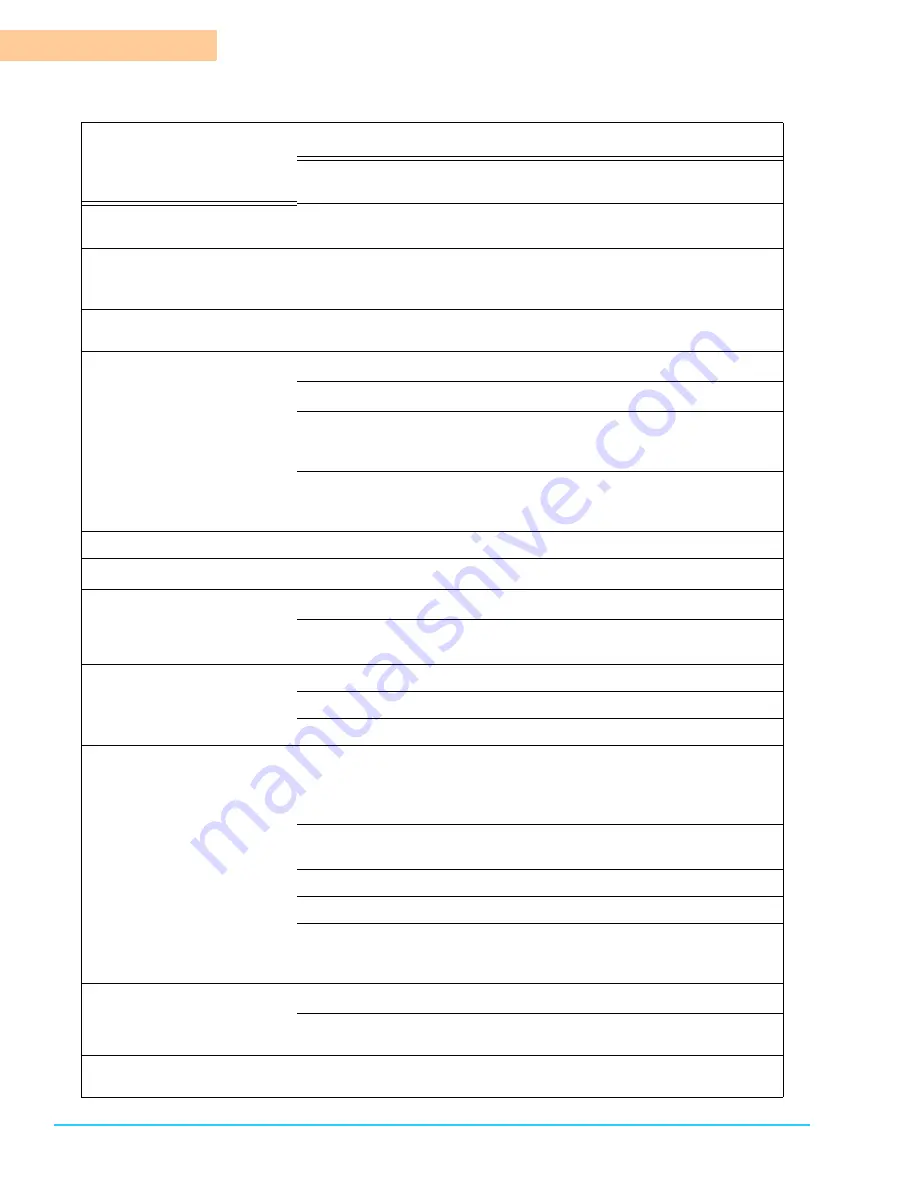
-122
Bravo™ Programming and Operations Guide
Rev. 2
0
Over–printing of leading contact area causes the paste to squeeze out under the compo-
nent. Use “home plate” aperture design to reduce the leading contact area of the paste.
o
Solder mask problems due to the thickness of the mask causing a different capillary
action. A rapid ramp up profile in the 1.5° to 2.5° C range may correct the problem.
p
Cracked Solder Joints
Result of physical flexing or thermally induced stresses on an assembly from cycling
beyond the recommended range. Also consider a flaw design style in the component
(necessitating a change to a different component.
q
Higher Amount of Residue than
Expected
Temperature below the paste’s heat requirement
r
Voids
Incompatibility between the profile and the paste
s
Incorrect profile especially in preheat/preflow to allow solvent to evaporate
t
Insufficient dwell time above liquidus (TAL)
u
. Refer to solder manufacturer’s paste speci-
fications to ensure TAL meets requirements needed for gas to separate and escape from
the molten solder.
If adhesive is used, ensure a slow–enough ramp rate to avoid voids formed by trapped
volatiles. If glue is cured too fast, it can skin over and the remaining volatiles or moisture
in the glue may form voids.
v
Excessive Intermetallic Compound
Oxidation of the Paste
Stayed in soak zone too long
w
Slump Formation
Too rapid rise in preheat temperature
x
High ambient temperature, particularly on fine pitch where the ration of height to width is
large.
y
Coplanarity
Warped boards
Uneven solder surfaces
Poor component fabrication or handling
Bridging
Excess solder deposition from inadequate or infrequent underside stencil wiping.
Increase automatic stencil wiping to prevent bridging.
z
Also, more frequent cleaning is
required at slower print speeds because of the increased time that pressure is applied to
the paste in the apertures during printing.
aa
Improper stencil design. Ensure that the stencil design incorporates a 1 – 3 mil reduction
from the pad to minimize squeeze–out and avoid bridging.
ab
Possible board or component contamination
Misaligned component
Pad Geometry and stencil apertures have a much more significant impact [on bridging
than the reflow oven]. If their geometries aren’t suitable, then no oven can change the
bridging defect.
ac
Insufficient or Non–wetting
Base metal may be visible on the PCB — contact the supplier
ad
Excess soak time may deplete the flux before soldering, adjust the parameters, keeping
within the solder manufacturer’s specifications
Tombstoning
One side of the board melts before the other side. Adjust profile or board components;
inspect heat sinking
Problem
Possible Cause(s)
Solder Beading (cont.)
Содержание Bravo 8105
Страница 2: ...Bravo 8105 Programming and Operations Guide ...
Страница 14: ...T A B L E O F C O NT E N T S xiv Bravo Programming and Operations Guide Rev 2 ...
Страница 42: ...T E C H N IC A L D A T A Electrical Information 2 28 Bravo 8105 Programming and Operations Guide Rev 2 2 ...
Страница 90: ...A LA R M S Alarm History 7 76 Bravo 8105 Programming and Operations Guide Rev 2 7 ...
Страница 126: ...M A IN T D IA G S C R E E N S PLC Status 10 112 Bravo 8105 Programming and Operations Guide Rev 2 10 ...