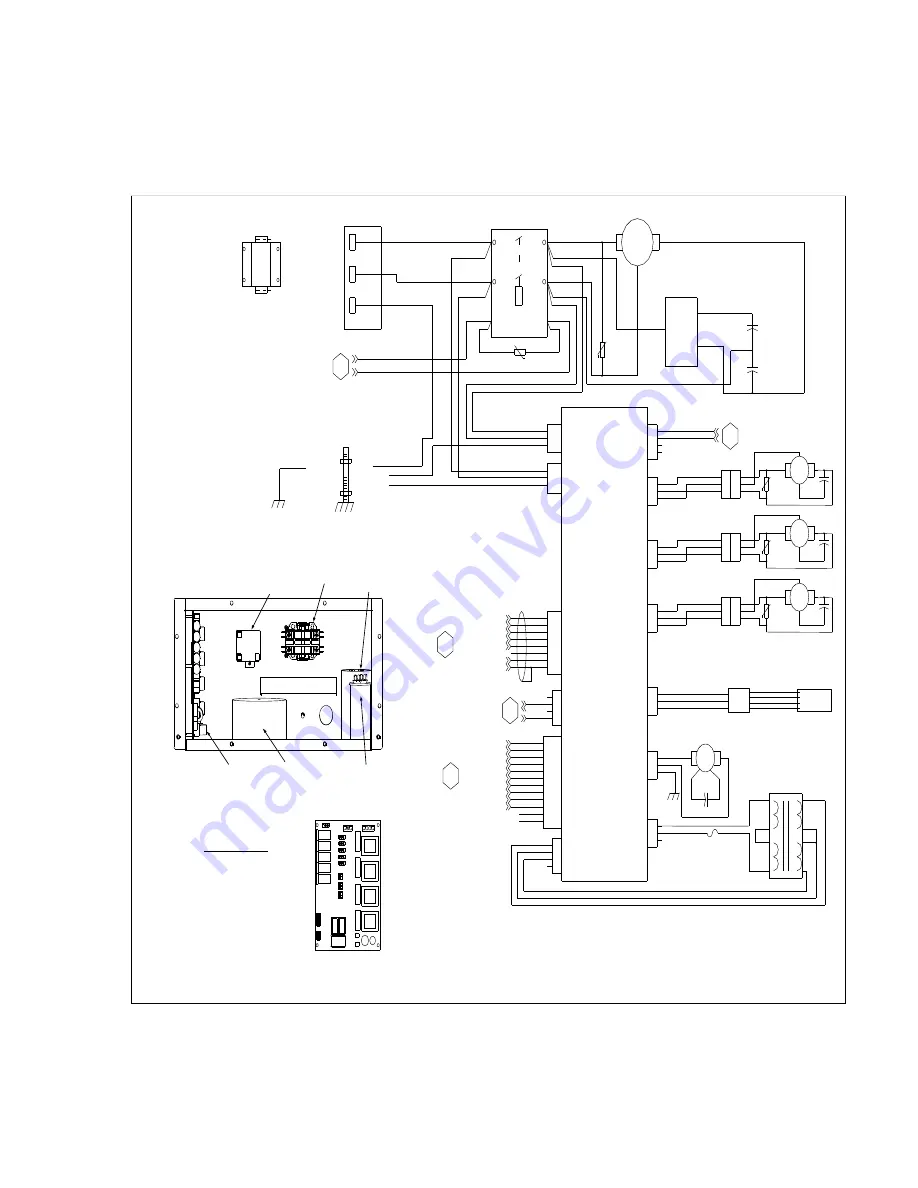
36
15.3 ELECTRICAL/SCHEMATIC-01
T2
L2
GRN/YEL
COIL B
MAIN GND
SECONDARY GND3
SECONDARY GND1
SECONDARY GND2
L6-30P
MAIN GROUND
WHT
WHT/RED
GRN/YEL
GRN/YEL
GRN/YEL
GRN
CONTACTOR, 2POLE 30AMP
COIL A
COIL B
BRN
5
LT BLUE
LT BLUE
GRN/YEL
GRN/YEL
LT BLUE
BRN
Line
1
NC
BLK
2
Common
RED
BLUE
189-227 uF @ 250 VAC
START CAP.
40 uF @ 370 VAC
RUN CAP.
