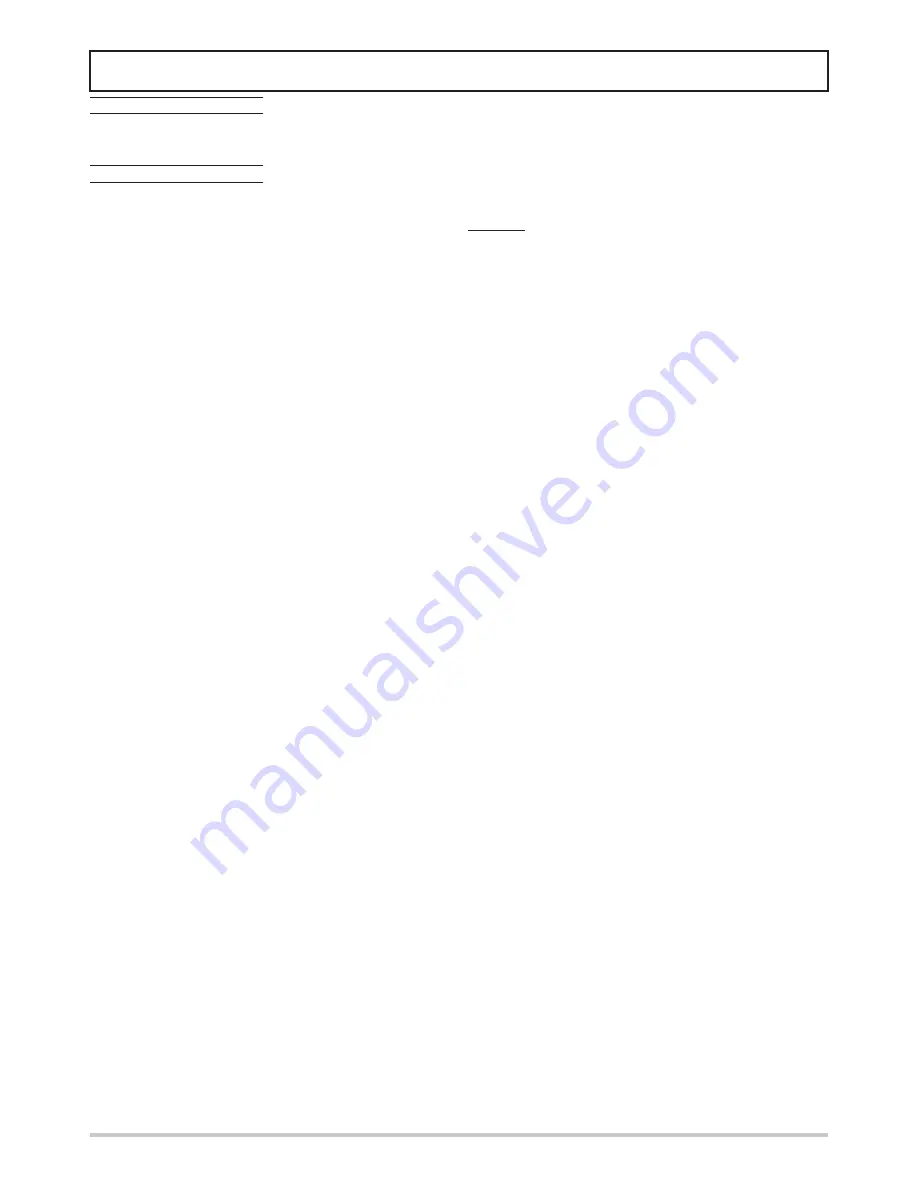
42
START UP
START-UP
General Rules
The following operations must be carried out only by properly trained personnel. To make the
contractual warranty
effective, start up
must be carried out by autho-
rized service centres
.
Before calling the service centre it is advisable to make sure that all the installation steps have been completed (positioning, electrical connections, hydraulic connections).
Preliminary Operations
WARNING - Before you perform the checks listed below, please read
carefully the section “Safety and Maintenance”
Verify
that :
- the unit has not suffered visible damages due to transport or positio-
ning
- the unit is placed on an horizontal surface able to bear its weight
- the minimum operating area are respected
- the ambient conditions comply with the provided operating limits
- the hydraulic and electrical connections has been carried out correctly
Electrical cheks
Verify that the unit power supply line complies with the regulations in force.
Check that the section of power cables are suitable to withstand the ove-
rall absorption of the unit (see electrical data), and that the unit has been
properly grounded.
Check that all electrical connections are well fixed and all terminals pro-
perly tightened.
Switch on the unit by turning the switch in position ON . The display will
light a few seconds after power up , check the operating status of both Std
-by or off ( via keyboard). A wrong sequence of the power supply phases
is immediately detected by the phase sequence controller (standard on all
the three phase power supply units) and reported on the display of the unit.
To eliminate the error switch each other two phases of the power supply
line.
