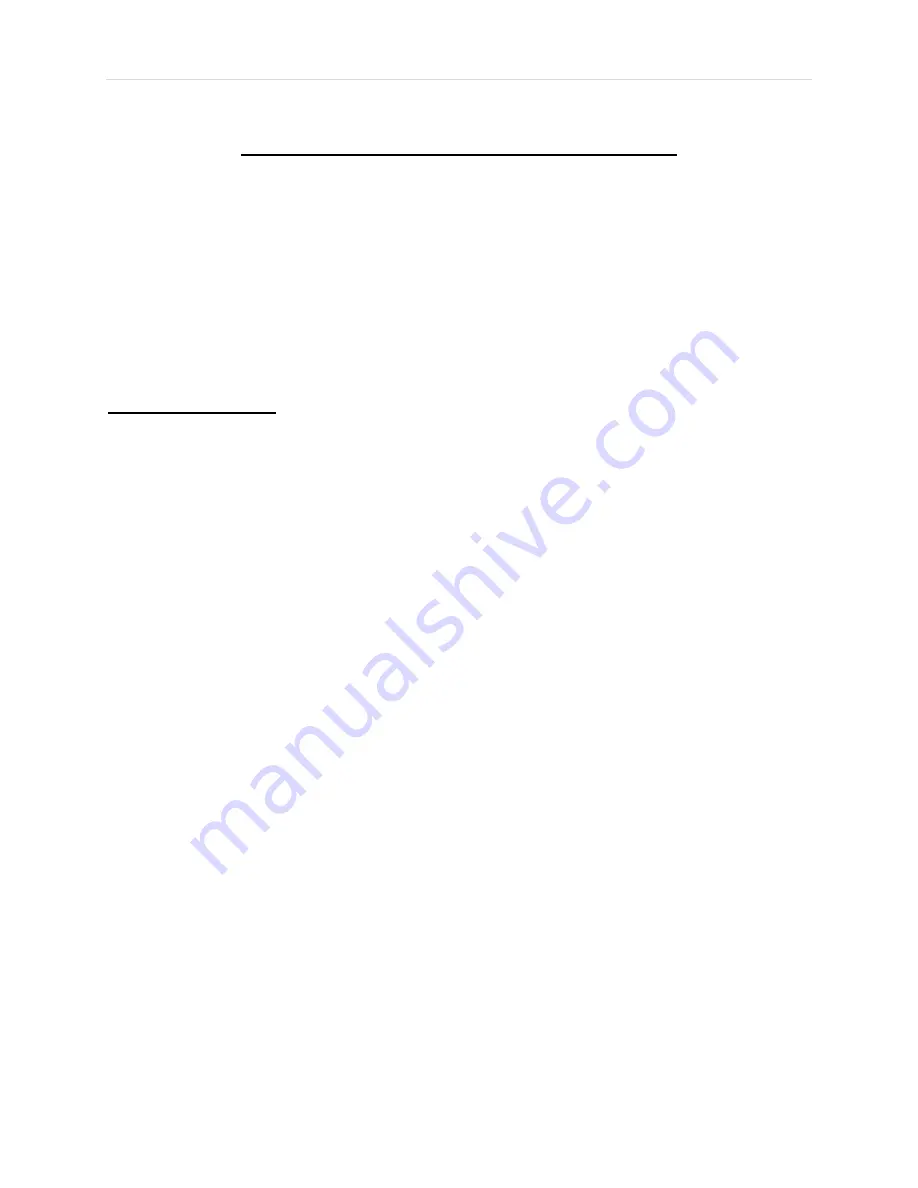
P a g e
|
12
ENERGIZER
BATTERY
MANUFACTURING
VERSION
1.2
Section
3:
Application
and
Design
Considerations
Excessive
exposure
to
air
can
have
an
adverse
affect
on
Zinc
Air
battery
operation,
primarily
due
to
carbon
dioxide
reacting
with
the
electrolyte
in
the
air
electrode.
The
battery
can
also
absorb
water
or
dry
out
depending
on
ambient
conditions.
Balancing
the
air
requirement
of
the
battery
during
discharge
versus
the
need
to
minimize
exposure
during
rest
is
called
air
management.
Air
management
might
be
as
simple
as
removing
the
tab
from
the
battery
and
inserting
it
into
a
device,
or
it
might
include
a
system
to
open
and
control
air
access
to
the
battery
as
needed.
Air
management
is
application
specific,
and
most
devices
will
require
some
degree
of
air
management
to
optimize
battery
performance.
3.1
‐‐
Air
Management
There
are
several
types
of
air
management.
The
simplest
method
of
air
management
is
removing
the
tab
and
putting
the
battery
in
the
device.
This
is
how
miniature
zinc
air
cells
are
used
in
hearing
aids
since
the
total
battery
life
is
typically
expected
to
be
6
‐
8
weeks.
As
the
device
usage
becomes
more
intermittent,
other
methods
of
air
management
are
needed
to
deliver
optimal
battery
performance.
Throttling
is
a
technique
to
permanently
restrict
air
access
to
only
what
is
needed
by
the
battery
in
a
specific
application.
Throttling
is
most
appropriate
in
devices
that
require
a
small
portion
of
the
maximum
current
that
a
battery
can
sustain.
For
example,
a
device
might
require
10
mA
of
current
compared
to
the
maximum
of
100
mA
that
a
PP355
can
sustain.
This
technique
works
best
for
devices
that
have
a
low
average
drain
rate
with
little
increased
power
needs.
By
restricting
the
air
access
to
the
battery,
the
performance
life
can
be
extended.
As
device
use
becomes
more
intermittent
and
as
device
power
demands
increase,
valved
(open
and
shut)
air
management
becomes
more
appropriate.
Valved
systems
are
either
mechanical
or
electronic.
Each
system
requires
a
sealed
battery
or
battery
compartment,
into
which
air
is
introduced
by
the
valve
when
the
device
needs
power.
A
seal
can
be
accomplished
with
common
materials
such
as
o
‐
rings,
gaskets,
over
‐
molded
or
two
‐
part
injection
molded
materials,
or
other
methods.
A
mechanical
solution
might
be
an
ON
/
OFF
slide
switch
which
acts
as
a
simple
air
valve.
Other
device
specific
mechanical
actions
could
also
be
used
to
open
and
close
the
air
access.
Examples
include
changing
device
settings,
moving
a
piece
or
a
part
of
the
device
during
use,
pressing
a
button,
turning
a
dial,
or
manipulating
a
threaded
component.
An
electronic
valve
would
act
in
a
similar
fashion,
except
that
the
device
electronics
would
open
the
air
access
automatically.
A
valve
could
be
opened
as
a
function
of
device
state
(on
=
open,
off
=
closed),
or
it
might
be
a
function
of
the
instantaneous
power
needs
of
the
device.
In
a
valved
air
management
solution,
a
low
level
of
air
access
might
still
be
needed
to
be
able
to
provide
the
quiescent,
or
background,
power
required
to
activate
the
ON/OFF
valve.
Figure
11
shows
generally
where
each
of
these
air
management
techniques
is
appropriate.