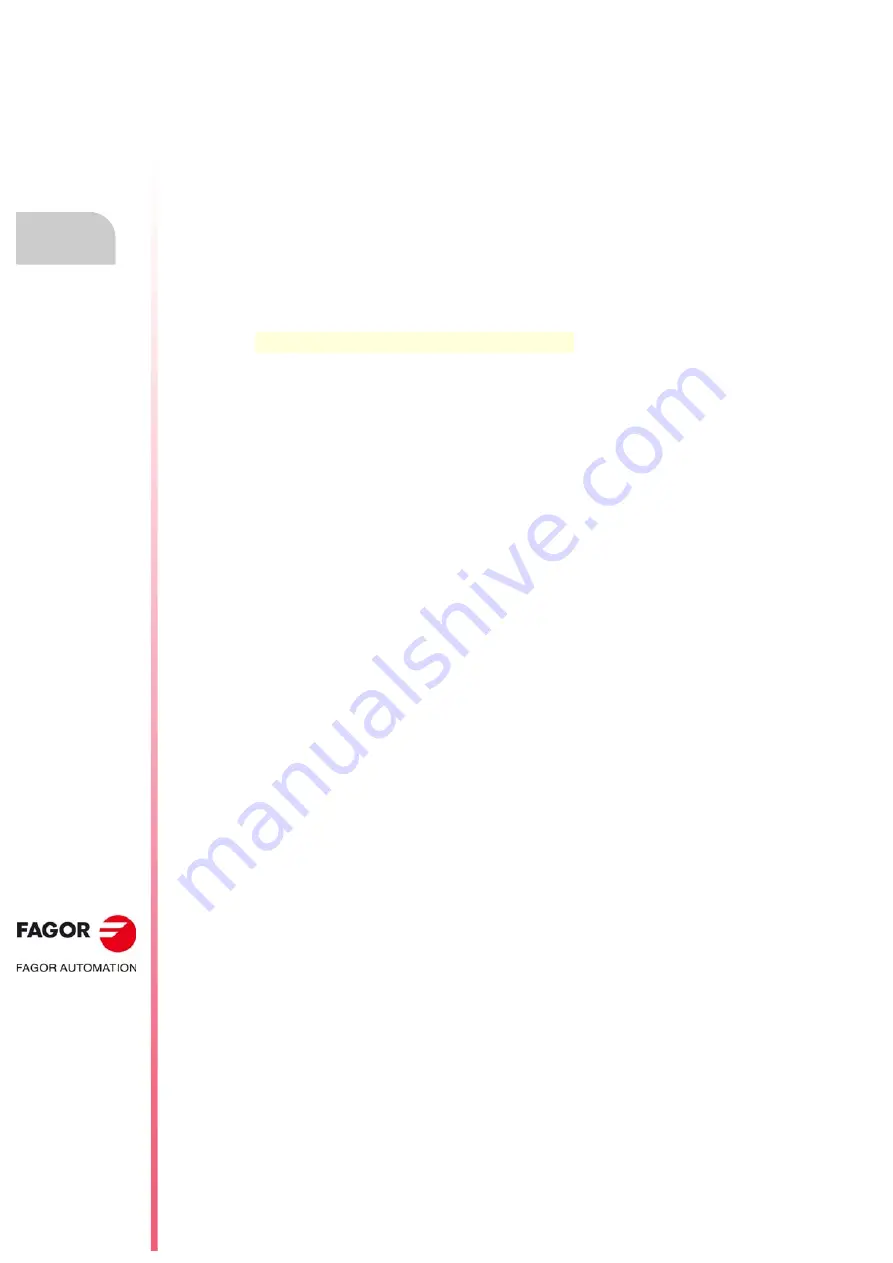
Programming manual.
CNC 8070
20.
HSC. HIGH SPEED
MACHININ
G
.
Ca
nceli
ng th
e HSC mo
de.
·374·
(R
EF
: 1709)
20.6
Canceling the HSC mode.
The HSC mode is canceled with the instruction #HSC OFF. HSC is also canceled when
programming any of the functions G05, G07 or G50. Functions G60 and G61 do not cancel
the HSC mode. Activating a second HSC mode does not cancel the previous HSC mode.
Programming.
Program the instruction alone in the block.
Programming format.
The programming format is:
#HSC OFF
Influence of the reset, turning the CNC off and of the M30.
The HSC mode is canceled on power-up, after executing an M02 or M30 and after an
emergency or reset.
#HSC OFF
Содержание 8070 BL
Страница 1: ... Ref 1709 8070 CNC Programming manual ...
Страница 8: ...BLANK PAGE 8 ...
Страница 12: ...BLANK PAGE 12 ...
Страница 14: ...BLANK PAGE 14 ...
Страница 26: ...BLANK PAGE 26 ...
Страница 28: ...BLANK PAGE 28 ...
Страница 30: ...BLANK PAGE 30 ...
Страница 60: ...Programming manual CNC 8070 2 MACHINE OVERVIEW Home search 60 REF 1709 ...
Страница 72: ...Programming manual CNC 8070 3 COORDINATE SYSTEM Coordinate programming 72 REF 1709 ...
Страница 80: ...Programming manual CNC 8070 4 WORK PLANES Select the longitudinal axis of the tool 80 REF 1709 ...
Страница 96: ...Programming manual CNC 8070 5 ORIGIN SELECTION Polar origin preset G30 96 REF 1709 ...
Страница 178: ...Programming manual CNC 8070 9 TOOL PATH CONTROL MANUAL INTERVENTION Variables 178 REF 1709 ...
Страница 304: ...Programming manual CNC 8070 16 C AXIS Machining of the turning side of the part 304 REF 1709 ...
Страница 440: ...Programming manual CNC 8070 22 STATEMENTS AND INSTRUCTIONS Flow controlling instructions 440 REF 1709 ...
Страница 442: ...Programming manual CNC 8070 23 CNC VARIABLES 442 REF 1709 ...
Страница 443: ...Programming manual CNC 8070 443 User notes REF 1709 ...