Verify that:
- the voltage of the power supply line complies with the the nominal one
of the unit
- for three phase power supply units, the unbalance between the phases
is lower than 3% (a higher value produces an excesive current input
on one or more phases causing possible damages to the electrical
components of the unit)
NOTE
.
Example of phase unbalance calculation
- Read the value of the three line voltages using a voltmeter :
line voltage between phases L
1
and L
2
:
V
1-2
= 390 V
line voltage between phases L
2
and L
3
:
V
2-3
= 397 V
line voltage between phases L
3
and L
1
:
V
3-1
= 395 V
- Calculate the difference between the maximum and minimum value of the
measured line voltages :
ΔV
max
= max ( V
1-2
; V
2-3
; V
3-1
) - min ( V
1-2
; V
2-3
; V
3-1
) = V
2-3
- V
1-2
= 397 - 390 = 7 V
- Calculate the average line voltage value :
Δ
average
= ( V
1-2
+ V
2-3
+ V
3-1
) / 3 = ( 390 + 397 + 395 ) / 3 = 394 V
- Calculate the percentage unbalance value :
ΔV
max
/ V
average
x 100 = 7 / 394 x 100 = 1,78 % < 2 %
Check that the connections made by the installer comply with the data
reported here .
If present, check that the resistance of the compressors oil crankase are
operating, by measuring the temperature rise of the oil crankase. The re-
sistance / s must be in operation for at least 24 hours before starting the
compressor , and in each case the temperature of the oil crankase must be
10 - 15 ° C higher than the ambient temperature .
WARNING - At least 24 hours prior to the operation of the unit ( or at the
end of each period of prolonged pause ) the unit must be powered in such
a way as to allow the heating elements of the compressor crankcases to
evaporate the refrigerant present in the oil. Failure to do so may cause
serious damage to the compressor and will void the warranty.
Hydraulic circuit checks
Check that all hydraulic connections are executed correctly: Refer to the
installation manual.
Check that the hydraulic system is filled, under pressure and air free (pos-
sibly vent it).
Make sure that any shutoff valves present in the system are properly open.
Make sure that the circulation pump is running and that the water flow
is sufficient to close the contact of the differential pressure and / or flow
switches .
Check the correct operation of the differential pressure and / or flow
switches: close the shutoff valve at the outlet of the heat exchanger, the
unit display must show the alarm message, eventually reopen the valve
and reset the alarm.
Turning on
ATTENTION
. The operation must be agreed in advance depending on
the timing of construction of the plant . Before the intervention of Service
Department all works (electrical and plumbing connections , water filling
and air vent of the plant) will have been completed.
Start all the plant components necessary to guarantee an adequate water
flow rate on the plant hydraulic circuit.
Activate the unit in cooling or in heating mode operating on the user interfa-
ce and setting a set point suitable to require the unit to work.
Refrigerant circuit checks
The vibrations during transport , may have loose connections : check for le-
aks of refrigerant gas especially at the refrigerant pressure taps , pressure
transducers and pressure switches.
After a short period of operation, check the oil level of the compressor ( if
present siight oil) and the absence of bubbles in the glass of liquid indicator
( if present) . The continuous passage of vapor bubbles may mean that the
refrigerant charge is low or that the expansion valve is not properly adju-
sted. The presence of bubbles in the running for short periods , however,
is possible.
Evaporation and condensation temperature
Verify that:
- the saturation temperature (dew point) corresponding to the conden-
sing pressure is about 10-15°C higher than the outdoor air temperatu-
re in cooling and about 5°C higher than the water outlet temperature in
heating
- the saturation temperature (dew point) corresponding to the evapora-
ting pressure is about 5°C lower than the water outlet temperature in
cooling and about 5-10°C lower than the outdoor air temperature in
heating
Superheat
Check the superheat comparing the temperature measured with a con-
tact thermostat fitted to the compressor suction pipe , with the temperature
shown on the low pressure gauge ( saturation temperature corresponding
to the evaporation pressure ) . The difference between these two tempe-
ratures gives the value of the superheta. The optimal values are between
4 and 8 ° C.
Subcooling
Check the subcooling comparing the temperature measured with a con-
tact thermostat on the pipe outlet of the condenser , with the temperature
shown on the pressure gauge of high pressure ( saturation temperature
corresponding to the condensation pressure ) . The difference between
these two temperatures gives the value of subcooling . The optimal values
are between 4 and 5 ° C, for reversible units with subcooler in the coil the
optimal values are between 10 and 20 ° C depending on the external air
temperature .
Discharge temperature
If the values of subcooling and superheat are regular, the temperature me-
asured at the outlet of the compressor discharge pipe must be:
- Units charged with R410A of 30/40 ° C higher than the condensing tem-
perature
- Units charged with R134a of 15/20 ° C higher than the condensing tem-
perature .
Hydraulic circuit check
- the difference between the water inlet and outlet temperature from the
plate heat exchanger of the unit is inside the limits provided.
Electrical setting check
- the current absorbed by the compresor and the fans is lower than the
maximum value admitted (FLA), as indicated in the section “Technical
data and performances”
Start up
Preliminary operation