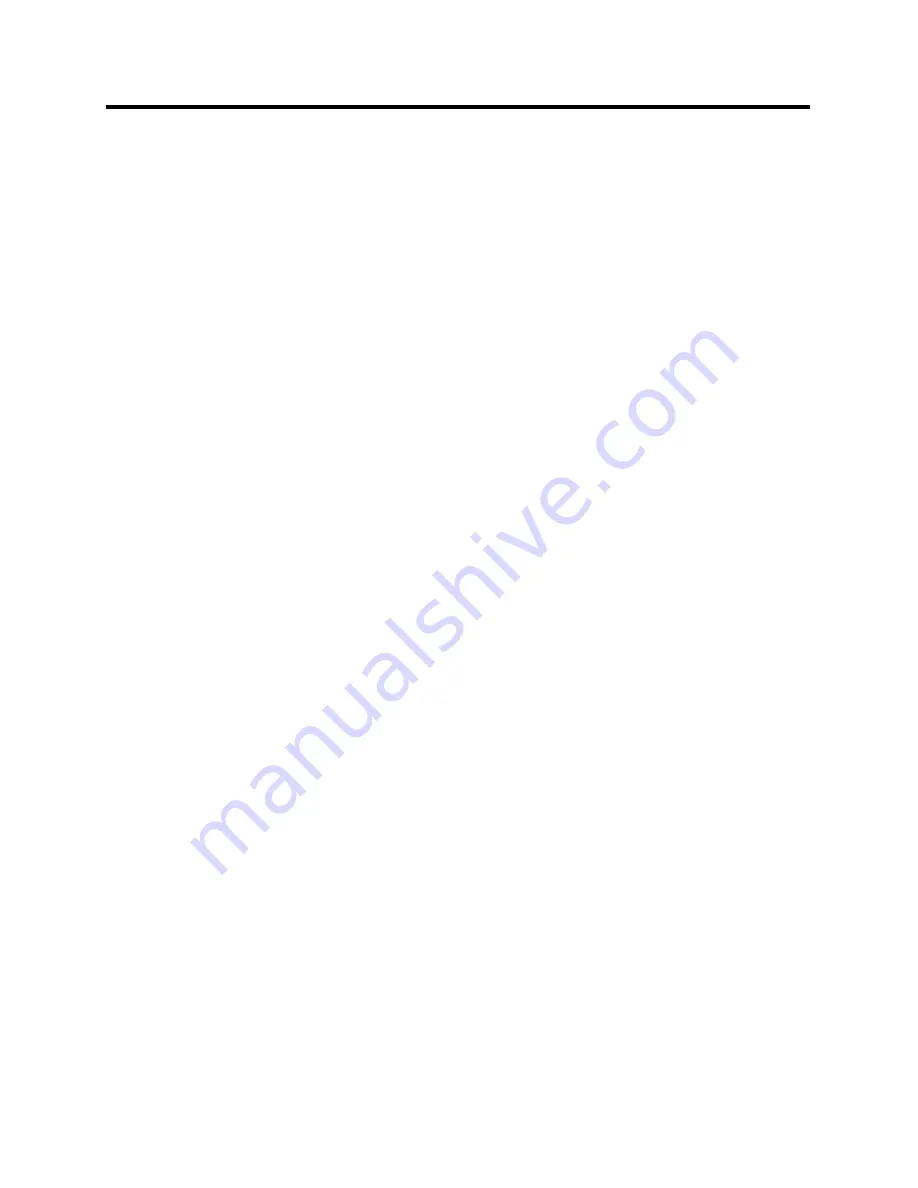
11
welder will stop welding. If this happens, allow the weld-
er to continue to idle and cool for 15 minutes. After giv-
ing the unit time to cool, cycle the power switch off and
back on to reset the welder and resume welding. Lower-
ing the welder output will increase the duty cycle duty
cycle. This welder has a rating of 25% @ 180 amps
when operating 240V and 25% @ 115A when operating
on 120V. (Certain factors like ambient temperature, hu-
midity, particle/dust buildup inside of the welder, poor
quality power input etc, all can affect duty cycle.) Duty
cycle is the amount of time out of a 10 minute time peri-
od that the unit can operate at the rated amperage. For
example, at 180 amps, the unit can operate for 2.5
minutes out of a ten minute time period. The balance of
time the unit should be resting, while switched on with
the fan running. Lowering the amperage results in im-
proved duty cycle ratings. The duty cycle interrupt cycle
is governed by a temperature sensor rather than an actu-
al timer. This is a more effective and practical way of
determining duty cycle limit. Intermittent welding and
many practices involved in fabrication and repair makes it
hard to track usage so a temperature limit is the best
way to protect the welder if it is overworked. Intentional-
ly and consistently exceeding the duty cycle rapidly ages
components and may cause premature failure of the
welder. The duty cycle interrupt feature is not a fail safe
against abuse and any heat related damage.
