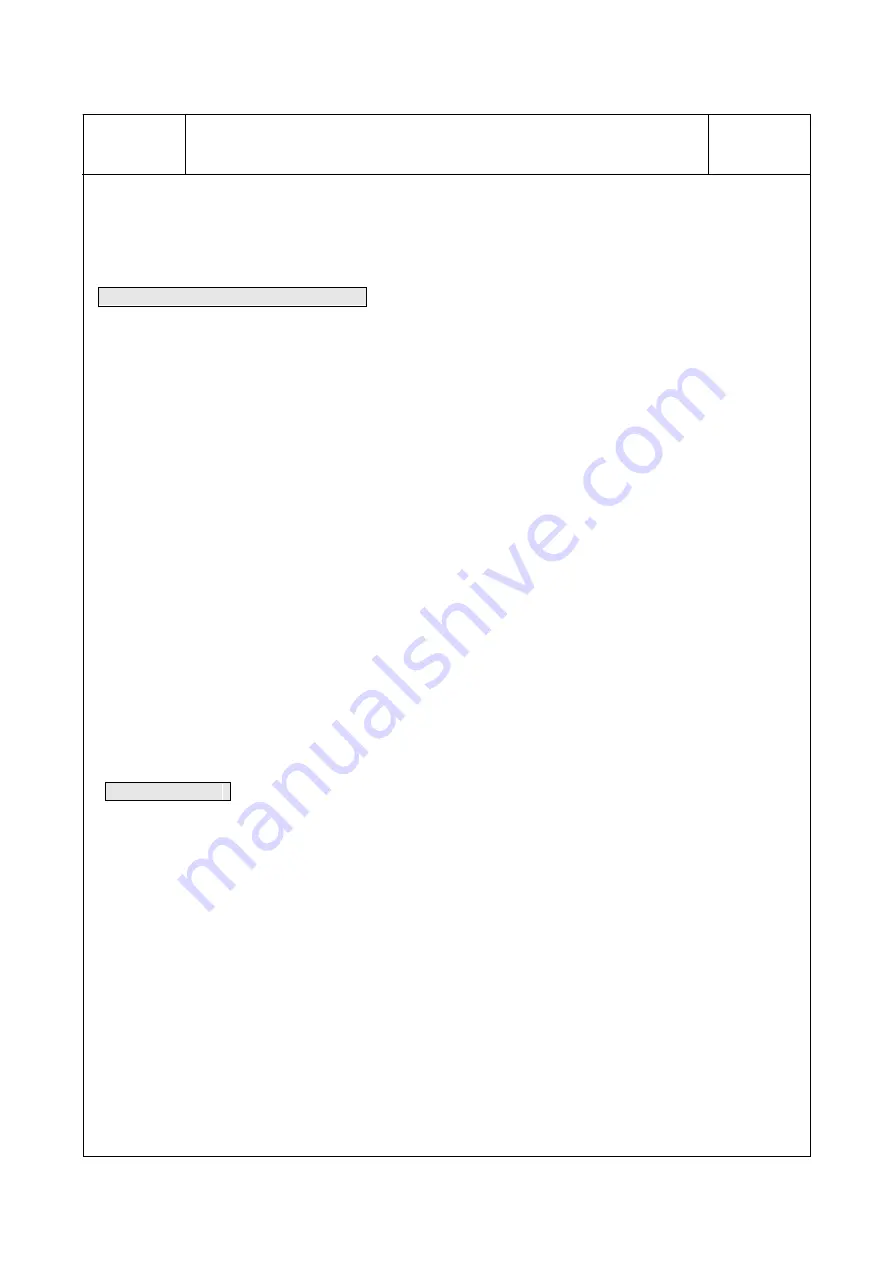
Advanced Function Instruction
7 -7 0
FUN 86
TPCTL
PID TEMPERATURE CONTROL INSTRUCTION
FUN 86
TPCTL
PVn : Process variable at time “n”
PVn_1: Process variable when loop was last solved
En: Error at time “n” ; E= SP – PVn
Ts: Solution interval for PID calculation (Valid value are 10, 20, 40, 80,160, 320; the unit is in 0.1Sec)
PID Parameter Adjustment Guide
z
As the gain (Kc) adjustment getting larger, the larger the proportional contribution to the output. This can
obtain a sensitive and rapid control reaction. However, when the gain is too large, it may cause oscillation.
Do the best to adjust “Kc” larger (but not to the extent of making oscillation), which could increase the
process reaction and reduce the steady state error.
z
Integral item may be used to eliminate the steady state error. The larger the number (Ti, integral tuning
constant), the larger the integral contribution to the output. When there is steady state error, adjust the “Ti”
larger to decrease the error.
When the “Ti” = 0, the integral item makes no contribution to the output.
For exam. , if the reset time is 6 minutes, Ti=100/6=17
;
if the integral time is 5 minutes, Ti=100/5=20.
z
Derivative item may be used to make the process smoother and not too over shoot. The larger the number
(Td, derivative tuning constant), the larger the derivative contribution to the output. When there is too over
shoot, adjust the “Td” larger to decrease the amount of over shoot.
When the “Td” = 0, the derivative item makes no contribution to the output.
For exa, if the rate time is 1 minute, then the Td = 100; if the differential time is 2 minute, then the Td = 200.
z
Properly adjust the PID parameters can obtain an excellent result for temperature control.
z
The default solution interval for PID calculation is 4 seconds (Ts=40)
z
The default of gain value (Kc) is 110, where Pb=1000/110
×
0.1%
≒
0.91%; the system full range is 1638
°
, it
means 1638
×
0.91
≒
14.8
°
to enter proportional band control.
z
The default of integral tuning constant is 17, it means the reset time is 6 minutes (Ti=100/6=17).
z
The default of derivative tuning constant is 50, it means the rate time is 0.5 minutes (Td=50).
z
When changing the PID solution interval, it may tune the parameters Kc, Ti, Td again.
Instruction guide
z
FUN86 will be enabled after reading all temperature channels.
z
When execution control “EN” = 1, it depends on the input status of H/C for PID operation to make heating
(H/C=1) or cooling (H/C=0) control. The current values of measured temperature are through the
multiplexing temperature module ; the set points of desired temperature are stored in the registers starting
from Sv. With the calculation of software PID expression, it will respond the error with an output signal
according to the setting of set point, the error's integral and the rate of change of the process variable.
Convert the output of PID calculation to be the time proportional on/off (PWM) output, and via transistor
output to control the SSR for heating or cooling process; where there is a good performance and very low
cost solution. It may also apply the output of PID calculation (stored in registers starting from OR), by way
of D/A analog output module, to control SCR or proportional valve, so as to get more precise process control.
z
When the setting of Sn, Zn (0 Sn 31 and 1 Zn 32, as well as 1 Sn + Zn 32) comes error, this
instruction will not be executed and the instruction output “ERR” will be ON.
This instruction compares the current value with the set point to check whether the current temperature falls within
deviation range (stored in register starting from Os). If it falls in the deviation range, it will set the in-zone bit of
that point to be ON; if not, clear the in-zone bit of that point to be OFF, and make instruction output “ALM” to be
ON.
Содержание FBs-CBE
Страница 78: ...MEMO ...
Страница 111: ...4 6 X0 X1 Node A Y0 Y1 Node B differential down Incerse differential up t Scan time Inverse t t ...
Страница 141: ...Basic Function Instruction 6 16 FUN 2 SKP SKIP START FUN 2 SKP Y2 Y1 Y0 T201 10S X0 X1 X2 0 10 0 ...
Страница 305: ...MEMO ...
Страница 348: ...MEMO ...