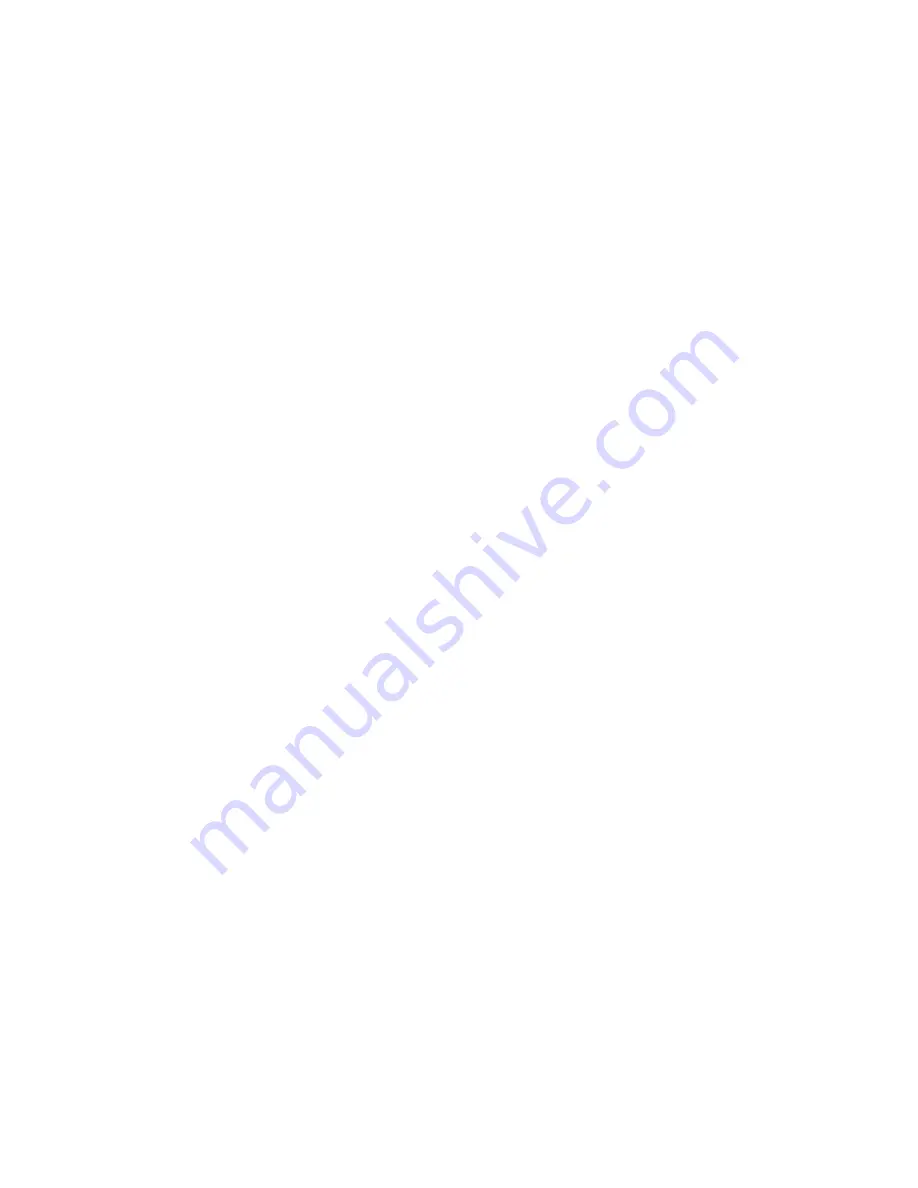
Page 85
8.1.2 USING THE CONSTANT CURRENT PROCESS OUTPUTS
The EN1001, while in any Constant Current mode, can be programmed to provide always,
no matter what is shown on display before beginning of weld sequence, a weld current
readout at the end of any sequence. Several Constant current Process Outputs function as
defined in section 5.4.7 and can be programmed to function as follows.
To obtain an
End of Sequence Readout
, find [
;!:!
] in the Extended Functions and program
a value of [
;!:!
] = 12.
While in the constant current mode, Control will measure the value of current maintained
during the weld and show this value on DATA display at the end of the sequence.
If a window is being monitored for HI/LO range, the value shown on the display will be the
current maintained by the control if the control can maintain this value. If the control cannot
maintain the set current value,
the control will flash LO or HI
(depending on the case).
To obtain an
End of Sequence Readout and Process Output Valve, i.e. Valve 3, alarm
output
, find [
;!:!
] in the Extended Functions and program a value of [
;!:!
] = 13.
While in the constant current mode, Control will measure the value of current maintained
during the weld and show this value on DATA displays at the end of the sequence.
If a window is being monitored for HI/LO range, the value shown on the display will be the
current maintained by the control, if the control can maintain this value. If the control cannot
maintain the set current value,
the control will flash LO or HI
(depending on the case).
In
addition, the Control will turn Valve 3 ON for 1/2 of a second
(30 cycles).
To
INTERRUPT A repeat Sequence or STOP at the end of a weld
, find [
;!:!
] in the
Extended Functions and program a value of [
;!:!
] = 14.
While in the constant current mode, the Control will measure the value of current maintained
during the weld and show this value on DATA displays at the end of the sequence.
If a window is being monitored for HI/LO range, the value shown on the display will be the
current maintained by the control, if the control can maintain this value. If the Control
cannot maintain the set current value,
the control will DISPLAY LO or HI permanently
.
In
addition
, the control will stop a repeat sequence if in the repeat mode or stop the
Control from any further initiations.
In order to re-enable initiations, it is necessary to
simply press any front panel pushbutton to clear HI/LO error.
To obtain a
Weld current Readout without monitoring HI/LO LIMITS
, program
Extended Functions parameter Process Output [
;!:!
] = 12. Program a value in the weld
current parameters [
3O
] = 00.99, or [
3O
] = XX.XX , where XX.XX is close to the maximum
available current. Program a value in the weld current parameters [
7U
] = 00.10. Do not leave
these values at zero. If HI or LO are left at zero, the control uses a default window of current
value+10% for the HI, and current value -10% for the LO, and monitors a default window
as described above.
If any other
non-constant
current
Process
Output
must be used, simply use the SELECT
push-button to indicate Percent Current before weld initiation, as explained in previous
section.
StockCheck.com
Содержание EN1000 series
Страница 2: ...S t o c k C h e c k c o m ...
Страница 19: ...Page 17 Figure 3 6 External SCR Contactor connection S t o c k C h e c k c o m ...
Страница 120: ...Page 118 11 3 TROUBLESHOOTING GUIDE S t o c k C h e c k c o m ...
Страница 121: ...Page 119 S t o c k C h e c k c o m ...
Страница 122: ...Page 120 11 4 BLOCK DIAGRAM S t o c k C h e c k c o m ...