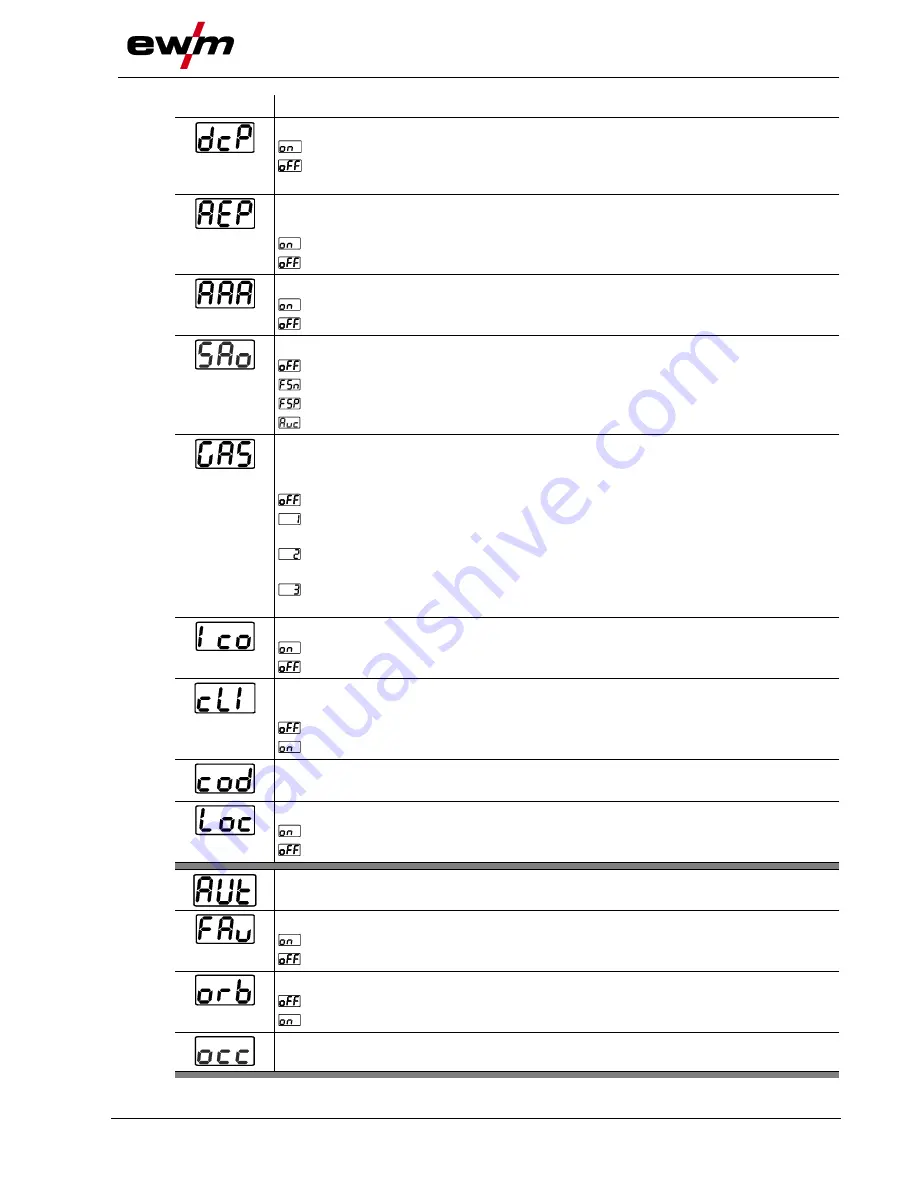
Welding procedure
Machine configuration menu
099-00T400-EW501
21.10.2016
69
Display
Setting/selection
Welding current polarity switch (dc+) with TIG DC
------- Polarity switch released
------- Polarity switch blocked;
protects the tungsten electrode from being permanently damaged (ex works).
Reconditioning pulse (tungsten ball stability)
Cleaning effect of the tungsten ball at the end of welding.
------- Function enabled (ex works)
------- Function disabled
activArc voltage measuring
------- Function enabled (ex works)
------- Function disabled
Error output to interface for automated welding, contact SYN_A
------- AC synchronisation or hot wire (ex works)
------- Error signal, negative logic
------- Error signal, positive logic
------- AVC (Arc voltage control) connection
Gas monitoring
Depending on where the gas sensor is situated, the use of a pilot static tube and the
welding process monitoring phase.
------- Function disabled (ex works).
------- Monitoring during the welding process. Gas sensor between gas valve and
welding torch (with pilot static tube).
------- Monitoring prior to the welding process. Gas sensor between gas valve and
welding torch (without pilot static tube).
------- Permanent monitoring Gas sensor between gas cylinder and gas valve (with
pilot static tube).
AC commutation optimisation
> see 4.1.17 chapter
------- Function enabled
------- Function disabled (ex works)
Minimum current limit
> see 4.1.2 chapter
Depending on the set electrode diameter
------- Function disabled
------- Function enabled (ex works)
Access control
– access code
Setting: 000 to 999 (000 ex works)
Access control
> see 4.5 chapter
------- Function enabled
------- Function disabled (ex works)
Automation menu
Fast take-over of control voltage (automation)
------- Function enabled
------- Function disabled (ex works)
Orbital welding
------- Function disabled (ex works)
------- Function enabled
Orbital welding
Correction value for orbital current