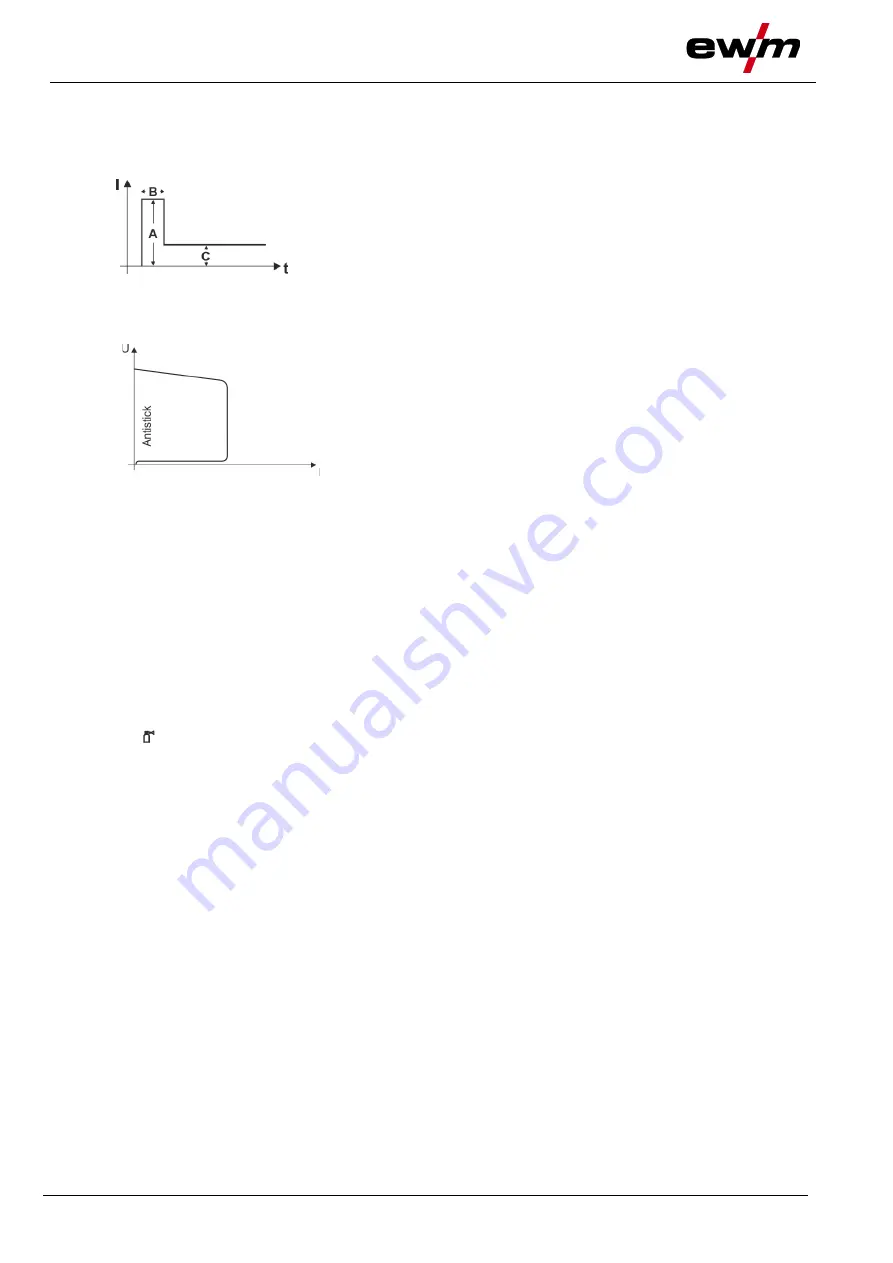
Functional characteristics
Options (additional components)
50
099-5TLPXQ-EW501
29.01.2021
5.4.3 Hotstart
The function hot start ensures a secure igniting of the arc and a sufficient heating to the still cold parent
metal at the beginning of the welding process. The ignition takes place here with increased current (hot
start current) over a certain time (hot start time).
A = Hot start current
B = Hot start time
C = Main current
I =
Current
t =
Time
Figure 5-41
5.4.4 Antistick
The Antistick feature prevents the electrode from annealing.
Should the electrode stick despite the Arcforce feature, the machine au-
tomatically switches to the minimum current within approx. one second.
This prevents the electrode from annealing. Check the welding current
setting and correct for the welding task in hand.
Figure 5-42
5.5 Options (additional components)
5.5.1 Electronic gas flow control (OW DGC)
The connected gas line has to have a preset pressure of 3–5 bar.
The electronic gas flow control (DGC) regulates the optimum gas flow rate for the respective welding pro-
cess (optimally preset from the factory). This helps avoid welding errors caused by too much (gas blast)
or insufficient shielding gas (shielding gas cylinder empty or gas supply interrupted).
The required gas flow rate can be controlled by the user and corrected if necessary (nominal valuesbe-
fore welding). In addition, when used in combination with Xnet software (optional), the exact gas con-
sumption can be recorded.
The parameter is selected by pressing the parameter display push-button on the right side. The signal
light "
"
is illuminated. The value unitscan be in litres per minute “l/min" or Cubic Feet Per Hour "cFH"
(adjustable with special parameters P29
> see 5.10 chapter
). During the welding process, these nominal
values are compared with the actual values. If these values differ more than the specified error threshold
(special parameters P28) the error message "Err 8" is output and the continuous welding process is stop-
ped.
5.5.2 Wire reserve sensor (OW WRS)
Minimizes the risk of seam errors due to early detection and display (signal light "End") with about 10 %
remaining wire. At the same time, the forward-looking production allows the reduction of the auxiliary pro-
cess times.
5.5.3 Wire spool heater (OW WHS)
Prevention of condensation on the welding wire due to adjustable temperature (special parameters
P26
> see 5.10.1.23 chapter
) of the wire spool heater.