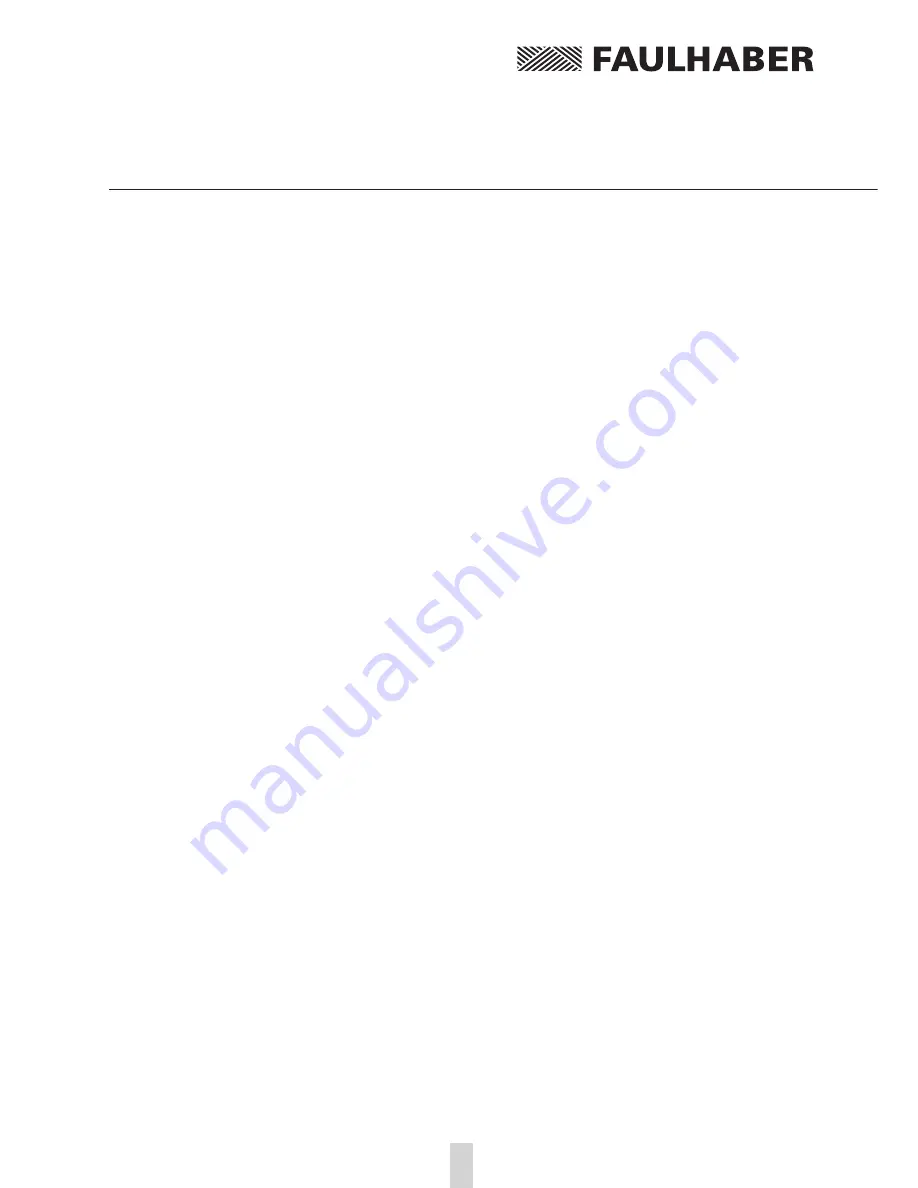
29
Additional Modes
The direction of rotation is set with the ADR and
ADL commands.
ADR
➔
with a positive voltage the motor
rotates in the positive direction (right).
ADL
➔
with a negative voltage the motor
rotates in the negative direction (left).
Positioning with a Pulse-Width
Modulated Signal
Positioning will be controlled by a PWM
from the analog input when the commands
APCMOD
and
SOR2
are given one after the
other. The pulse duty ration sets the command
position value. A pulse duty ratio of 0.5 (ON
time = OFF time) will set the command position
to 0. A pulse duty ratio larger than 0.5 leads to
a positive command position value and a ratio
less than 0.5 leads to a negative value.
The
AC
- and
SP
-values are also applicable in
analog positioning mode making soft accele-
ration and braking possible.
Special Function:
The presence of a Hall Sensor makes it possible to
register the absolute position of the armature
inside of one revolution. That means that in the
event of a power loss the exact position can be
recalled after the power is restored (if the
armature has only moved within one revolution).
With the following commands it is possible to
position the motor inside one revolution with
a voltage ranging from 0 - 10 V even after the
power has been turned off and then on again.
ADL
... With a positive voltage the motor
will rotate to a negative position
(after power is restored to the motor
it is at a negative position value
ranging from 0 to –1000)
APCMOD... Switches to analog positioning
LL1000
... Sets maximum position to one
revolution.
EEPSAV ... Saves the configuration.
Using an External Encoder to Measure
Actual Position
A processed signal from an external encoder can be
used to precisely measure actual position.
■
The positioning resolution depends on the resolu-
tion of the encoder.
■
Depending on the application, the speed can
either be measured at the encoder or the Hall
Sensor.
■
The external encoder can be fastened directly to
the motor shaft. The encoder can also be fastened
directly to the output shaft of the complete
system enabling highly accurate positioning that
can be optimized at the output stage.
■
The analog Hall Sensors provide the motor com-
mutation.
■
All other positioning mode functions, for example,
combined motion profiles, can also be used in
conjunction with the external encoder.