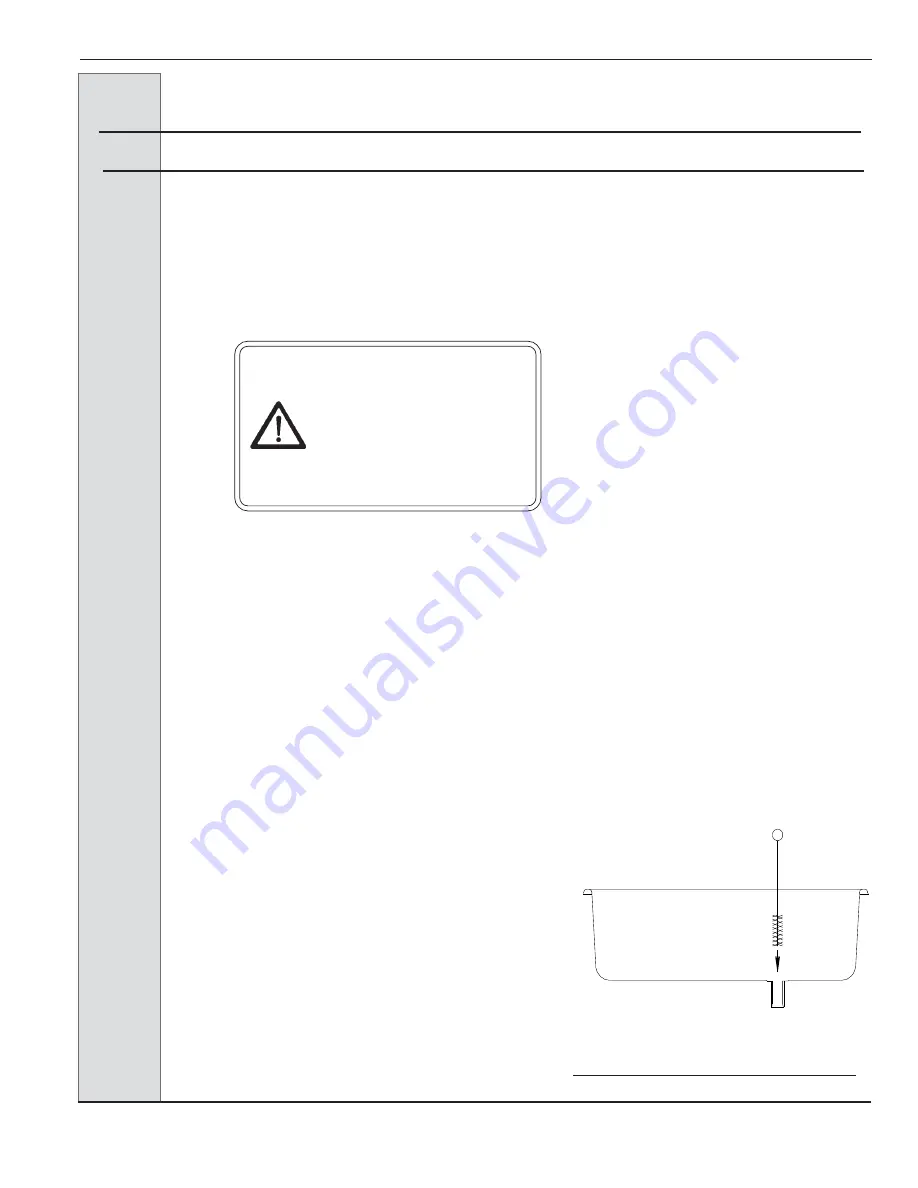
ELECTRO FREEZE Shake Model CS705
184592
23
8
Start-up Instructions
The sanitizing instructions explained in this
section are procedures to remove bacteria
and maintain a clean, sanitary freezer. The
shake freezer must be disassembled,
washed, and sanitized according to the
instructions in this manual before start-up
to insure the best possible cleanliness.
CAUTION
To prevent bacteria growth,
use only approved sanitizers
to sanitize the freezer.
Sanitizing must be done just
prior to starting the freezer.
Failure to do so could create
a health hazard.
Important:
Do not use unapproved sanitizer or
laundry bleach. These materials may
contain high concentrations of chlorine
and will chemically attack freezer
components.
NOTE:
It is your responsibility to be aware
of and conform to the requirements for
meeting federal, state and local laws
concerning the frequency of cleaning and
sanitizing the freezer.
1.
Prepare 2 gallons (7.6 liters) of
sanitizing solution in a container. Sanitizing
solution must be mixed according to
manufacturer’s instructions to yield 100
PPM strength chlorine solution. (example:
Stera-Sheen Green Label). Use warm
water (100-110°F or 37-43°C) to wash,
rinse, and sanitize.
2. Wash and sanitize your hands and
forearms.
3.
The mix feed tube assembly
should be laying in the bottom of the
hopper pan. Do not install.
Important:
Never let the sanitizer remain in the
freezer for more than 15 minutes.
8.1 Sanitizing
Important:
Do not insert any tools or objects into
the mix feed port or head dispensing
hole while the freezer is running.
4.
Pour sanitizing solution into the
hopper pan. Using a clean brush, scrub
the hopper walls, the mix feed port from
the hopper to the cylinder, the inside of
the mix feed tube and adapter (see figure
8-1), and the inside of the hopper cover.
5.
Insert mix float on mix level
sensor.
6.
Allow sanitizer to fill the cylinder.
7.
Connect the main power supply.
8.
The syrup switch should be in
the “OFF” position. Place the selector
switch to the "CLEAN" position and allow
the beater to run for 5 minutes. During
this time period check for leaks around the
head, plunger and drain tube.
9.
Place an empty container under
the dispensing head and drain the sanitiz-
ing solution from the cylinder by slowly
pulling down on the dispense handle.
Open and close the handle approximately
10 times during draining to sanitize the
port area of the dispense head.
10. With most of the sanitizing
solution drained, turn the selector switch
to the "OFF" position and drain remaining
solution from the hopper and cylinder and
close the plunger.
Figure 8-1
Sanitize hopper and its
components
Содержание COMPACT Series
Страница 2: ...This page is intentionally blank ...
Страница 10: ...This page is intentionally blank ...
Страница 15: ...ELECTRO FREEZE Shake Model CS705 184592 5 3 5 Dimensions Figure 3 2 Electro Freeze Model CS705 Dimensions ...
Страница 16: ...ELECTRO FREEZE Shake Model CS705 184592 6 4 Part Names and Functions Figure 4 1 Head Assembly 19 20 ...
Страница 24: ...ELECTRO FREEZE Shake Model CS705 184592 14 Figure 6 2 Dispense Head Assembly 6 2 DisassemblyInstructions ...
Страница 30: ...ELECTRO FREEZE Shake Model CS705 184592 20 Figure 7 4 Head Assembly 7 Assembly continued ...