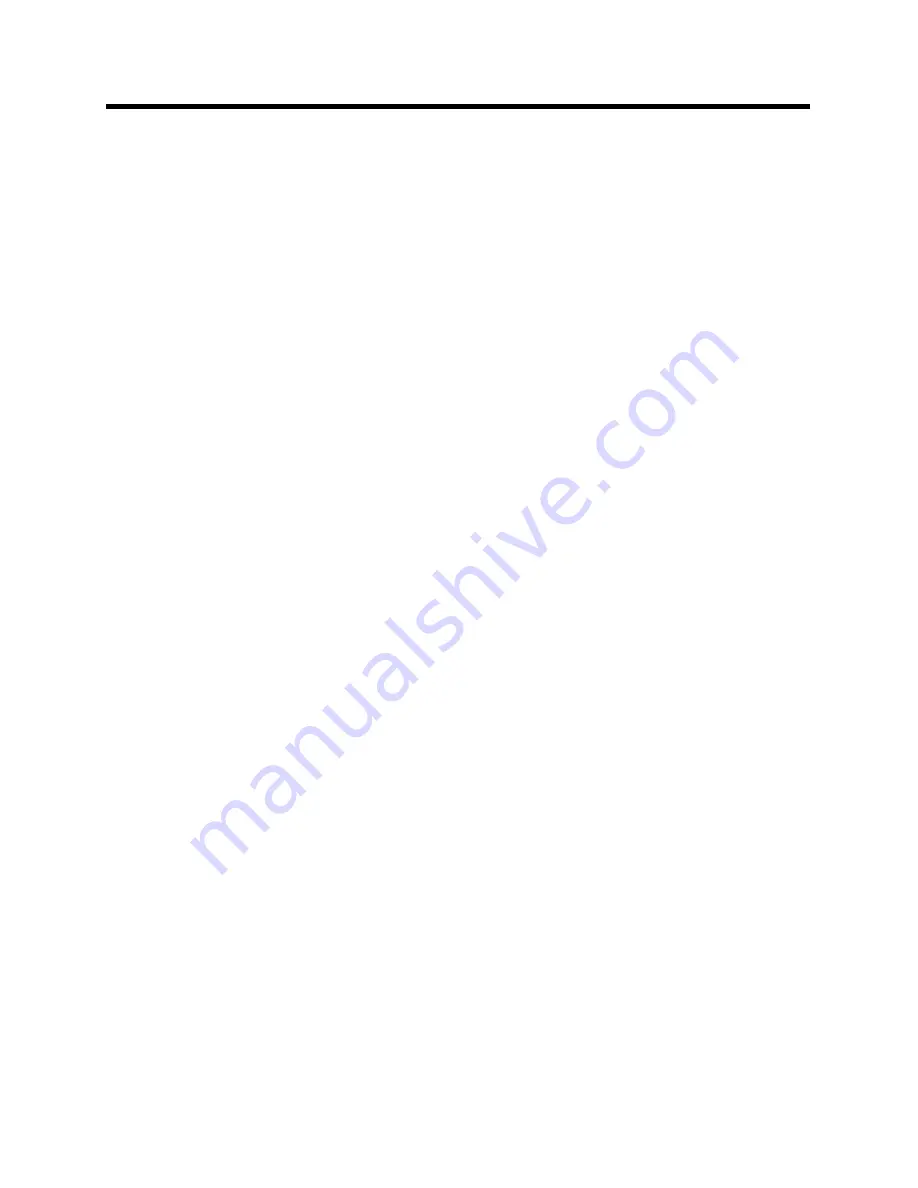
17
Front Panel:
1.
LED Indicators.
The LED
’
S indicate the existing
status of the machine. The On indicator is lit any-
time the machine is turned on . The amber color
light will be lit when the duty cycle has been ex-
ceeded. When it is lit, welding will be interrupted.
(The wire will continue to feed but will not arc
when the trigger is pressed.) If the duty cycle is
exceeded, allow the unit to cool for 15 minutes
before resetting the machine by powering it off
and back on. Do no turn the welder off until the
unit has sufficiently cooled. If the red over
-
current light is lit, welding will also be interrupted.
If this light comes on, an overcurrent/overvoltage
or under voltage has occurred. Check wiring such
as extension cords and circuit breakers for suffi-
cient current carrying capacity. Also check to see
if slag has bridged the space between the contact
tip and the shielding gas nozzle or if the wire stick
out is too long. Occasionally this may occur when
using larger wire
(.035”)
at or near maximum set-
tings with a long stick out of the wire. Once the
cause has been remedied, turn the power off and
back on to reset the welder. If the light does not
clear after remedying the cause, contact Everlast
technical support for further diagnosis.
2.
Voltage Selector.
The voltage selector increases
and decreases the voltage incrementally through-
out the range. Increasing the voltage helps im-
prove wet in and puddle fluidity. Too little voltage
results in a ropey, narrow weld with poor fusion.
Too much voltage results in an erratic, violent arc
and undercutting.
3.
Wire Speed/Amp Selector.
The wire speed se-
lector controls amperage throughout the range by
varying the speed of the wire. The relationship
between wire feed speed and amps is a direct
one. Increasing one, increases the other. Actual
amp output at the same given wire speed will vary
with different diameter wires.
4.
Spool Gun Switch.
This switch changes the units
output to the spool gun. The spool gun connects
to the main Euro connection, and wire speed/
voltage control is retained on the panel.
5.
S
pool Gun Connector.
The spool gun control wire
is connected directly to this 2 pin connector. This
provides On/Off control of spool gun feeding. It
does not provide welding power.
6.
Work Clamp Connector.
This is where the work
clamp connects to the welder. This is a DINSE 25
style connector. The work clamp cable can be
lengthened by removing the rubber cover. Firmly
grip the cover and slide it back. Under the con-
nector is a set screw that retains the cable. If arc
starting becomes irregular or difficult, check to
ensure the work clamp and cable are in good
repair that the cable is tight in the connector.
7.
Euro Connector.
The Euro connector provides
rapid and secure connection of the MIG gun with-
out having to use tools. Use only hand pressure
to tighten the connector. Do not over
-
tighten the
plastic retainer collar. Both the MIG gun and op-
tional spool gun connect to this point. Both the
spool gun and MIG gun cannot be connected at
the same time.
Setup Guide and Component Identification
Section 2