Never turn
the unit off until it has time to cool.
NOTE: If you are welding and the unit begins to feed
wire only without an arc when the trigger is pressed,
check the status of the duty
-
cycle light or the overcur-
rent light. When either an overcurrent or duty cycle
event has occurred, the unit will keep feeding wire but
not produce an arc when the trigger is held down.
1.5
Overcurrent.
The unit is also equipped with an
overcurrent limiter. This feature detects when there is
either an over/under voltage or excessive amp draw. If
the overcurrent light is triggered, the unit will also inter-
rupt welding. When this is experienced, first power the
unit off. Then check to make sure the unit is plugged into
an appropriately rated outlet and that it is being used
with a correct sized wiring rated for the length of the
wire run. Do not operate this welder with undersized
extension cords or overheating, fire or damage may re-
sult. Cycle the power switch off and back on to reset
the unit. If the Overcurrent light does not clear, then it is
likely the power supply is poor or the unit has developed
an internal fault. Contact Everlast if the overcurrent can-
not be cleared or reoccurs repeatedly as the unit may
have sustained internal damage.
NOTE: When using large diameter welding wire
(.035”
or greater on solid wire) at or near the maximum output
of the machine, the welder may occasionally experi-
ence an overcurrent. This can happen if the wire is not
trimmed to an appropriate length and the gun is
touched held too far away when starting the arc. Rem-
edy all other causes first before assuming this is the
issue. This may also occur if the contact tip is
touched to the metal when starting the arc. It can oc-
cur if the gun nozzle has excess slag bridging inside of
the nozzle to the contact tip and the nozzle is subse-
quently touched to the metal when starting the arc.
This creates a dead short and can trigger an overcur-
rent.
1.6
General operation and setup.
1)
Wire Tension.
Always check wire tension before
use. Use no more wire tension than is necessary.
(See page 15 for adjustment.) Start with a 4 setting.
2)
Work Clamp.
MIG welders require good work clamp
(ground) contact. Routinely inspect work clamp and
cable and make sure they are in good condition and
that the cables are held tight in the connectors and
are free of corrosion.
Always grind a small clean
spot where the work clamp is to be attached. Al-
ways connect the work clamp directly to the metal
being welded if possible. Hard starting or
“
machine gunning
”
at the start of the weld may
be a result of a poor ground.
3)
MIG gun use and maintenance.
Before use make
sure that collar on the Euro quick connect has been
fully tightened by hand. Do not use tools. Grip the
gun firmly when starting the arc to prevent push
-
off
and spattering/popping at the start of the weld.
Trim the wire to
1/4”
or less and hold the gun about
3/8”
off the weldment to start the weld. Use nozzle
dip or a anti
-
spatter spray to help keep the MIG gun
nozzle from becoming plugged with slag. Regularly
check and clean the nozzle. Nozzle dip and anti
spatter can be bought at almost any welding supply
store. It is an economical way to prevent harmful
accumulation of slag in and on the nozzle and can
be used in the weld area to prevent spatter from
sticking to the work
-
piece. Do not apply too much
to the nozzle or directly to the weld area or porosity
may occur. Only apply when the protective qualities
begin to dissipate. Nozzle dip and anti spatter also
provide some lubricity to the contact tip and in-
creases the lifespan and ease of feeding. Make
sure to change contact tip size when changing the
wire size.
Using too large of a contact tip can
cause erratic arc behavior. Using too small of a
contact tip can cause jamming.
When welding with
aluminum, use a special aluminum contact tip or at
least one size larger regular contact tip to accom-
modate the wire as it expands due to the heat. Over
time, the gun liner may become gradually fouled
with dirt, metal filings from the coating and other
possible contaminants. To prevent this, regularly
remove the wire from the cable, and blow dry com-
pressed air down the gun neck with the contact tip
removed. If necessary remove the liner and replace
it if becomes worn and irregular or difficult feeding
or gas flow is observed.
NOTE: (Binzel/Trafimet 15
series) When removing the shielding gas nozzle,
Introduction and Specifications
Section 1