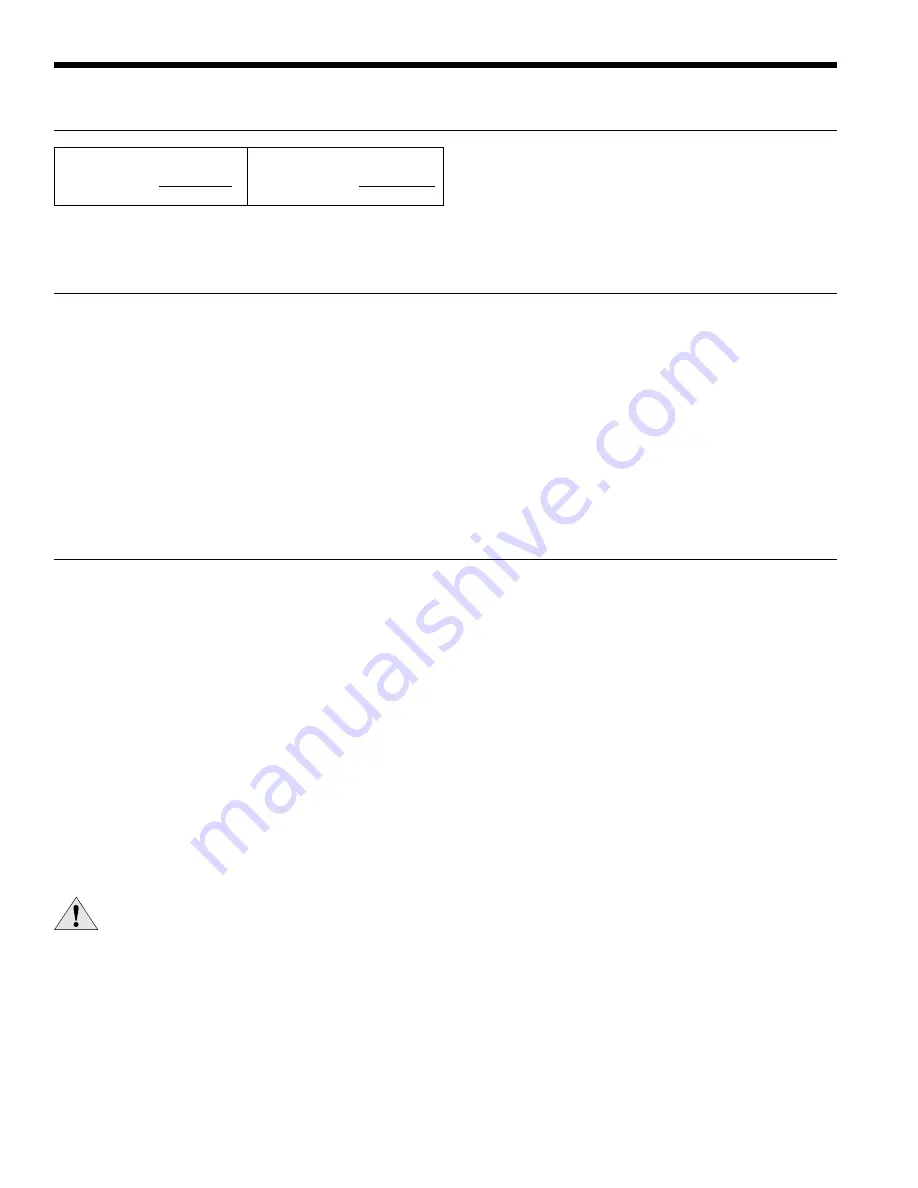
28
NXW REVERSIBLE CHILLER INSTALLATION MANUAL
HE
GPM x 500*
Legend
Abbreviations and Definitions
Reference Calculations
Heating Calculations:
Cooling Calculations:
LWT = EWT +
HR
GPM x 500*
LWT = EWT -
NOTE:
* When using water. Use 485 for 15% methanol/water or Environol solution.
ELT
= entering load fluid temperature to heat pump
EER = cooling energy effciency (TC/KW)
LLT
= leaving load fluid temperature from heat pump
PSI
= pressure drop in pounds per square inch
LGPM = load flow in gallons per minute
FT HD = pressure drop in feet of head
LWPD = load heat exchanger water pressure drop
KW
= kilowatt
EST
= entering source fluid temperature to heat pump
HR
= heat rejected in MBTUH
LST
= leaving source fluid temperature from heat pump
TC
= total cooling capacity in MBTUH
SGPM = source flow in gallons per minute
COP = coefficient of performance (HC/KW x 3.413)
SWPD = source heat exchanger water pressure drop
HC
= heating capacity in MBTUH
HE
= heat of extraction in MBTUH
Verify the following:
High voltage is correct and matches nameplate
•
Fuses, breakers and wire size are correct
•
Low voltage wiring is complete
•
Piping is complete and the water system has been
•
cleaned and flushed
Air is purged from closed loop system
•
Isolation valves are open and water control valves or loop
•
pumps are wired
Service/access panels are in place
•
Transformer has been switched to lower voltage tap if
•
needed (208/230 volt units only)
Unit controls are in “off” position
•
Flow switches are installed and ready or wires are
•
jumpered
Freeze detection setpoints have been set in the
•
microprocessor
WARNING: Verify ALL water controls are open
and allow water flow PRIOR to engaging the
compressor. Failure to do so can result in freezing
the heat exchanger or water lines causing
permanent damage to the unit.
Unit Startup
Startup Steps
Set thermostat control above cooling setpoint.
•
Set thermostat control in cooling mode.
•
Slowly reduce the control setting until both the
•
compressor and water control valve/loop pumps are
activated. Verify that the compressor is on and that
the water flow rate is correct by measuring pressure
drop through the heat exchanger and comparing to the
Pressure Drop table (page 32). Check for correct rotation
of scroll compressors. Switch any two power leads at the
L1, L2, and L3 line voltage termination block if incorrect.
Perform a cooling capacity test by multiplying GPM x
•
∆
T
x 485 (antifreeze/water). Use 500 for 100% water. Check
capacity against catalog data at same conditions.
Set control to “OFF” position.
•
Leave unit “OFF” for approximately five (5) minutes to
•
allow pressure to equalize.
Adjust control below heating setpoint.
•
Set control in “HEAT” position mode.
•
Slowly increase the control setting until both compressor
•
and water control valve/loop pumps are activated. The
reversing valve should be heard changing over.
Perform a heating capacity test by multiplying GPM x
•
∆
T
x 485 (antifreeze/water). Use 500 for 100% water. Check
capacity against catalog data at same conditions.
Check for vibrations, noise and water leaks.
•
Set system to maintain desired setpoint.
•
Instruct the owner/operator of correct control and
•
system operation.