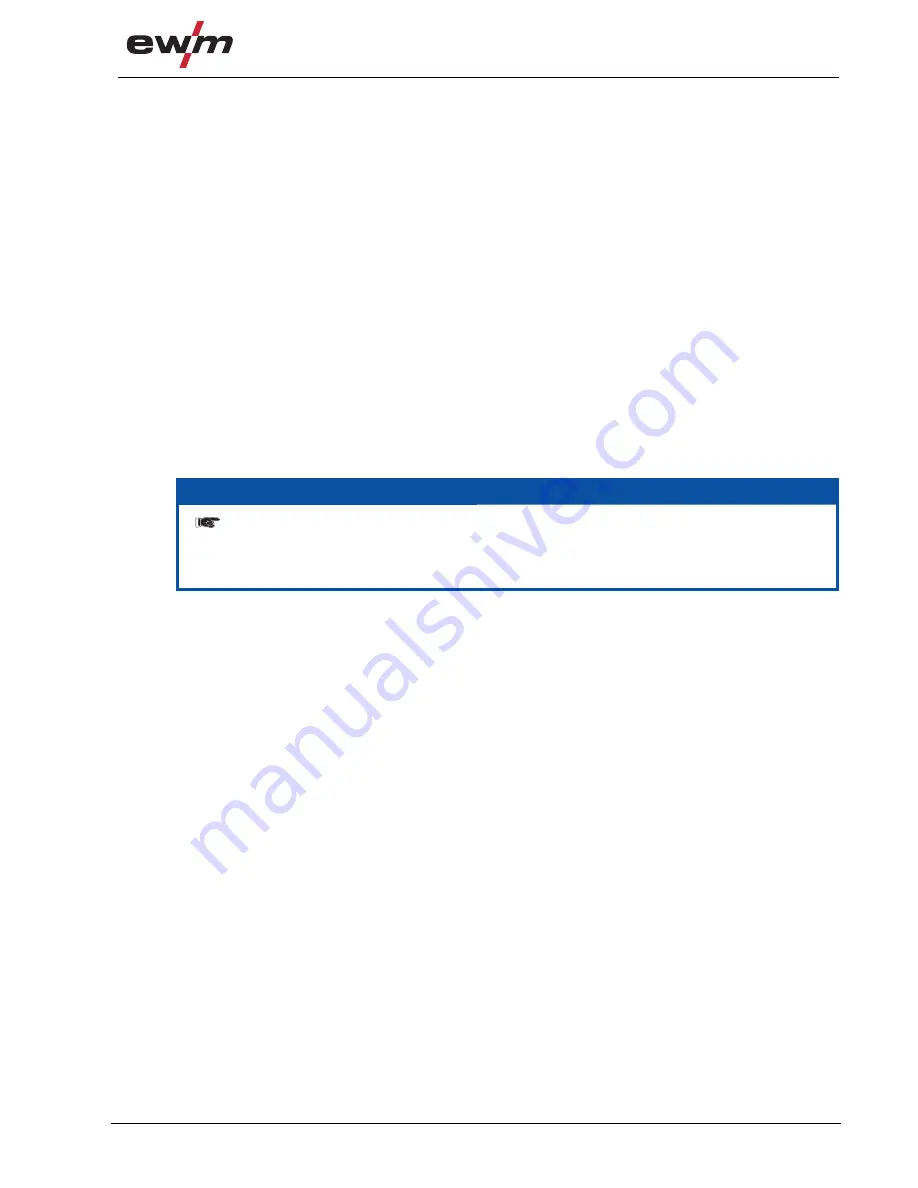
Design and function
MIG/MAG welding
099-005215-EW501
29.06.2011
41
5.7.10
forceArc
The forceArc process is welding in the spray arc range with a considerably shortened arc.
Disadvantages of short-circuit phases are compensated by the fast control inverter technology.
Benefits of forceArc welding:
• Good
fusion
penetration
• Directionally
stable
arc
• No
undercuts
• Higher
welding
speed
• Small heat-affected zone
You can make use of these properties after selecting the forceArc process (see the "Selecting a
MIG/MAG welding task" chapter).
As with pulse arc welding, it is important to make sure of a good welding current connection.
• Keep welding current cables as short as possible and ensure that cable cross-sections are adequate!
• Fully unroll welding current cables, torche tube packages and, if applicable, intermediate tube
packages. Avoid loops!
• Use welding torches, preferably water-cooled, that are suitable for the higher power range.
• Use welding wire with adequate copper coating when welding steel. The wire spool should have layer
spooling.
NOTE
Unstable arc!
Welding current cables that are not fully unrolled can cause faults in the arc (flickering).
• Fully unroll welding current cables, torch tube packages and, if applicable, intermediate
tube packages. Avoid loops!
5.7.11
rootArc
The rootArc process is welding with a stable, soft, short arc, even when using welding leads.
The benefits of rootArc welding:
• Easy, reliable root welding without pool support.
• Effortless gap bridging.
You can make use of these properties after selecting the rootArc process (see the "Selecting a MIG/MAG
welding task" chapter).