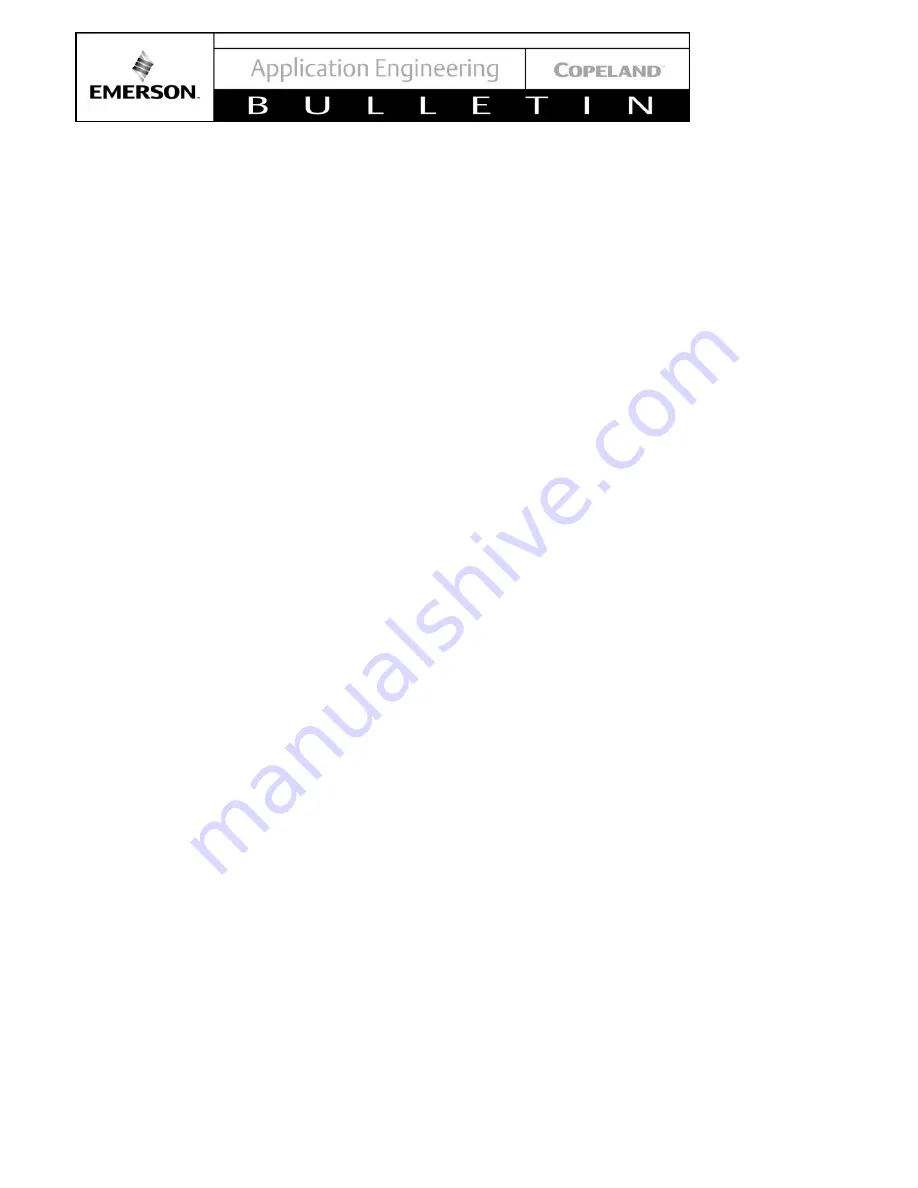
© 2017 Emerson Climate Technologies, Inc.
7
AE4-1414
should be properly insulated. See
Table 6
of
AE-1328
for thermistor temperature vs resistance values. Refer
to
Table 1
for part numbers of discharge line
thermistors.
Figure 6
illustrates the discharge
thermistor.
Motor Overload Protection
The drive will provide motor over current protection in
the event the compressor becomes mechanically
locked or if the load on the compressor motor is
abnormally high. The input power supply to the drive
must be properly fused.
Oil Type
The variable speed scrolls are charged with polyolester
(POE) oil. See the compressor nameplate for the
original oil charge. A complete recharge should be
approximately four fluid ounces (118cc) less than the
nameplate value. Copeland
™
Ultra 32-3MAF, available
from Emerson Wholesalers, should be used if
additional oil is needed in the field. Mobil Arctic
EAL22CC, Emkarate RL22, Emkarate 32CF and
Emkarate 3MAF are acceptable alternatives.
