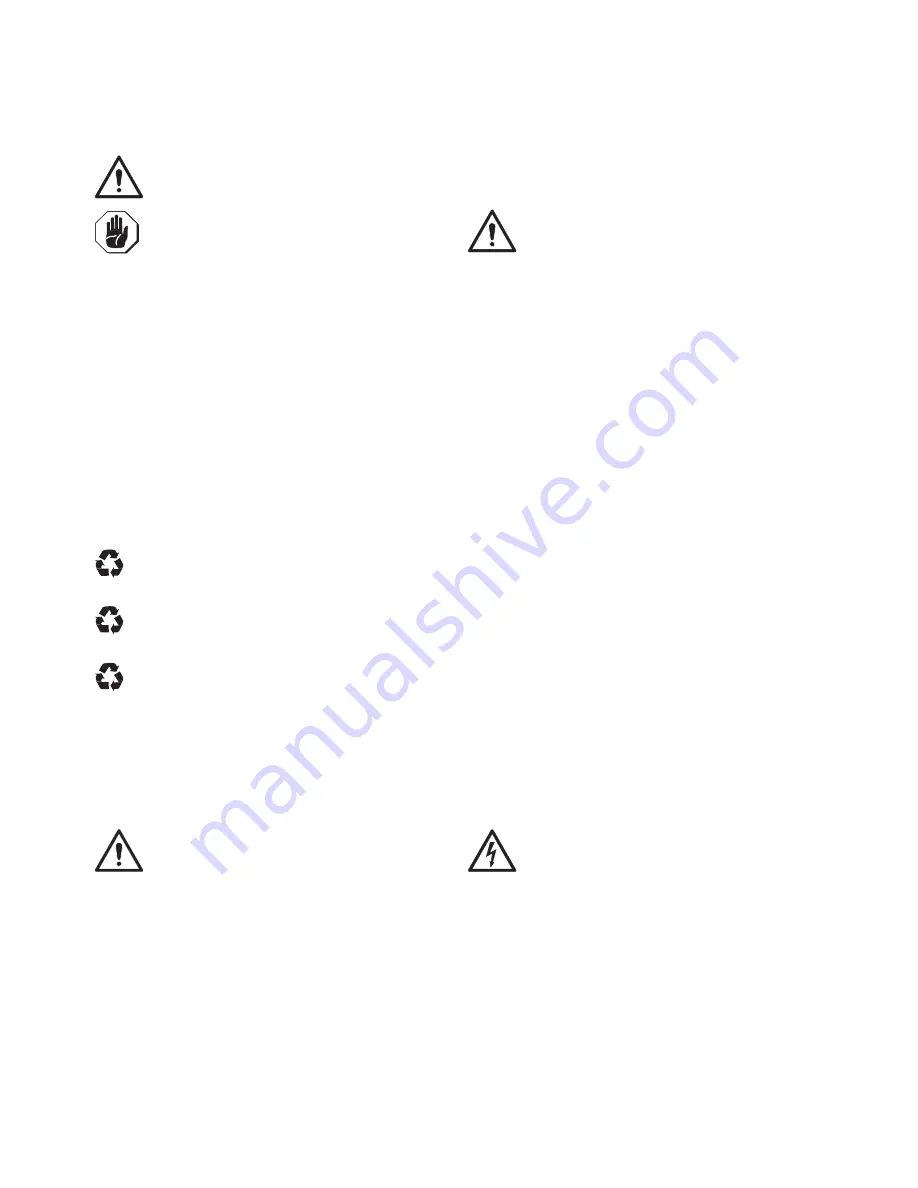
32
can operate is +43°C.
The machine must be taken to the place of installation and the
packing base removed only when being installed.
Arranging the machine:
• position the machine in the required place;
• adjust the height and levelling with the adjustment feet, also
checking correct door and drawer closing:
ATTENTION!
The appliance must be levelled; otherwise its
operation could be affected.
NOTE:
The plug must be accessible even after the appliance
is positioned in the place of installation.
• wear protective gloves and unpack the machine, carrying out
the following operations:
- cut the straps and remove the protective film, taking care
not to scratch the surface if scissors or blades are used;
- remove the cardboard top, the polystyrene corners and
the vertical protection pieces.
For appliances with stainless steel cabinet, remove the protective
film very slowly without tearing it, to avoid leaving glue stuck to
the surface. Should this happen, remove the traces of glue with
a non-corrosive solvent, rinsing it off and drying thoroughly; it is
advisable to go over all the stainless steel surfaces with a rag
soaked in paraffin oil in order to create a protective film.
B.2.4 DISPOSAL OF PACKING
The packing must be disposed of in compliance with the current
regulations in the country where the appliance is used.
