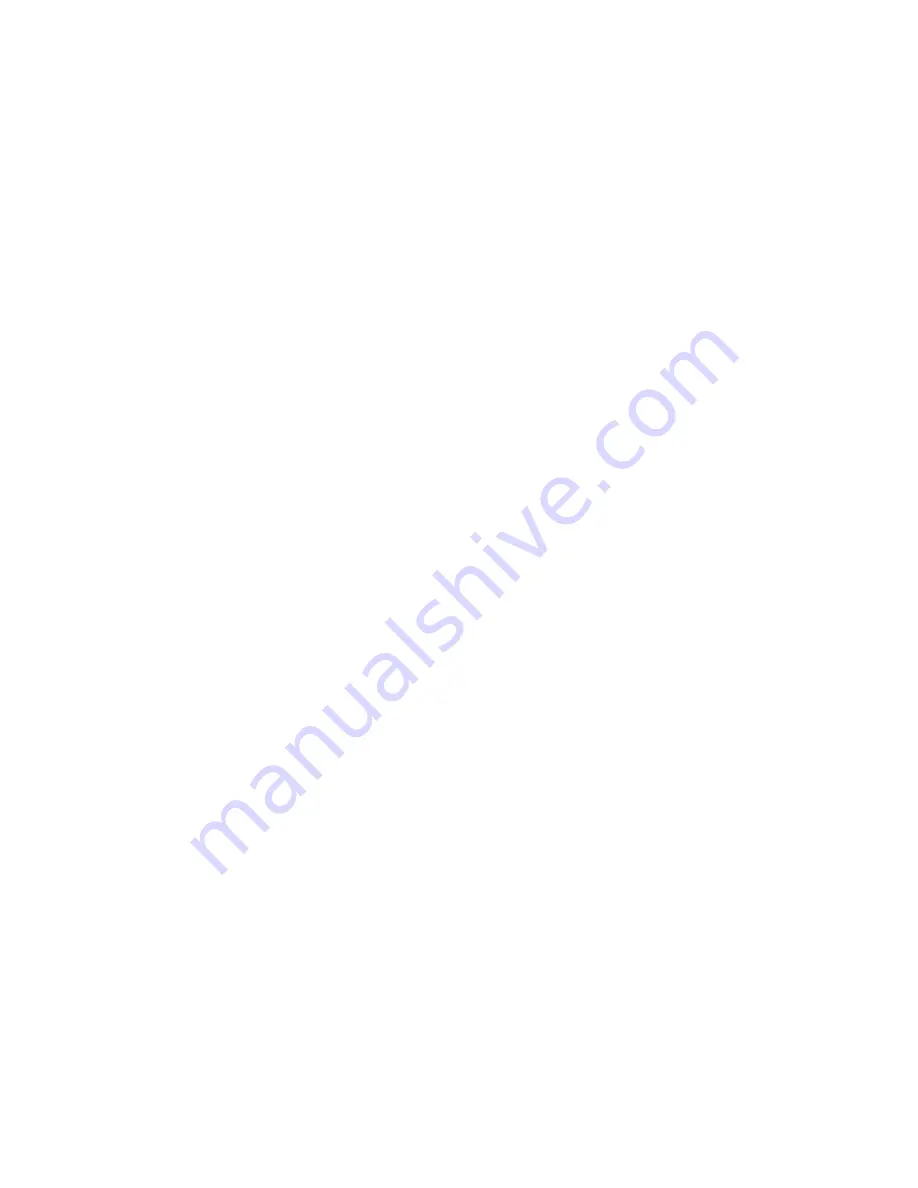
24
1.
While welding aluminum with the Spool gun or MIG gun you must use 100% argon. You
cannot use a mix as you would with steel or stainless.
2.
While welding aluminum with the Spool gun or MIG gun you must use the next size up tip or
a special oversize tip for the wire because the heat will cause the aluminum wire to swell
and it will either drag or seize in the tip.
3.
While welding aluminum with the MIG process, best results are achieved by using a dedi-
cated stainless steel brush to remove the oxide layer and acetone or aluminum cleaner be-
fore welding. Even though aluminum may appear shiny and clean, it still has an oxide layer,
and a thin layer of oil left over from the manufacturing process. Some soot will appear in
most MIG welds but if a lot is noticed, you have either contaminated metal, or insufficient
gas flow. You can also induce turbulence by having too much of a torch angle. Start with a
90 degree angle and then lean the gun slightly (about 15 degrees) to the
“
push
”
position.
4.
Welding aluminum is not a short circuit process. It is a spray transfer process. Spray trans-
fer is a process that is can be used to weld many metals, but in Aluminum it must be used
to weld correctly. In spray transfer, the wire does not short out against the weld material.
Instead a steady
“
spray
”
of droplets of molten metal pinches off before the wire can contact
the material. It is a much quieter process. If you are not familiar with the spray transfer
process, please research it before you try it. If you incorrectly adjust the welder while weld-
ing aluminum in the MIG process, you will burn up contact tips almost instantly.
5.
If you are trying to weld Aluminum with .
030”
wire or smaller, you may not achieve ade-
quate results because of the higher wire feed speeds needed. Try stepping up to the next
wire size and wire feed speed rate requirements will drop.
6.
If using with a generator, use with only a generator rated or certified for clean power output.
This a rating given by the manufacturer of the generator if the total harmonic distortion is
10% or less (usually 5% or less). A generator that does not produce clean power can cause
erratic operation and damage to the welder
’
s electronics. Ideally a generator capable of
generating 3500 watts or more should be used for 120V use and 7500 watts for 240V use.
7.
MIG burn back is a common condition where the wire may burn back and fuse with the
contact tip while welding or after the trigger is released. If the burn back is slight, allow the
tip to cool slightly and remove the tip from the gun feeding extra wire as necessary to get
the tip fully removed. Usually, with a little twisting effort the wire can be removed from the
tip. However, at times the tip may need to be discarded if the burn back has been severe.
If burn back is experienced, it is usually a result of too low of wire speed or too short of a
stick out while welding. Increase wire speed to help prevent additional events of burn back.
8.
Replace the contact tip when the orifice is noticeably enlarged or becomes egg shaped. A
worn out contact tip can cause issues with arc stability. Always make sure you are using
the correct size tip for the application.
GENERAL NOTES: