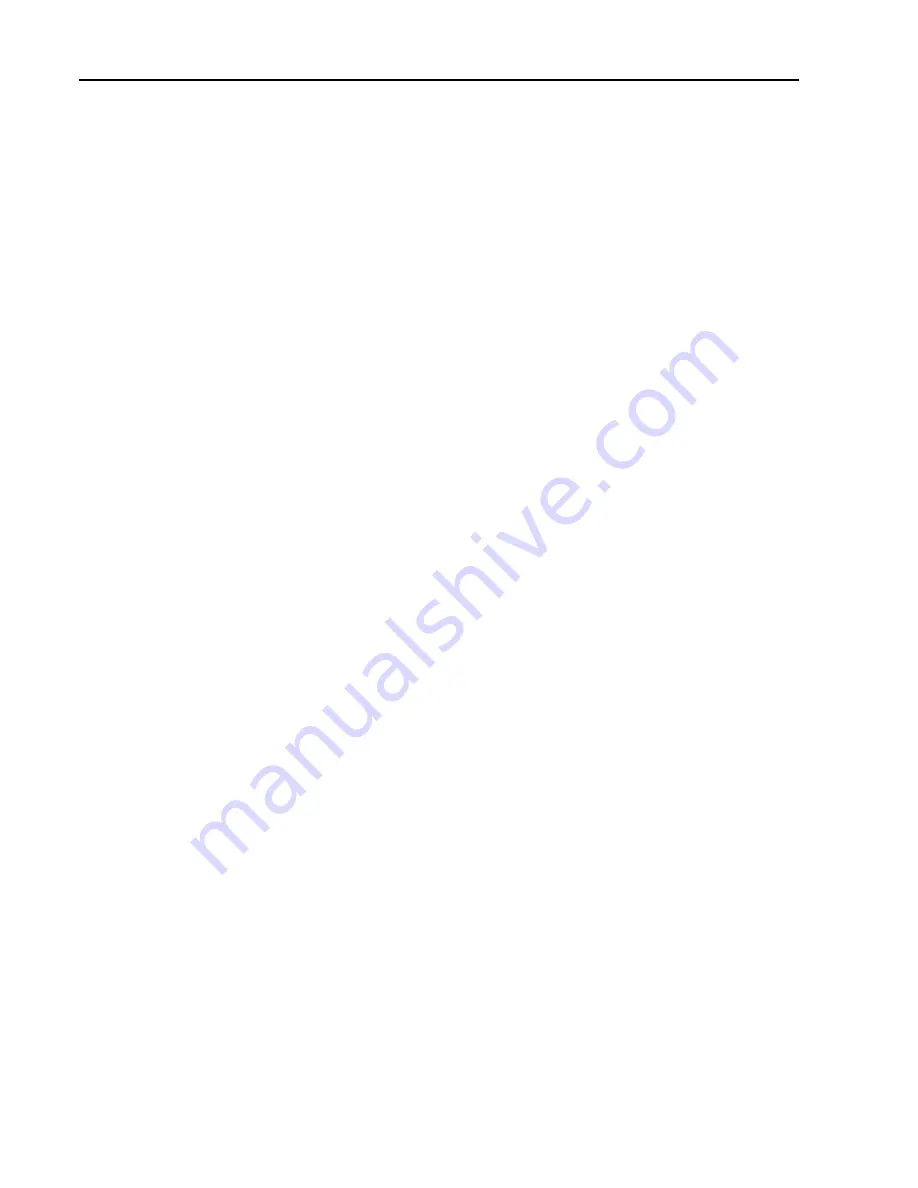
106
Service Manual
40:22 I/O BOARD MISHMASH
The error code is shown if wrong Type of I/O unit is fitted.
Could also occur if adressessing of the I/O units is made in a incorrect way.
After addressing of I/O units the CPU reads the Type of each unit.
If there is a mismatch between what the Type of I/O unit the CPU finds, and what the I/O unit type the software con-
figuration expects, the error will be shown.
Machine will not run until problem is solved. There are two exceptions: I/O type 1 can be used when I/O type 11 is ex-
pected, but not oposite. I/O type 8 can be used when I/O type 81 is expected, but not oposite.
Possible causes:
• When adressing the I/O units the operator has pressed a the button on the wrong I/O unit.
• Wrong type of I/O unit if fitted in the machine.
• Two I/O units have got the same adress.
Recommended actions:
1. Readdress all I/O units.
Use
I/O CONFIGURATION
function in service mode.
Alternatively use Common Service Tool, I/O addressing function.
2. Use the electric schematic to find correct I/O board to address.
3. Use Common Service Tool, I/O addressing function to get best overview/visualization of the problem.
Содержание T5190LE
Страница 1: ...Service Manual Tumble dryer T5190LE Type N1190 Original instructions 438 9167 00 EN 2017 02 09 ...
Страница 2: ......
Страница 30: ...30 Service Manual Demount the control panel fig 7967A Demount the supporting rail fig 8044 ...
Страница 35: ...Service Manual 35 Demount the control panel fig 7967A Demount the supporting rail fig 8044 ...
Страница 40: ...40 Service Manual Demount the control panel fig 7967A Demount the supporting rail fig 8044 ...
Страница 45: ...Service Manual 45 Demount the control panel fig 7967A Demount the supporting rail fig 8044 ...
Страница 117: ......