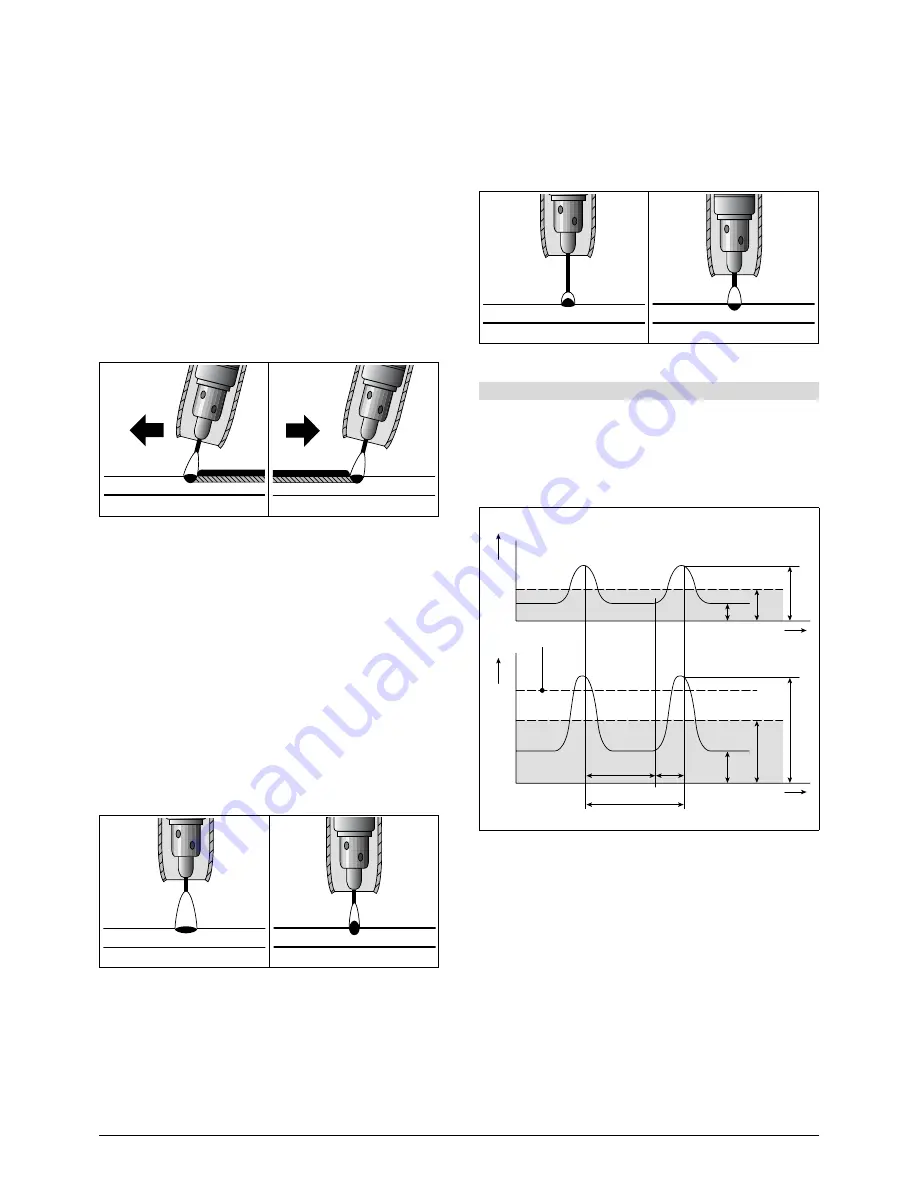
14
Holding and manipulating the torch
)
Metal shielded gas welding can be welded in all posi-
tions: horizontal, vertical-down, vertical-up, overhead
and in horizontal-vertical position.
At horizontal welding hold the torch vertical to the workpiece
(neutral torch position) or up to 30° “pushing” the torch. At
thicker welds, a slight dragging motion is sometimes used.
For best depth of penetration and covering of shielded gas is
the neutral position of the torch the most suitable one. Please
notice if the torch is tilted to far, it could be that possible that
air will be sucked into the shielded gas atmosphere (injection
effect).
At vertical and overhead welding a slight pushing motion is re-
quired. Vertical down welding is most used for thin materials,
for this kind of weld hold the torch at the neutral or slightly
“dragging” position. For this kind of welding is some experi-
ence required cause the welding pool could run ahead and
cause some lacks welding. With thicker material there is a
danger of lacks of fusion cause the welding pool is very liquid
due to high voltage.
Avoid extreme side to side movements to avoid that the weld-
ing pool will be damed up in front of the arc. This could cause
lacks of fusion due to the welding pool flows ahead of the
welding spot. The side to side motion should only be as wide
as is necessary to reach both sides of the joint. If the joint is
wide enough you should weld two parallel string beads.
At vertical-up position the side to side motion should describe
the shape of an open triangle.
Length of the arc
Welding with a longer arc reduces the penetration, the weld-
ing bead is wide and flat with increased spattering. The weld-
ing material is transferred with slightly larger drops than at
welding with a shorter arc. A longer arc is useful for welding a
fillet weld to form a flat or concave seam.
Welding with a shorter arc (at the same amperage) increases
the penetration, the welding bead is narrow and high with re-
duced spattering. The welding material is transferred with
smaller drops as long as the welder is not welding with short
arc.
Length of the wire electrode
The distance between the torch and the workpiece should be
10 – 12 times the diameter of the wire. Altering the distance
of the torch will influence the length of the electrode end.
A longer electrode end reduces the amperage and the pene-
tration.
A shorter electrode end increases the amperage if the wire-
feed speed remains the same.
Current and voltage pulses
Material transfer is achieved by current and voltage pulses
controlled at the same rate as the pulse frequency. The arc
power is changed by the ratio between basic and current
pulses, the pulse duty factor between basic and current puls-
es and the pulse frequency.
Welding direction dragging
Welding direction pushing
Long arc
Short arc
14 Basics of pulsed arc welding
Long electrode end
Short electrode end
U
g
u
s
[v]
U
m
U
p
l
g
t
g
T
p
= 1/ f
p
kritische Stromstärke
t
p
i
s
[A]
t[s]
t[s]
l
m
l
p
Содержание MULTIMIG 400puls
Страница 2: ...2 5 5 6 10 8 9 6 7 12 15 14 11 10 ...
Страница 19: ...19 Appendix mounting torch holder ...
Страница 20: ...326601 06 05 ...