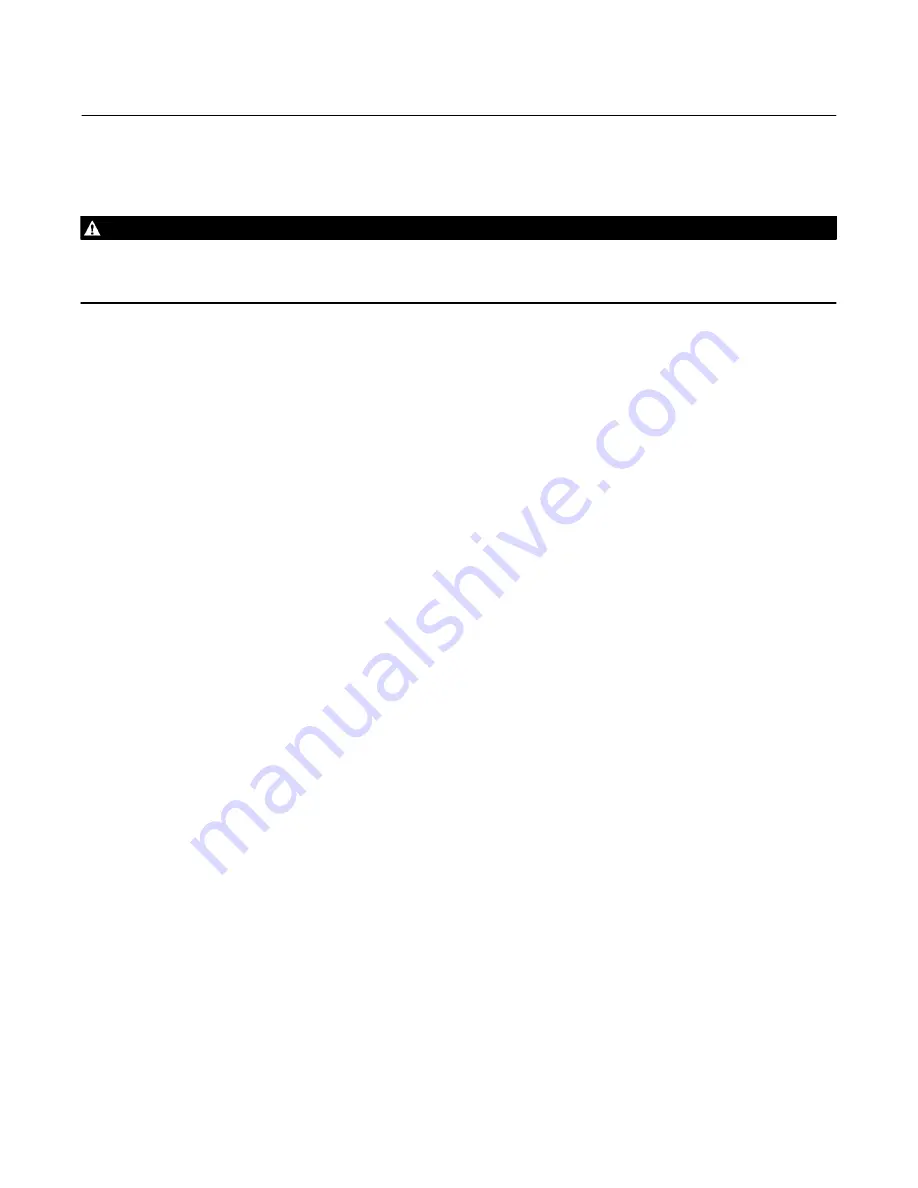
Instruction Manual
D200158X012
4194S Controllers
July 2018
5
Specifications
WARNING
This product is intended for a specific current range, temperature range and other application specifications. Applying
different current, temperature and other service conditions could result in malfunction of the product, property damage or
personal injury.
Specifications for 4194S controllers are listed in table 1-1.
Educational Services
For information on available courses for 4194S controllers, as well as a variety of other products, contact:
Emerson Automation Solutions
Educational Services - Registration
Phone: 1-641-754-3771 or 1-800-338-8158
E-mail: [email protected]
emerson.com/fishervalvetraining