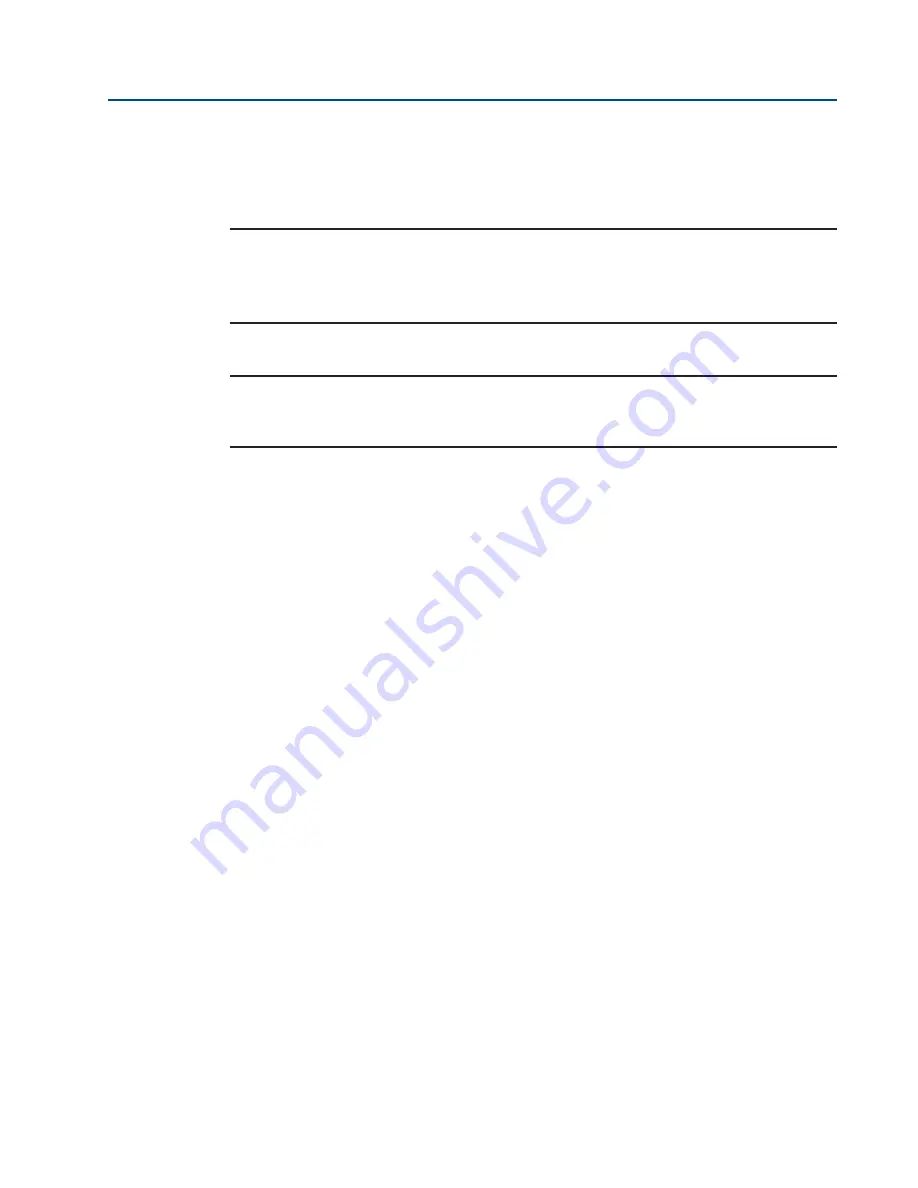
User Instructions
Part Number IOM – 87376-7 July 2016, Rev 1.
9
•
In fail-safe operation, let the actuator run against the stop.
•
Despite the locknut being undone, it must not be possible to screw the end stop
further into the cover flange.
NOTE:
If the stroke is to be shortened by means of the end stop, the actuator must not be in the
fail-safe position. Before adjusting, it is necessary to move the actuator electrically at least 10%
away from the end position.
After undoing the locknut, screw the end stop into the cover flange, and check the adjustment
of the end stop by triggering a fail-safe stroke.
In electrical operation, it is not permissible for the mechanical end stop to be run into. After
adjusting the mechanical end stop, check the setting of the travel end position and correct it if
necessary. After completing the adjustment work, fix the locknuts back in place.
6.4
Adjusting the Hydraulic Damper (If applicable)
The hydraulic damper allows the velocity profile to be adjusted in small degrees in fail-safe
operation. The hydraulic damper is preset and it is not recommended that the setting be
changed. Too weak adjustment of the damper may cause peak forces when the end stop is
reached, whereas too strong adjustment may cause problems during electrical operation in the
fail-safe direction. If, in spite of this, changes are required in the damper setting, proceed with
caution and only make small changes in combination with test runs.
Procedure:
•
Remove the damper cover.
•
There is a graduated dial with an adjusting screw on the end side of the damper.
•
Adjusting to smaller numerical values causes weaker damping and an increase in the
shifting speed.
•
Only adjust by half number values and repeat test runs.
•
After completing the adjustment work, put the cover back on and make sure the
position of the damper to the housing does not get changed during the adjustment
work.
6.5
Final Step
Following commissioning, check for proper sealing the covers to be closed and cable inlets
(see
Section 13.4
). Check actuator for paint damage (by transport or installation) and repair if
necessary.
Section 7: Maintenance
All maintenance work may only be performed with the actuator disconnected from the power
supply.
Due to this requirement, the actuator has to be in the fail-safe position. If this is not the
case, it may be because of a fault in the fitting (stuck fitting shaft).
Содержание RTS FQ
Страница 2: ...User Instructions Part Number IOM 87376 7 July 2016 Rev 1 0 ii ...
Страница 6: ...User Instructions Part Number IOM 87376 7 July 2016 Rev 1 0 iv ...
Страница 7: ...User Instructions Part Number IOM 87376 7 July 2016 Rev 1 v ...
Страница 89: ...User Instructions Part Number IOM 87376 7 July 2016 Rev 1 0 82 ...