OUTPUT
L2
L1
T2
T1
COIL A
INPUT
MAIN AC-P1
230 VAC NEU
230VAC LINE
WHT
BLK
T1
L1
S
R
C
BRN
COMPRESSOR
DIAGRAM
CONTACTOR, 2POLE 30A
L1
L2
GND
RELAY
STARTER
BRN
2
12
LPB-P14
BTR 230VAC LINE
230AC LINE
230AC NEUTRAL
CHASSIS GND
POS LAMPS
BTR_EN RIGHT
BTR_CHASSIS
230AC NEU.[SW'D]
230VAC LINE
CHASSIS GND
XFMR
PCB, LOWER POWER DISTRIBUTION
FAN
WHT/YEL
24VAC INPUT
GND
GND
12VAC
24VAC
LPB-P9
1
3
4
2
LOAD1 CTRL P5-9
BTR2 CTRL P5-7
BTR1 CTRL P5-8
BTR3 CTRL P5-6
AC_REF_IN CTRL P5-5
LOAD REF CTRL P5-3
LOAD3 CTRL P5-10
LOAD2 CTRL P5-4
+5VDC1_CNTLR_P12-1
+5VDC2_CNTLR_P12-2
+15VDC_CNTLR_P12-3
-15VDC_CNTLR_P12-4
ANA GND_CNTLR_P12-5
DIG GND1_CNTLR_P12-7
DIG GND2_CNTLR_P12-9
FAN RUN CTRL P5-12
COMP RUN CTRL P5-1
+5 VDC 2 IN
+5 VDC 1 IN
+15VDC IN
-15VDC IN
ANA GND
DIG GND 1
DIG GND 2
GRN
GRN
RED
RED
YEL
ORG
GRN
1
8
7
3
6
5
4
2
24VAC RTN
24VAC RTN
WHT/RED
WHT/GRN
4
3
2
1
WHT
LOAD2
2
WHT
WHT
WHT
WHT
WHT
WHT
WHT
LOAD3
BTR1
BTR2
BTR3
LOAD REF
AC_REF_IN
7
8
4
5
6
3
WHT
LOAD1
LPB-P13
1
LPB-P10
24VAC
24VAC
WHT
FAN
10
11
12
COMP RUN
9
LT BLUE
BRN
1
2
3
LPB-P4
8
5
8
7
6
7
6
5
RED
1
2
3
4
1
4
3
2
325VA 24VAC_CT
WHT
BLK
GRN
1
2
3
LPB-P3
ORN
GRN/YEL
3
2
3
2
1
BRN
BLUE
GRN/YEL
START CAP
FAN 1
LPB-P12
3
BLK
3
COMP_RUN
24 VAC
CONTACTOR COIL
BTR MOTOR 1
BTR MOTOR 2
BTR_CHASSIS
BTR_EN LEFT
BTR 230VAC LINE
SW_230 VAC LINE T1-3
SW_230 VAC NEU T2-3
SECONDARY GND 2
230VAC NEU L2-2
SECONDARY GND 1
230VAC LINE L1-2
2
1
3
LPB-P2 SWITCHED AC INPUT
1
3
2
LPB-P1 MAIN AC INPUT
WHT/RED
WHT
2
3
1
4
LPB-P8
BLK
LPB-P7
BLK
LPB-P6
RED
GRN/YEL
2
3
1
GRY
1
LEFT
TAN
GRN
BTR
GRY
1
3
CENTER
TAN
BTR
GRN
BLK
2
1
1
3
2
PCB, LOWER POWER DISTRIBUTION
RED
RED
WHT
YEL
YEL
BRN
LT BLU
RED
WHT
LEGEND: FUSE RATINGS
F1-LEFT BEATER (2.5A/230V)
F2-RIGHT BEATER (2.5A/230V)
F3-AIR COMP. (2.5A/230V)
F4-T1 (2.5A/230V)
F5-MERCHANDISER (2.5A/230V)
P2
P12
P1
BALLAST
RED
RED
BLUE
BLUE
FLUORESCENT LAMP
BTR MOTOR 2
BTR_CHASSIS
BTR_EN RIGHT
BTR 230VAC LINE
LPB-P5
BLK
2
3
GRN/YEL
YEL
1
11
33
22
BTR
RIGHT
GRY
BLK
TAN
GRN
A
A
T1
K101
LPB1
F1
F2
F3
F4
F5
CONTACTOR
C101
C102
F5
F4
F3
F2
F1
P13
P14
P3
P4
P5
P6
P7
P8
P9
P10
B
C
D