fluid through.
Check the hoses and strainer for blockages.
Screen is
behaving
erratically.
Dirt on the screen or hands.
Wipe the screen clean to remove traces of dirt or
oil. In most cases gloves will not work with the
touch screen.
Particle Counting
Problem
Possible Cause
Solution
Contamination
codes dropped
to near zero
A blockage in
the flow path
Check there is adequate flow going through the unit
(approximately 20-100ml/min)
Check/clean the suction strainer for any contamination
Erratic count
levels
Unstable
sample
Check for the presence of air. Bubble counts should be
maintained below 200 bubbles/ml in each channel.
RH & Water Content
Problem
Possible Cause
Solution
Water content
is above 95%
High moisture levels
in the sample.
Damaged moisture
sensor.
Flush the unit immediately with dry oil to avoid damage
to the moisture sensor. If levels still don’t fall the sensor
could be permanently damaged.
Water content
bouncing from
near 0 to 100%
Damaged moisture
sensor.
Permanent damaged due to excessive moisture. Sensor
will require replacing.