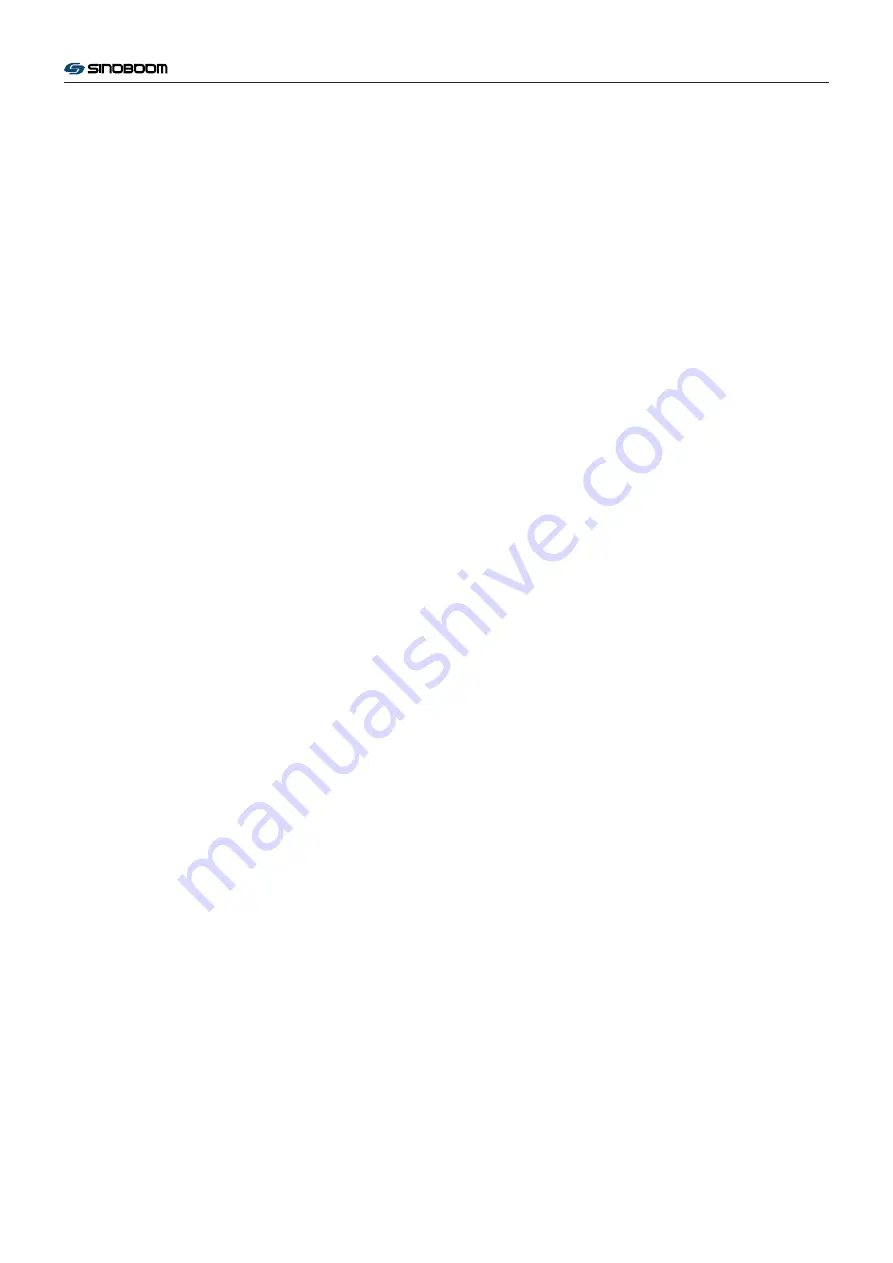
Operating Procedures
Energy
Two 12V lead-acid storage battery are connected in
series and drive one 24V DC motor. The gear pump is
connected to the output shaft of the motor with the
spline to provide power for the system.
Hydraulic System
The entire hydraulic system of the machine is divided
into two parts: one is for steering function and the
other is for platform up and down functions.
When the motor works, the hydraulic pump will
deliver the pressure oil to the functional valve block
on which the directional valve is installed and is used
to complete different actions. For protecting relevant
components, and prevent the system overloading, the
valve block is fitted with overflow valve.
Electrical System
2 separated batteries (12V) are used in the system,
which are used for driving pump controlled DC motor
and traveling drive motor, controlling scissor arm up
and down, traveling and other functions. Batteries are
charged by external power.
Machine Control
The functions of the machine are controlled with one
controller in this system. This controller is installed in
the ground control box. The controller exchanges data
through a high-speed data bus.
Safety Measures
A series of angle sensors and limit switches provides
signals to the controllers. The level sensor measures
the angle of vehicle body on axis X and axis Y; when
the angle on axis X exceeds 1.5° or the angle on axis
Y exceeds 3°, the alarm will be triggered, and the
machine could not lift, travel or turn.
The stroke switch is used for confirming whether the
pit protection mechanism is turned on into position.
The platform will stop ascending if it is about 2m
away from the ground, the pit protective plate fails to
be spread and the sensor fails to detect any signal.
4
GTJZ0407SE
Maintenance Manual