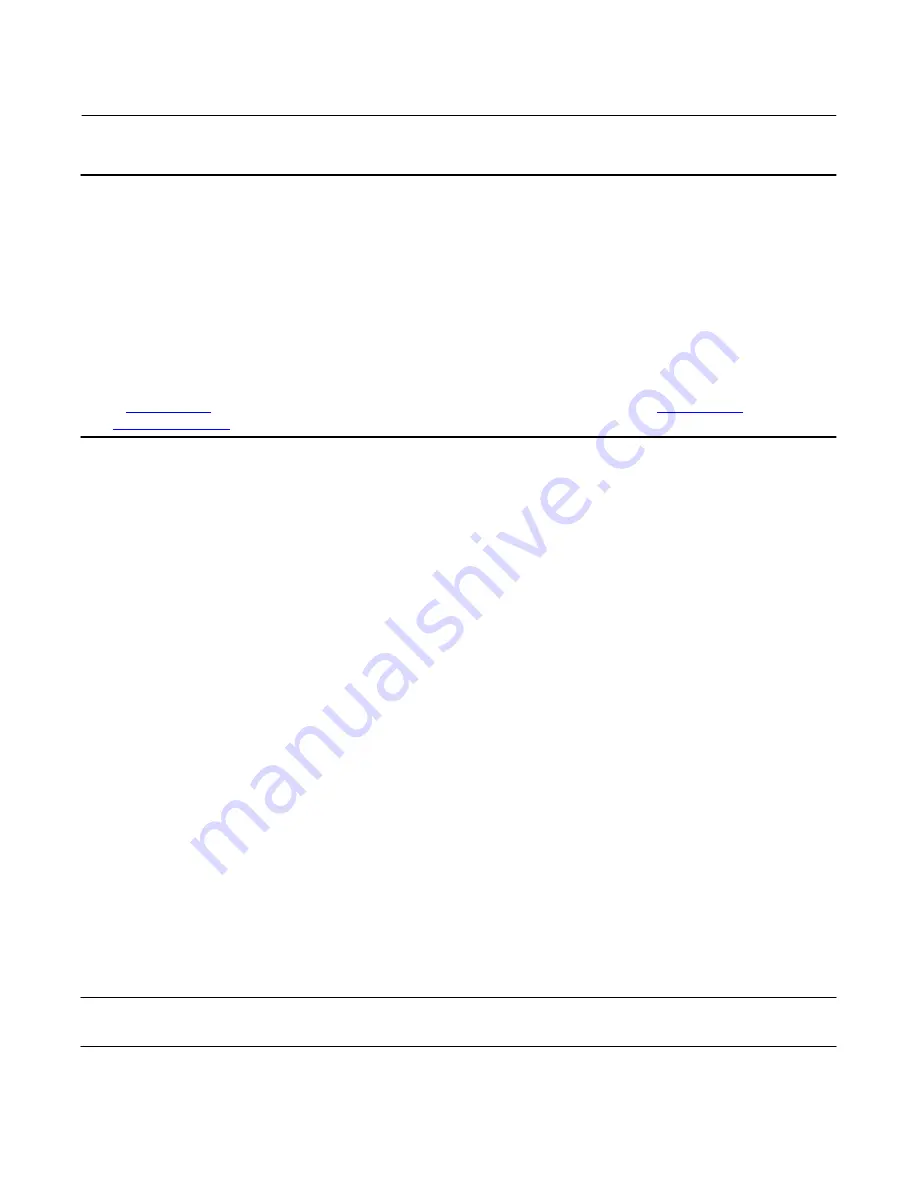
Instruction Manual
D103621X012
4320
January 2018
52
Note
The 4320 also includes a power module voltage warning and a critical power failure alert. These can be viewed through the
gateway web interface. Look under
Monitor
then
Point Data
and select your device from the available HART tags.
There are two fields (true or false) that can be mapped into Modbus, OPC, or DeltaV:
D
TAG.BATTERY_WARNING_GETTING_LOW and
D
TAG.CRITICAL_POWER_FAILURE
BATTERY_WARNING_GETTING_LOW occurs at approximately 6.5 volts, at room temperature, and should be used to indicate that
maintenance should be performed or scheduled soon.
CRITICAL_POWER_FAILURE occurs at approximately 6 volts, at room temperature, and should be used to indicate that
maintenance should be performed or scheduled immediately.
For information on using Modbus or OPC with the 4320 refer to 4310/4320 Wireless Position Monitor OPC System Integration
Guide (
) or 4310/4320 Wireless Position Monitor Modbus System Integration Guide (
your
or Local Business Partner or at www.Fisher.com.
D
Open
or
close stroke time
indicates how long the on/off controller took to previously open or close the valve (not
available in snap-acting mode). Increased stroke time could suggest increased packing or bearing friction, loss of
motive-force, or trim clogging. Decreased stroke time could indicate the loss of process pressure or separated
linkage.
Refer to figure 22 and 23 for the Field Communicator menu trees.
In AMS Wireless Configurator or AMS Device Manager, go to
Service Tools, Variables,
then select the Valve tab
to view
Last Close Stroke Time
or
Last Open Stroke Time
and the
Dwell Time
in the current state, as shown in figure 28.
D
Opened/high
or
closed/low dwell time
indicates how much time has elapsed since the switch state last entered
opened/high or closed/low region. This can be used to determine when the valve last moved.
Transition Dwell
provides the total elapsed time the valve was in the transition state between limits. This was
initially implemented for safety relief valve monitoring applications to eliminate the need of calculating the
difference of timestamps sent to the control system host. This refers to the time the valve was not closed. In order
for this feature to report correctly you must first map to the Transition Dwell as a published variable. Go to
Configure
,
Manual Setup
and click on the Wireless tab. Select View/Configure Message 0 (or whichever message is
publishing
Selected Device Variable
). Click on Modify, then set Transition Dwell as one of the published variables.
Click on Accept.
Refer to
Dwell Tracking
and
Tracking Debounce
under Operational Options on page 37 to enable and refine the Dwell
Tracking feature.
Refer to figure 22 and 23 for the Field Communicator menu trees.
In AMS Wireless Configurator or AMS Device Manager, go to
Service Tools, Variables,
select the Dwell tab and
Read
Dwell Variables
to view
opened/high
or
closed/low dwell
and
transition dwell
times, as shown in figure 29. If
communicating at the maintenance port, the
Read Dwell Variables
button does not appear, the Dwell Times are
directly available on the Dwell tab.
Note
The screen shot in figure 29 is for a wireless connection.