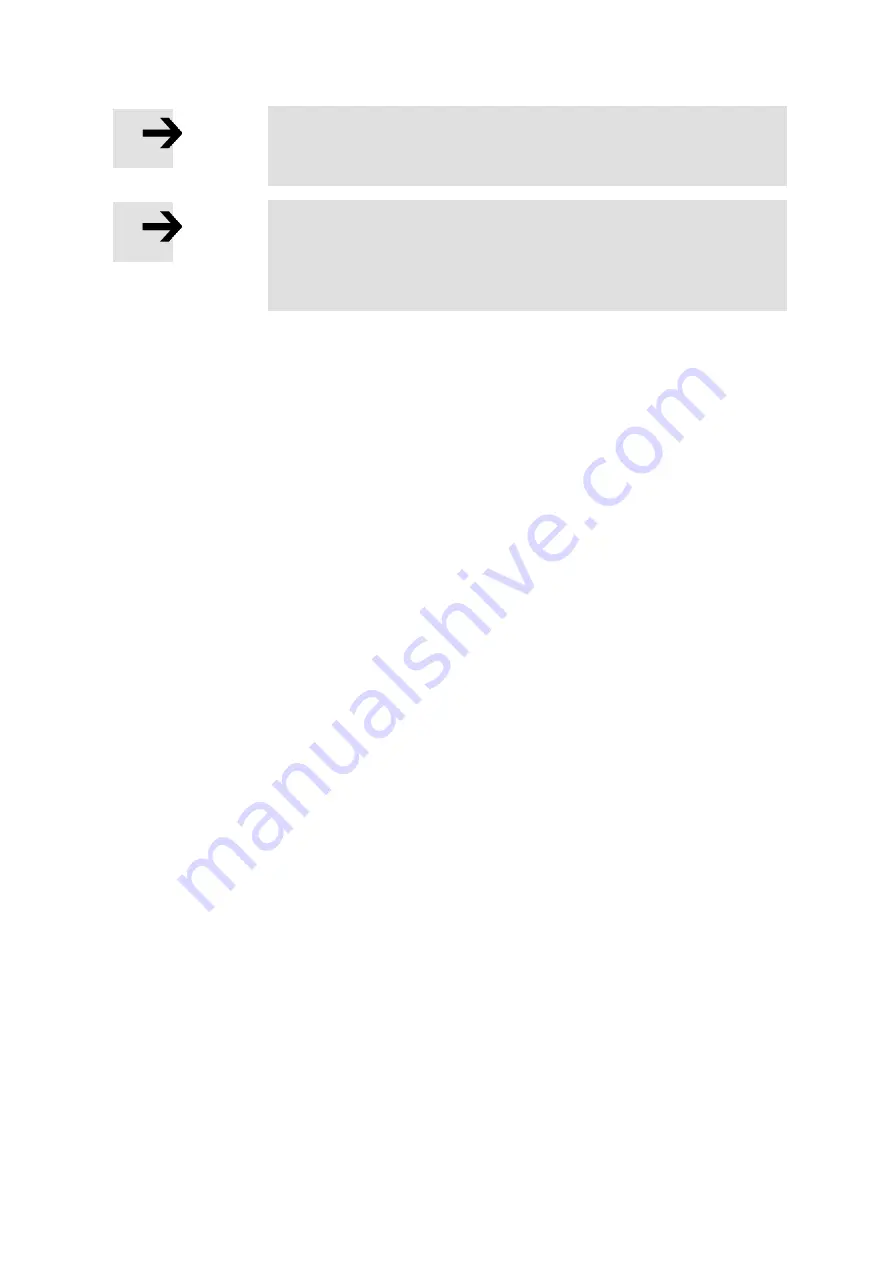
4. Functional safety engineering
Festo P.BE-CMMD-AS-HW-EN 1002NH
95
Note
The holding brake of the EMMS-AS-…-RS
B
/-RM
B
is not suitable for
braking the motor and does not have a safety function.
Note
The time delay of the PNOZ relay must be adjusted for the
application (see chapter 4.3.10). If this time delay is set too low,
the drive performs an STO function when the time has passed and
the brake will be worn.
4.3.8
Restoration of normal operation
Before switching it on again, make sure that all hazards have been eliminated and the
system can be safely placed in operation again. If there are areas inside that can be
entered, a manual acknowledgement must be made via the optional S2 button.
4.3.9
Testing the safety function
For each on-off cycle of the machine, the PILZ device PNOZ XV2P checks whether the
relays of the safety equipment open and close properly. The function of switching off the
output stage enable and controller enable must be checked regularly (e.g. monthly) via
the PLC. In addition, the "Acknowledgment of driver supply" signal must be checked for
plausibility.
4.3.10
Determination of the brake time
The brake time can easily be determined through the FCT Trace function. The brake time
can vary greatly due to different loads. Determine the values for the maximum brake time.
Содержание CMMD-AS series
Страница 2: ......
Страница 75: ...3 Product description Festo P BE CMMD AS HW EN 1002NH 75 For linear axes For rotational axes ...
Страница 91: ...4 Functional safety engineering Festo P BE CMMD AS HW EN 1002NH 91 4 3 5 Parameterization example FCT ...
Страница 93: ...4 Functional safety engineering Festo P BE CMMD AS HW EN 1002NH 93 4711d_21 Fig 4 8 Sample circuit SS1 CMMD AS ...
Страница 99: ...5 Mechanical installation Festo P BE CMMD AS HW EN 1002NH 99 Fig 5 2 Motor controller CMMD AS Mounting ...