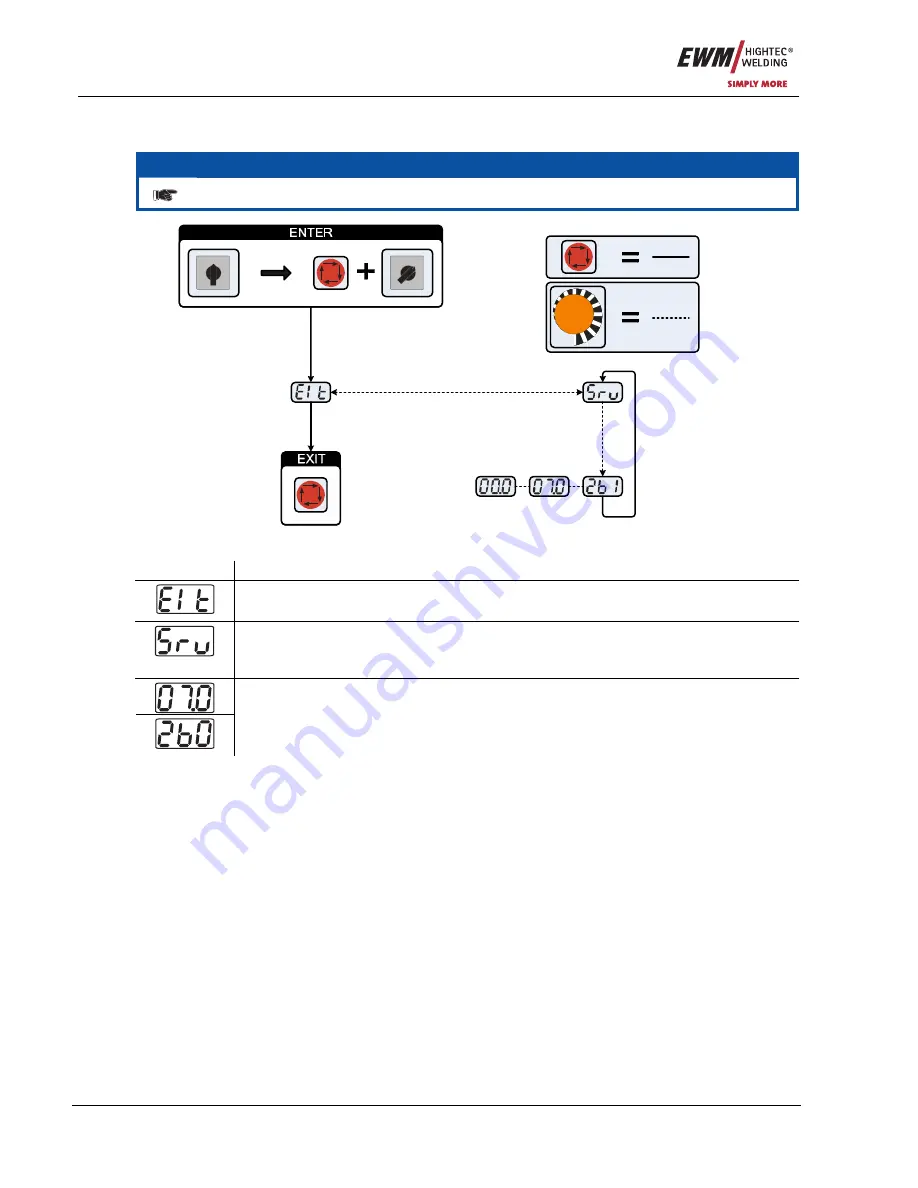
Operating problems, causes and remedies
Display machine control software version
66
Item No.: 099-000155-EWM01
9.3
Display machine control software version
NOTE
The query of the software versions only serves to inform the authorised service staff!
0
1
0
1
Figure 9-2
Display Setting/selection
Exit the menu
Exit
Service menu
Modifications to the service menu may only be carried out by authorised maintenance
staff!
Software version query (example)
07=
System bus ID
02b0= Version
number
System bus ID and version number are separated by a dot.