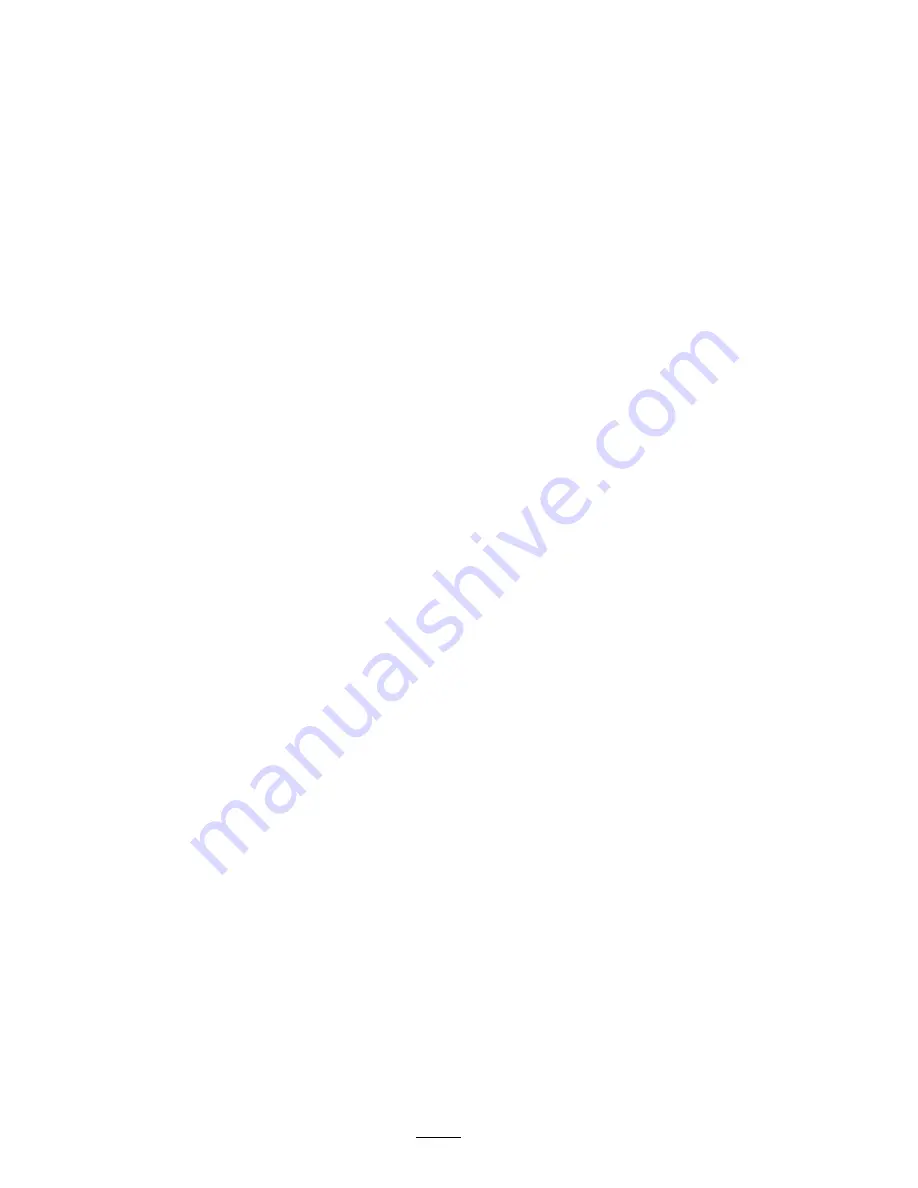
Contents
Introduction ........................................................... 3
Safety ..................................................................... 5
Safety Alert Symbol ......................................... 5
Safe Operating Practices .................................. 5
Safety and Instructional Decals ......................11
Specifications ........................................................20
Systems ..........................................................20
Dimensions....................................................23
Torque Requirements .....................................24
Product Overview .................................................24
Operation ..............................................................25
Controls .........................................................25
Pre-Start.........................................................29
Operating Instructions ...................................29
Transporting ..................................................36
Maintenance ..........................................................39
Recommended Maintenance Schedule(s) ............39
Periodic Maintenance ........................................40
Check Engine Oil Level ..................................40
Check Battery Charge .....................................40
Check Mower Blades ......................................42
Check Safety Interlock System ........................44
Check Rollover Protections Systems (Roll
Bar) Knobs.................................................47
Check Seat Belt...............................................47
Check for Loose Hardware .............................47
Service Air Cleaner .........................................47
Check Deck Gearbox Oil................................47
Check Hydraulic Fluid Level ...........................48
Check Tire Pressures ......................................48
Check Condition Of Belts...............................48
Lubricate Grease Fittings................................49
Check Wheel Lug Nuts...................................49
Drain Fuel Filter/Water Separator...................50
Change Fuel Filter/Water Separator................51
Change Deck Gearbox Oil..............................52
Change Engine Oil and Filter..........................52
Change Hydraulic System Filter and
Fluid ..........................................................52
Check Engine Coolant Level...........................54
Change Engine Coolant..................................54
Thread Locking Adhesives..............................55
Mobil HTS Grease (Or Food-Grade
Anti-seize)..................................................55
Copper-Based Anti-seize ...............................55
Dielectric Grease............................................56
Adjustments ......................................................56
Deck Leveling–60 and 72 Inch Models ............56
Deck Leveling–96 Inch Models.......................58
Deck Belt Tension ..........................................61
Parking Brake Adjustment ..............................61
Motion Control Linkage Adjustment ..............62
Motion Control Damper Adjustment..............63
Caster Pivot Bearings Pre-Load
Adjustment ................................................63
Cleaning ............................................................64
Clean Engine and Exhaust System
Area ...........................................................64
Clean the Radiator ..........................................64
Clean Debris From Machine ...........................65
Clean Grass Build-Up Under Deck .................65
Inspect Engine Valve Clearance ......................65
Waste Disposal ...............................................65
Troubleshooting ....................................................66
Schematics ............................................................68
4
Содержание Lazer Z Series
Страница 1: ...LAZER Z DIESEL For Serial Nos 402 082 300 Higher Part No 4503 837 Rev B ...
Страница 74: ...74 ...