CAUTION! POE oil must be handled carefully and
the proper protective equipment (gloves, eye
protection, etc.) must be used when handling POE
lubricant. POE must not come into contact with
any surface or material that might be harmed by
POE, and spills should be cleaned up quickly with
paper towels, soap and water.
Maximum Tilt Angle
Applications, such as transportation air conditioning or
mobile radar applications, may require the compressor
to operate at some angle from vertical. Service
personnel may be required to maneuver a unit through
a stairwell or other cramped area that might require
tilting the unit. The maximum allowable tilt angles from
horizontal for individual compressors (not tandem or
trio applications) are summarized below:
Max. tilt angle with compressor running = 15°
Max. tilt angle with compressor not running = 60°
Contaminant Control
Copeland Scroll
™
compressors leave the factory with a
miniscule amount of contaminants. Manufacturing
processes have been designed to minimize the
introduction
of
solid
or
liquid
contaminants.
Dehydration and purge processes ensure minimal
moisture levels in the compressor and continuous
auditing of lubricant moisture levels assure that
moisture isn’t inadvertently introduced into the
compressor.
Moisture levels should be maintained below 50 ppm for
optimal performance.
A filter-drier is required on all
R-410A and POE lubricant systems to prevent solid
particulate contamination, oil dielectric strength
degradation, ice formation, oil hydrolysis, and
metal corrosion.
It is the system designer’s
responsibility to make sure the filter-drier is adequately
sized to accommodate the contaminants from system
manufacturing processes that leave solid or liquid
contaminants in the evaporator coil, condenser coil,
and interconnecting tubing plus any contaminants
introduced during the field installation process.
Molecular sieve and activated alumina are two filter-
drier materials designed to remove moisture and
mitigate acid formation. A 100% molecular sieve filter
can be used for maximum moisture capacity. A more
conservative mix, such as 75% molecular sieve and
25% activated alumina, should be used for service
applications.
Refrigerant Piping
Particular attention must be given to the system
refrigerant pipe size with the variable speed scrolls.
ASHRAE guidelines for pipe sizing should be followed
to ensure that refrigerant velocities are high enough at
low speeds to ensure oil return to the compressor. At
the same time, high refrigerant velocities at high speed
operation can result in excessive pressure drop and
loss of system efficiency. A careful evaluation and
compromise in pipe sizing will likely have to be settled
upon. A compressor sample with a sight-tube for
monitoring the oil level should be used during system
development to ensure an adequate oil level is
maintained at operating conditions and speeds.
If testing shows a gradual, continuous loss of oil in the
compressor sight-tube over long run cycles at low
speed, an oil boost cycle should be incorporated into
the system logic. An oil boost cycle is accomplished by
ramping the compressor speed up to a higher speed to
increase the refrigerant flow rate to flush or sweep oil
back to the compressor. Frequency and duration of a
recovery cycle depends on many variables and would
have to be determined through testing for each system
type and configuration. A default method could be to
initiate a recovery cycle at regular intervals.
Long Pipe Lengths / High Refrigerant Charge
Some system configurations may contain higher-than-
normal refrigerant charges either because of large
internal coil volumes or long line sets. If such a system
also contains an accumulator then the permanent loss
of oil from the compressor may become critical. If the
system contains more than 20 pounds (9 kg) of
refrigerant, it is our recommendation to add one fluid
ounce of oil for every 5 pounds (15 ml/kg) of refrigerant
Содержание Copeland Scroll ZPV066
Страница 14: ... 2017 Emerson Climate Technologies Inc 14 AE4 1414 ...
Страница 15: ... 2017 Emerson Climate Technologies Inc 15 AE4 1414 ...
Страница 17: ... 2017 Emerson Climate Technologies Inc 17 AE4 1414 ...
Страница 18: ... 2017 Emerson Climate Technologies Inc 18 AE4 1414 ...
Страница 19: ... 2017 Emerson Climate Technologies Inc 19 AE4 1414 ...
Страница 20: ... 2017 Emerson Climate Technologies Inc 20 AE4 1414 Figure 9 Start Up Procedure Figure 10 Shut Down Procedure ...