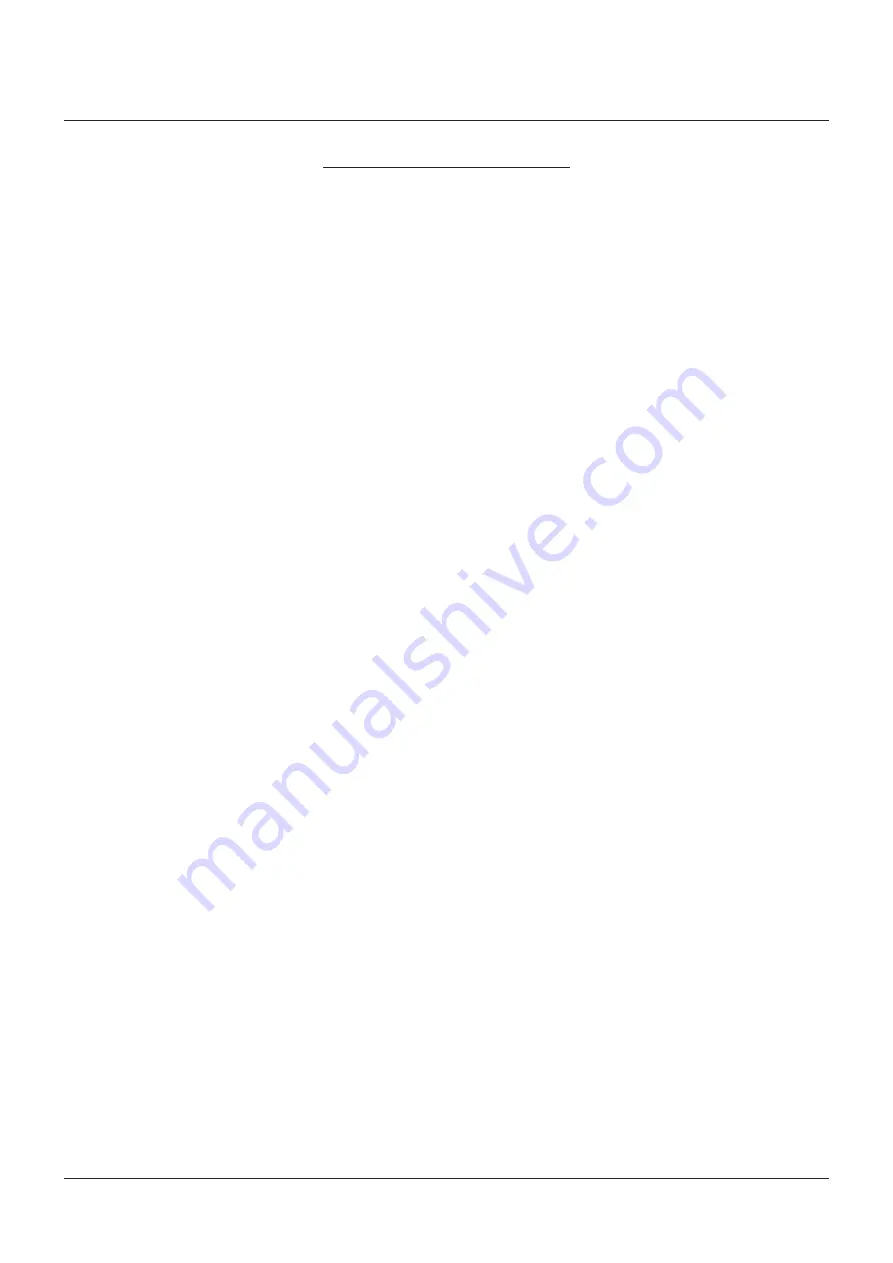
6
Penberthy
SerieS N2/K2 Tubular gagecocKS
InstallatIon, operatIon and maIntenance InstructIons
7.3 troubleshooting
stem packing leakage
- can often be
stopped by tightening the stem packing nut.
if leak persists, the stem packing should be
replaced by following steps 1) through 4)
of the Disassembly and 1) through 7) of the
reassembly instructions
Internal seat leakage
- is an indication of a worn
or damaged stem or seat. To replace the stem
follow steps 1) through 4) of the Disassembly and
1) through 7) of the reassembly instructions. To
renew the seat surface (Series N2), follow steps 1)
through 3) of the Disassembly instructions.
renew the seats by using a fine lapping
compound and a mandrel the same size, shape
and seat angle as the stem. Flush the gagecock
body clean and reassemble by following steps 4)
through 7) of the reassembly instructions.
renewable threaded seats (Series K2). remove
the seat by inserting a ¼" (6 mm) square driver
in the seat and turning it counterclockwise.
install the new seat by turning it clockwise
using the square driver, making sure that the
ball check, if used, is replaced in the body.
Tighten the seat in place.
leakage around union
connections
- can often
be stopped by tightening the union coupling
nut or remake connection using PTFe tape, or
equivalent, on all male pipe threads as shown
in Figure 1.
leakage around stuffing box connection
- is an
indication of worn out glass packing or improper
compression of glass packing. To replace
glass packing, follow steps 7) through 13)
of the Disassembly and 8) through 16) of
the reassembly instructions. in the event of
improper packing compression, leakage can be
stopped by tightening the glass packing nut.
Internal or external corrosion
- could be an
indication of a misapplication. an investigation
should be carried out immediately to
determine the cause of the problem. it is the
user's responsibility to choose a material of
construction compatible with both the contained
fluid and the surrounding atmosphere.
broken tubular glass
- replacement, follow
steps 7) through 12) of the Disassembly and
10) through 16) of the reassembly instructions.
8 reMOVal - dIsasseMbly - reasseMbly
warnInG
Use only qualified, experienced personnel who
are familiar with tubular gagecock equipment
and thoroughly understand the implications of the
tables and all the instructions. DO NOT proceed
with any maintenance unless the gagecock
assembly has been relieved of all pressure or
vacuum, has been allowed to reach ambient
temperature and has been drained or purged
of all fluids. Failure to do so can cause serious
personal injury and property damage.
8.1 disassembly
refer to the exploded parts drawing in Section
11 for additional reference during disassembly
and reassembly of the gagecocks.
1. remove handwheel nut (30), nameplate
(163) (lower gagecock only) and handwheel
(28) or lever (261) from stem.
2. loosen and remove stem packing nut (26).
3. remove stem by turning counterclockwise,
along with stem packing gland (19), stem
packing (25) and stem packing retainer (18).
4. Slip the stem packing gland (19), stem
packing (25) and stem packing retainer (18)
off stem (17).
5. on Series K2 gagecocks, remove bonnet nut
(21) and bonnet (20).
6. To replace seat on Series K2 gagecocks,
follow instructions as described in
maintenance procedures, section 7.3.
7. remove guard rods (40) if present.
8. loosen glass packing nut (37) on both upper
and lower gagecocks.
9. loosen vessel coupling nut (13) on upper
gagecock.
10. Slide tubular glass (48) upward into upper
gagecock until bottom of tubular glass
clears the stuffing box connection on the
lower gagecock.
11. While holding tubular glass (48) in the
upward position, rotate upper gagecock
counterclockwise (approximately ⅛ turn)
to allow clearance to remove tubular glass
from upper gagecock.
12. remove tubular glass (48) from upper
gagecock.
13. remove glass packing nut (37), glass
packing gland (36) and glass packing (34)
from both upper and lower gagecocks.