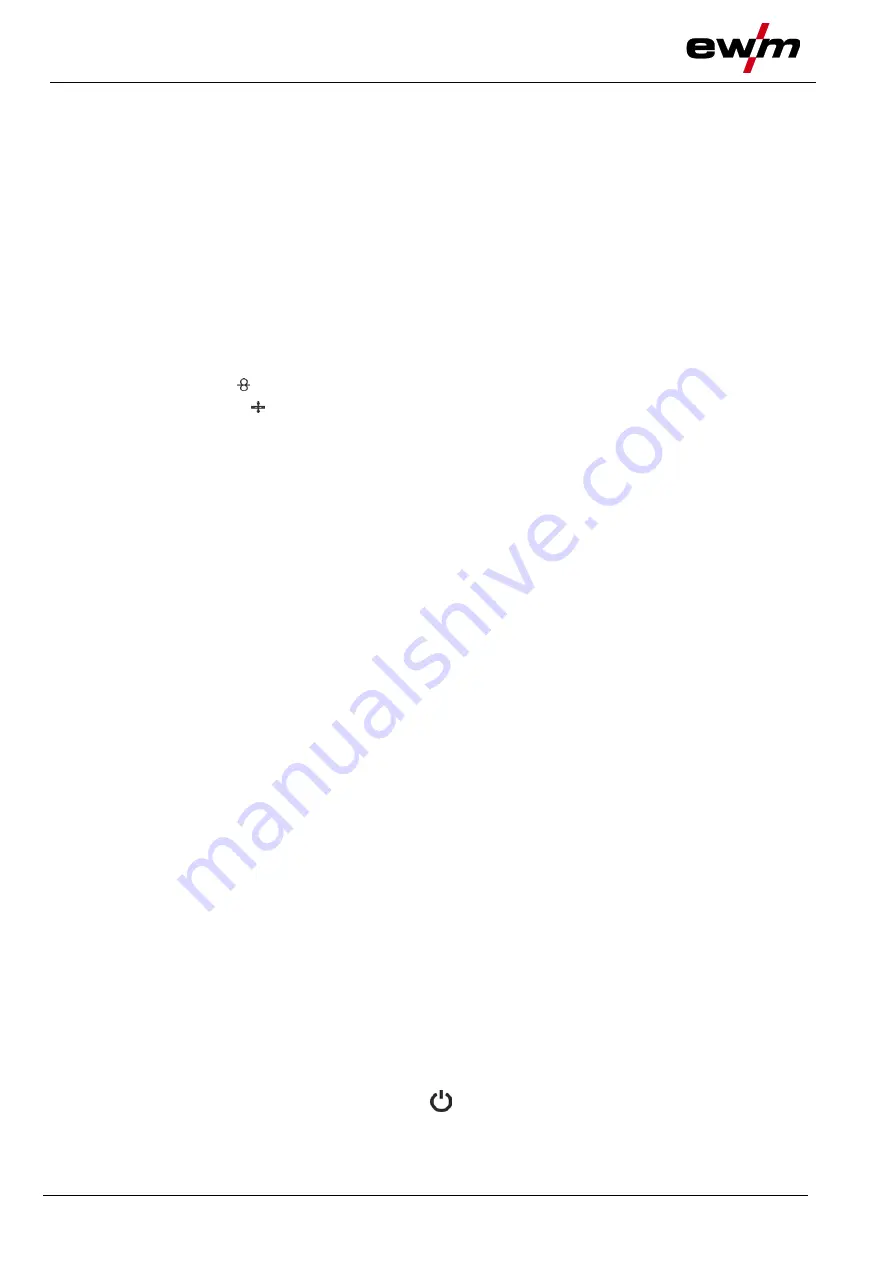
Machine control – Operating elements
Operating the machine control
20
099-5TLPXQ-EW501
29.01.2021
4.3 Operating the machine control
4.3.1 Main screen
The machine control switches to the main screen after it has been turned on or a setting has been com-
pleted. This means that the previously selected settings (indicated by signal lights where applicable) and
the nominal value for the current (A) are displayed in the left-hand welding data display. Depending on
the selection, the right-hand display shows the welding voltage (V) nominal value or the welding power
(kW) actual value. The control always switches back to the main screen after 4 sec..
4.3.2 Welding power setting
The welding power is adjusted with the rotary knob (click wheel) for welding power. You can also adjust
the parameters in the operation sequence or settings in the various machine menus.
MIG/MAG settings
The welding power (heat input into the material) can be changed by setting the following three parame-
ters:
• wire feed speed
• material thickness
• welding current A
These three parameters are interdependent and always change together. The significant parameter is the
wire feed speed in m/min. The wire feed speed can be adjusted in increments of 0.1 m/min (4.0 ipm). The
associated welding current and material thickness are determined from the wire feed speed.
The welding current displayed and material thickness are to be understood as guide values for the user
and rounded to full amperage and 0.1 mm material thickness.
A change in the wire feed speed, for example by 0.1 m/min, leads to a more or less large change in the
welding current displayed or in the material thickness displayed depending on the selected welding wire
diameter. The display of the welding current and the material thickness are also dependent on the selec-
ted wire diameter.
For example, a change in wire feed speed of 0.1 m/min and a selected wire diameter of 0.8 mm results in
a smaller change in the current or thickness of material than a change in wire feed speed of 0.1 m/min
and a selected wire diameter of 1.6 mm.
Depending on the diameter of the wire to be welded, it is possible that smaller or larger jumps in the dis-
play of material thickness or welding current take place or changes of these values become visible only
after several “clicks” on the rotary transducer. As described above, the reason for this is the change in the
wire feed speed by 0.1 m/min per click and the resulting change in the current or material thickness as a
function of the preselected welding wire diameter.
Please note also that the guide value of the welding current displayed before welding may deviate from
the guide value during welding depending on the actual stick-out (free wire end used for welding).
The reason lies in the preheating of the free wire end by the welding current. For example, the preheating
in the welding wire increases with the length of the stick-out. This means if the stick-out (free wire end)
increases, the actual welding current decreases due to larger preheating in the wire. If the free wire end
decreases, the actual welding current increases. This enables the welder to influence the heat input in the
component within limits by changing the distance of the welding torch.
Setting of TIG/MMA:
The welding power is set with the parameter “welding current” that can be adjusted in increments of 1 am-
pere.
4.3.3 Changing basic settings (machine configuration menu)
The basic welding system functions can be adjusted in the machine configuration menu. Only experi-
enced users should change the settings
> see 5.8 chapter
.
4.3.4 Lock function
The lock function protects against accidental adjustment of the device settings.
The user can switch the lock function on or off by pressing the button for a long time from each machine
control or accessory component with the symbol
.