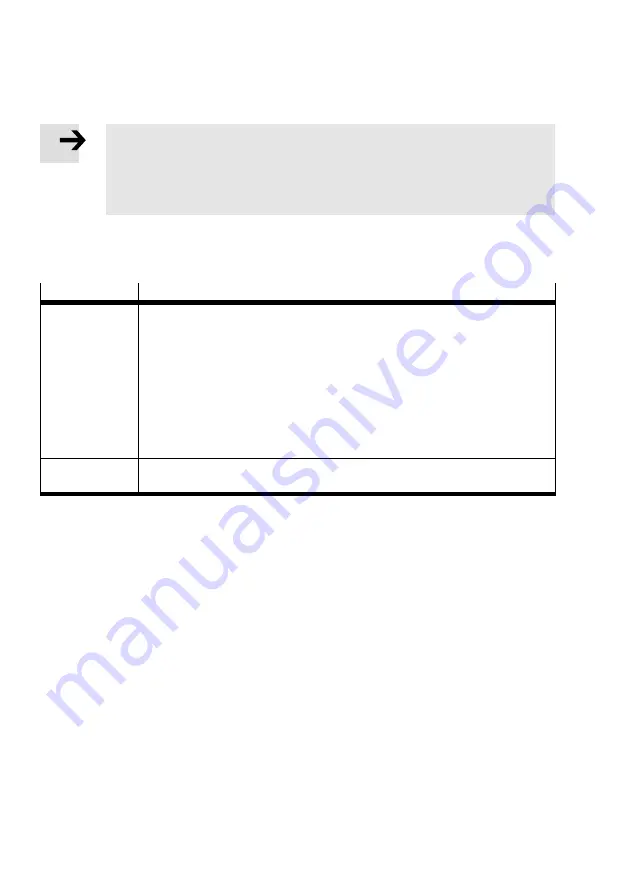
2
Overview
22
Festo – EXCM-10/-30-...-E-EN – 1612b – English
2.10
Emergency stop concept
Note
As part of your emergency stop concept, check which measures are required for
your machine/system in case of an emergency stop.
Observe the contents of this documentation on the switch-off functions
(
è
If an emergency stop circuit is necessary, use additional, separated safety limit switches (e.g. as
normally closed contacts in a series circuit).
Note the following aspects:
Action
Behaviour
Removal of the
ENABLE signal
–
Without brake/clamping unit:
The drive brakes with the quick stop edge (Quick Stop). Then the controller
end stage is switched off.
–
If a brake/clamping unit is used:
If the drive moves when ENABLE is removed, it is first brought to rest with the
stop delay. As soon as the drive has come to a rest, the brake output is reset:
the brake/clamping unit closes. Simultaneously, the switch-off delay time
begins to run. The controller continues to control the position. Then the con
troller end stage is switched off after the switch-off delay.
Switching off the
load voltage
The load voltage is switched off. The effective load on the drive may continue to
move due to inertia, or it will fall if mounted in a vertical or sloping position.