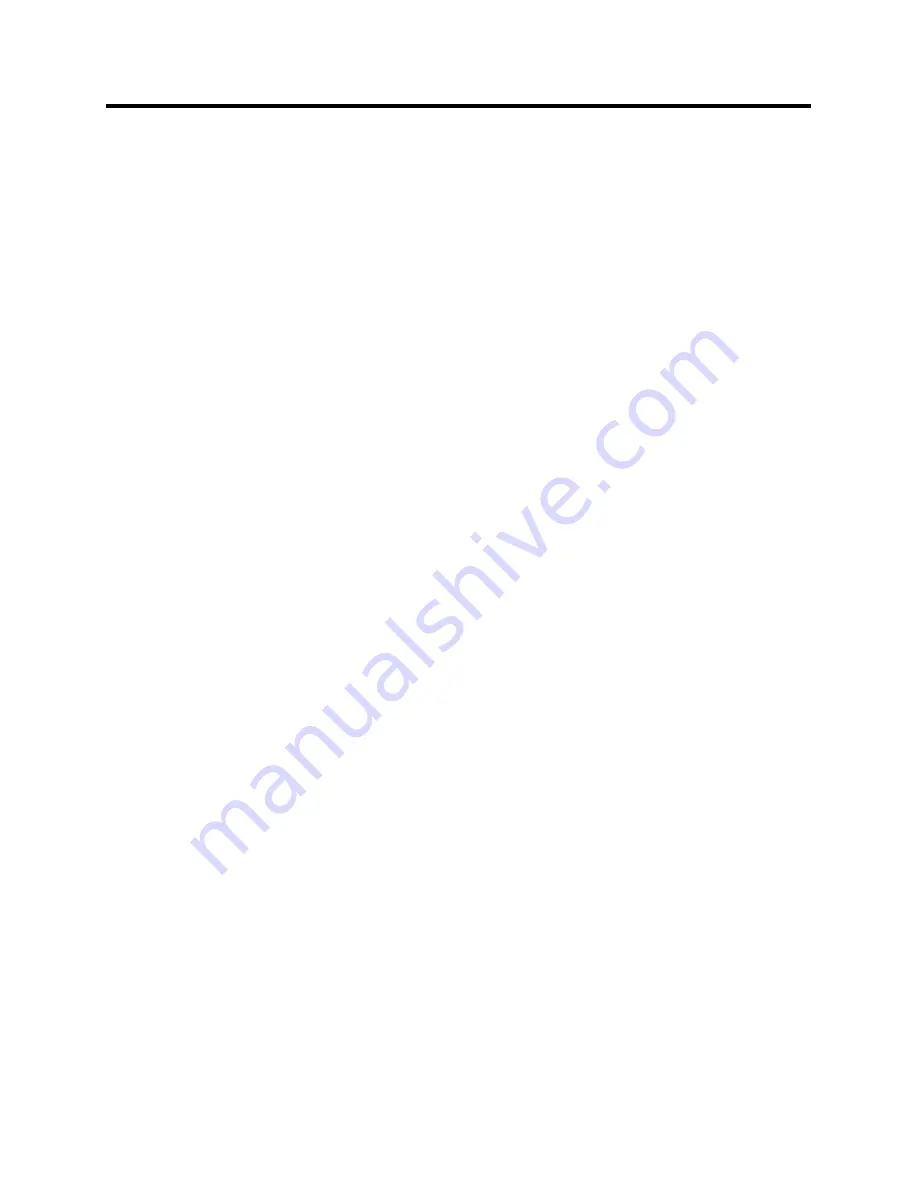
13
violent and irregular. Note that point as well. Lower
the voltage to a point midway between the two ex-
tremes where the arc seems to even out. After the
voltage is set, gradually adjust the wire feed/amps
until the sound of the arc is crisp. Listen to the arc.
A steady sizzle, or whine should be present. The
weld puddle should be wetting out neatly on the
edges of the weld. This sound has often been re-
ferred to as a
“
frying
”
sound. The sound should be
regular, and the arc should be visually stable without
significant popping and snapping. The wire should
be disappearing easily into the puddle without the
arc stopping. If the wire speed is too high, violent
popping with bits of flying wire may be noticed. If it
is too low the arc will appear to melt the wire before
it reaches the puddle and may melt irregularly, even
burning back into the tip.
Volts are responsible for
how flat and wet the puddle appears.
If too much
voltage is used, the weld will appear wide and flat
with the edges of the weld possibly exhibiting under-
cut. This will create weakness in the weld. If too
little is used, the weld will appear rope like and may
even sit on top of the metal with irregular fusion.
Amperage/Wire speed is responsible for penetra-
tion.
If it is set too high for the thickness of metal
being used, burn through can occur, especially on
thin gauge material. If welding thin materials such
as used in exhaust systems or body work, make
sure the wire speed is adjusted to reduce penetra-
tion before attempting a voltage change.
General
figures for both wire speed and amps can be easily
determined.
To determine wire speed, simply press
the trigger (without welding) and hold it for 15 sec-
onds. Measure the length of the wire that is run
from the torch in 15 seconds and multiply by 4.
This figure is your wire speed in inches per minute
(IPM). To roughly determine amps, which are
sometimes used by manufacturers for recommend-
ed settings, use the following formulas for the fol-
lowing wire thicknesses:
.023”:
IPM/3.5 = Amps
.030”:
IPM/2 = Amps
.035”:
IPM/1.6 = Amps
The actual constant given in this formula represents
“
inches per amp
”.
This formula is only a guide and is
only accurate in lower ranges as the function is not truly
linear. But it usually will be within the overall range speci-
fied by the manufacturer. For each manufacturer, the
filler wire diameter amp range may differ somewhat,
though a general range can be established.
1.7
Spool Gun.
The spool gun is an optional, but useful
tool to have for welding small and medium projects alu-
minum projects that are
3/32”
and over in thickness.
The spool gun connects directly in place of the regular
MIG gun. The Spool gun picks up the gas and power at
the Euro connection with a separate control connection
for the trigger on the spool gun. Once the spool gun
panel switch is flipped, the trigger will control on and off
operation of the gun. Wire speed and voltage are still
controlled at the panel however.
NOTE: Some guns
Everlast sells may have a separate control mounted on
the spool gun handle for wire speed, but is inoperative
and is not used with this unit.
When welding alumi-
num, the unit should be welded in the spray arc mode.
Typically spool guns are good for welding
3/32”
and
thicker aluminum. Spray arc mode is a mode where the
voltage is increased to near maximum voltage for this
unit, and wire speed is adjusted so that the wire melts
in a steady stream of consistently sized droplets before
the wire contacts the metal. A slight hiss will be present
if done correctly. There is a threshold for spray arc, and
it requires higher voltage and increased wire speed to
force it into this mode. This is a quieter mode than regu-
lar short circuit with quick wet in and fast forward travel.
It
’
s recommended that
.035”
wire be used to achieve the
best results. In general, the smaller the wire, the more
wire speed is required for spray arc. Due to the wire
feed speed of this unit, a smaller diameter wire will not
result in a successful spray arc needed for aluminum
welding. Larger diameter wire may cause over
-
currents
and may not feed well through the gun. More infor-
mation about spray arc welding with MIG can be found
in a variety of educational welding resources online.
Read over materials available and watch demonstration
videos for more information.
Introduction and Specifications
Section 1