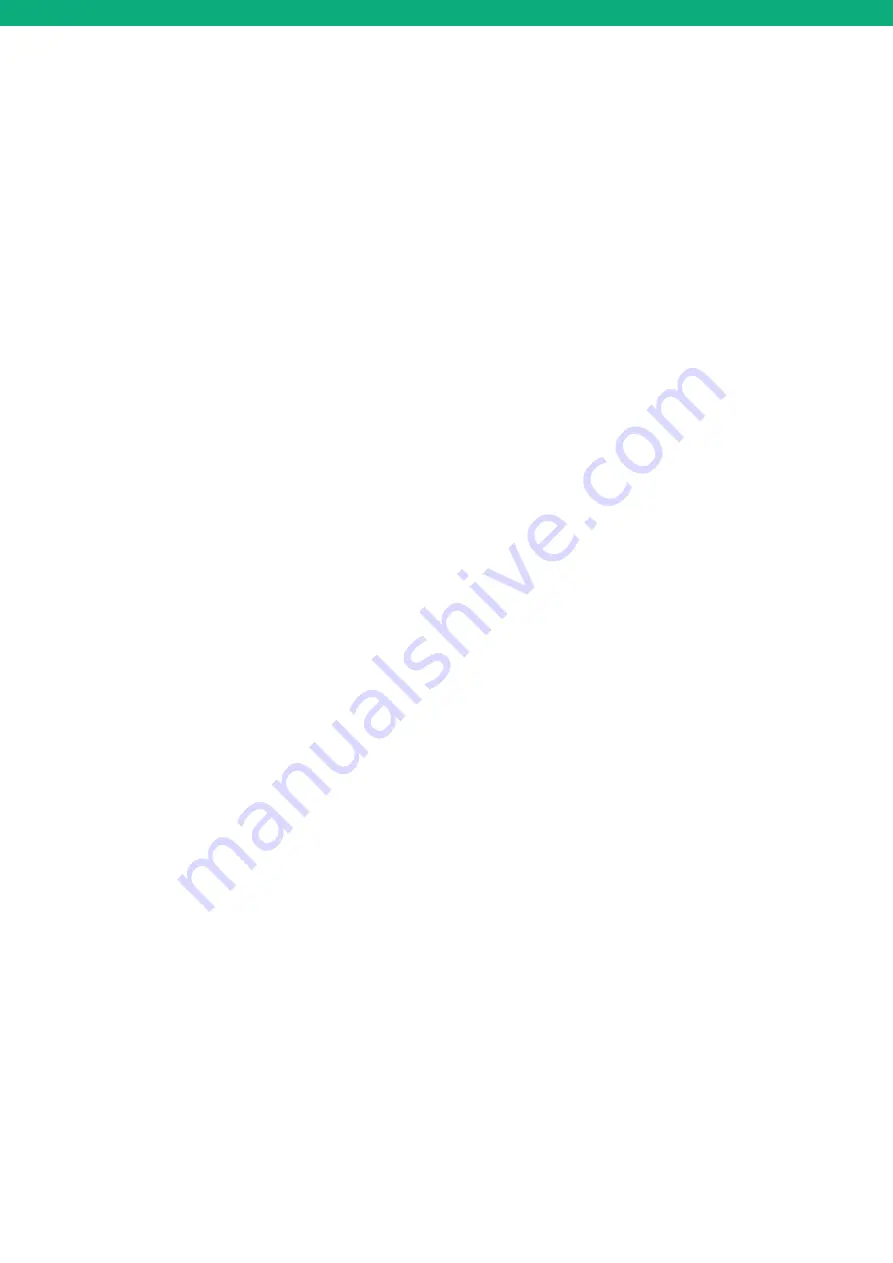
Leak Check
The success of all the subsequent commissioning depends on a leak free system, free of
contaminants, free of oxides, free of non-condensable’ s, that has been evacuated to a
low vacuum and charged with the prescribed refrigerant.
Leak test is particularly important for field-connected systems. Typically, field systems
lose as much as 20%–30% of their refrigeration charge annually. This is not only an unnec-
essary expense but also damages the environment. Compressor oil can be lost at the
same time as refrigerant and eventually lead to compressor failure. (Time spent on leak
test will eventually reduce the time spent on the evacuation process).
Ensure that all service valves are open during the leak test process. It is important to
recheck all joints within the unit as well as the external joints.
a.
The unit is shipped with a holding charge of dry nitrogen and should be leak free.
b.
Ensure that the test pressure do not exceed the system design pressures.
c.
Do not expose system pressure controls HP/LP to test pressures above their design
pressure. This can damage the pressure controls.
d.
Using an approved, calibrated electronic gas leak detector, leak test the entire
system paying attention to all joints.
e.
Periodically check functionality of the electronic leak detector during this process.
f.
To further check system integrity, spray a soapy water solution over joins then
visually inspect for bubbles.
g.
Leave the system under pressure for a designated period (24 Hours).
h.
Check and record the ambient temperatures and the system pressure with calibrat
ed approved instruments. This process is to be carried out every 8-12 hours during
the pressure testing process.
i.
If the test pressures cannot be maintained, repeat the leak testing process employ
ing the isolation of sections of the system to determine the source of leaks. Repair
the leak and repeat the leak testing process until system can be signed off as leak
free and approved by authorized personnel.
j.
Record findings and confirm pressure testing process completion.
Evacuation
a.
After the system is leak checked, connect approved dual stage vacuum pump
sized to application with fresh oil to evacuation valve.
b.
Ensure all inline system shut-off valves and solenoid valves are fully open.
c.
Evacuate the system to 300 microns.
d.
A triple evacuation is recommended. The third and final evacuation should achieve
a value of 300 microns or less. After this vacuum is reached, system is ready for
refrigerant charging and add as much refrigerant as possible into the receiver.
24