All the packing materials are environmentally friendly. They can be
safely kept, recycled or burnt in an appropriate waste incineration
plant. Recyclable plastic parts are marked as follows:
PE
polyethylene:
outer wrapping, instruction
booklet bag
PP
polypropylene:
straps
PS
polystyrene foam:
corner protectors
The parts in wood and cardboard can be disposed of, respecting
the current regulations in the country where the machine is used.
ATTENTION: With remote versions, connect the appliance to
the drainage system for the defrost water (kits with automatic
condensate evaporation are available).
B.2.5 POSITIONING MODELS FOR USE WITH REMOTE UNITS
ATTENTION!
Installation of the appliance and the refrigerant
condensing unit must only be carried out by the
manufacturer’s service personnel or by a special-
ised technician.
Place the condensing unit in a well-ventilated room away from
heat sources.
If the remote unit is installed outdoors, it must be protected against
the action of atmospheric agents with adequate covering, in any
case ensuring correct ventilation of the condensing unit.
Choose pipe widths according to that given in the technical data
(for recommended units).
Lay the copper piping, choosing the shortest path and avoiding
bends, elbows and vertical sections as much as possible, keeping
to the following:
- in horizontal sections, the inlet line must slope down towards
the condensing unit at an angle of not less than 2%;
- traps must be installed before all upward sections of the inlet
line, at a distance of 3-3.5 metres from each other;
- insulate the inlet line with suitable lagging;
- it is advisable to install the remote unit at a max. pipe length
of between 15 m and 20 m from the appliance.
NOTE: If the distance exceeds 20 m, ask the technical depart-
ment for details or use a more powerful refrigeration unit.
• Install on the delivery line, in the following order: a suitably
sized dehydration filter, a liquid flow indicator and a solenoid
valve, if not present.
B.2.6 EVACUATING THE LINES AND CHARGING WITH
REFRIGERANT GAS
(for installation with remote refrigeration unit)
ATTENTION!
CHARGING WITH REFRIGERANT MUST BE DONE
BY PROFESSIONALLY QUALIFIED PERSONNEL.
B.2.6.1 Leakage test
- Wash the inlet and delivery pipes with pressurised dry nitro-
gen;
- connect a nitrogen cylinder to the high and low pressure con-
nectors, making sure to also install a pressure gauge (using
a “
T
” union), and charge the high and low pressure lines with
gas to a pressure of approx. 15 bar. Close the cylinder cock
and, after at least 1 hour, check that the pressure has not
dropped below the previous reading value.
B.2.6.2 Vacuum
- Empty the circuit manually by opening the cocks on the unions;
- connect the pipes to a vacuum pump (preferably a two-stage
model with vacuum gauge and high and low pressure connec-
tors). Reach a vacuum level equal to or lower than 70mTorr
(0.0931 mbar). On reaching this level, maintain it for about 15
minutes and then proceed with charging the unit as described
below.
B.2.6.3 Charging with refrigerant
- Charge the high pressure (HP) line with liquid refrigerant for
R404A (to ensure addition of the correct mixture) until bringing
the pressure above 0 bar (atmospheric pressure);
- then shut off the high pressure (HP) line, start the compres-
sor and charge with liquefied gas slowly with short impulses
from the low pressure (LP) line until the bubbles in the liquid
indicator disappear, being careful not to freeze the inlet pipe
(LP) near the compressor.
B.2.7 CHECKS WHEN STARTING UP THE APPLIANCE
Check on the liquid flow indicator that the circuit is sufficiently
charged. Otherwise, complete charging following the instructions
in § B.2.6.3.
Using a digital thermometer, check that the temperature reading
on the control panel matches the instrument reading.
B.2.8 ELECTRICAL CONNECTION
Connection to the power supply must be carried out in compliance
with the regulations and provisions in force in the country of use.
ATTENTION!
Work on the electrical systems must only be car-
ried out by a qualified electrician.
The ap pliance works on a single phase 230V 50Hz power supply .
To connect to the power supply, in sert the power cable plug in
the corr esponding mains so cket ,
first ma king su re :
- the so cket has an effi ci ent earth contact and the mai ns voltage
and frequency match that given on the dataplate. In case of
any doubts regarding the efficiency of the earth connection
have the system checked by qualified personnel;
- the system power supply is arranged and able to take the
actual current absorption and that it is correctly executed
according to the regulations in force in the country of use;
- a differential thermal-magnetic switch suitable for the input
specified on the dataplate, with contact gap enabling com
-
plete disconnection in category III overvoltage conditions and
complying with the regulations in force, is installed between
the power cable and the electric line. For the correct size of
the switch, refer to the absorbed current specified on the ap
-
pliance dataplate.