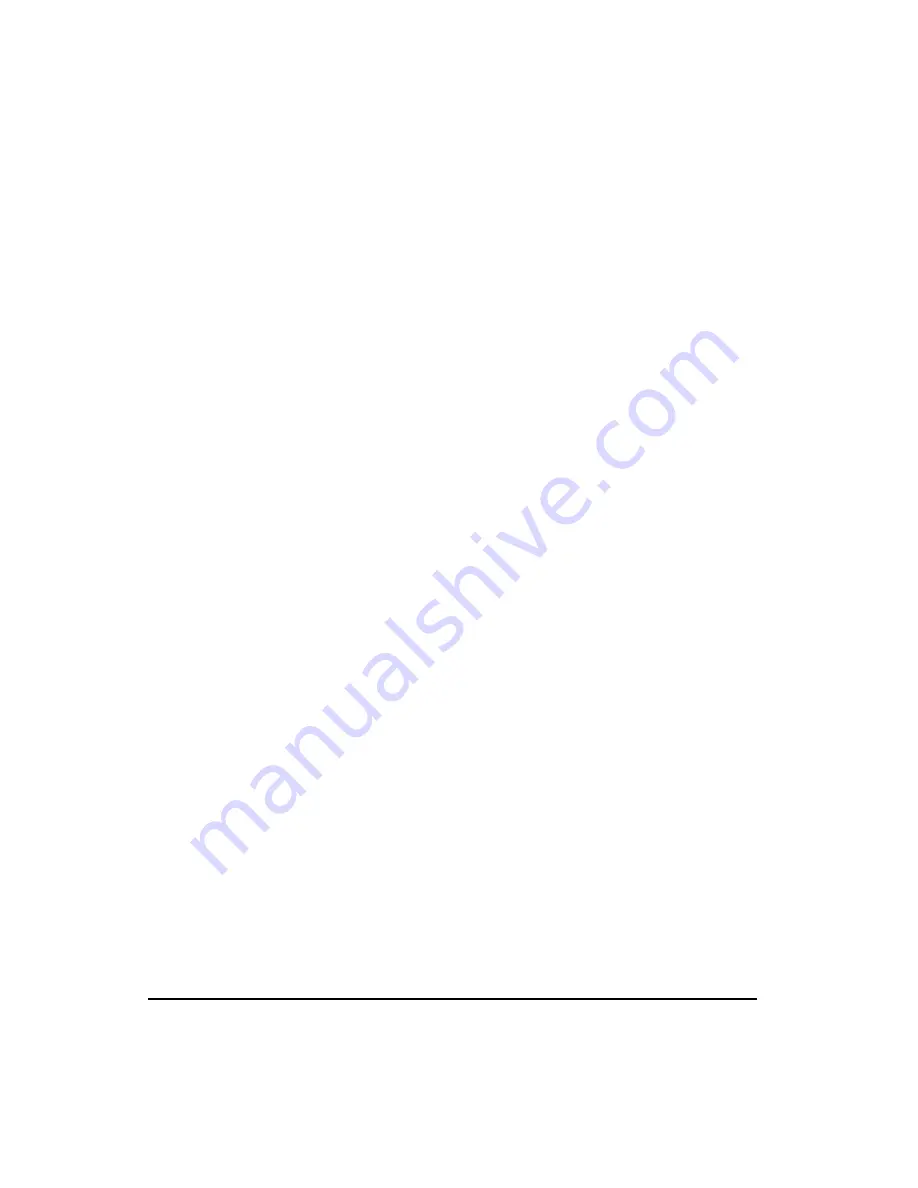
182
Epsilon Eb and EN Drives Reference Manual
signals are wired correctly and the Motor Encoder Reference Motion parameter is
correct.
5. Manually rotate the motor as accurately as you can, CW 20 revolutions. The Position
Feedback should increase by exactly 20 revs. If the change has some significant
fractional part (20.5 for example) the Motor Encoder Lines Per Revolution parameter is
probably wrong.
6. Select "View Motor Parameters" from the
Tools
menu. Note the value of the
Commutation Track Angle parameter. This parameter is obtained directly from the state
of the U, V and W commutation tracks.
7. Slowly rotate the motor clockwise. The Commutation Track Angle should increase in 60
degree steps and will roll over to 0 at 360. If it does not change, there is a fundamental
problem with the U, V and W encoder signals. If it decreases or changes erratically there
is either a problem with the Motor Encoder Reference Motion parameter or the phasing
of U, V and W.
8. Disconnect serial communications by clicking on the
Disconnect
button.
9. Power-down the drive and wait for the status display to go blank and then power the drive
up again.
10. Re-establish communications with the drive by selecting the
Upload
button.
11. Select "View Motor Parameters" from the
Tools
menu. Note the value of the
Commutation Angle Correction parameter. Its value should be zero until the motor
encoder Z channel is detected. Rotate the motor through one or more complete
revolutions until the Z channel is detected.
12. The value should now have a non-zero value between ±40 degrees. If the parameter is
still zero, the drive is probably not seeing the marker pulse.
To confirm this repeat Steps 7-9 several times with different motor shaft starting
locations. If the absolute value of the parameter is greater than 40, there is either a problem
with the phasing of U, V and W or an inconsistency in the encoder alignment parameters.
Torque Test
The purpose of this test is to enable the drive in Torque mode and verify that a positive
command produces CW torque.
1. Use PowerTools to select Torque mode and set Full Scale Torque to 5 percent. Then click
the
Update
button to download the changes to the drive.
With Full Scale Torque set to 5 percent, a maximum analog command of 10 volts will
generate 5 percent of continuous torque in the motor which should be enough to spin the
motor but not to damage it.
Artisan Technology Group - Quality Instrumentation ... Guaranteed | (888) 88-SOURCE | www.artisantg.com
Содержание Control Techniques EN Series
Страница 3: ...Artisan Technology Group Quality Instrumentation Guaranteed 888 88 SOURCE www artisantg com ...
Страница 224: ...205 Specifications Artisan Technology Group Quality Instrumentation Guaranteed 888 88 SOURCE www artisantg com ...
Страница 262: ...Artisan Technology Group Quality Instrumentation Guaranteed 888 88 SOURCE www artisantg com ...