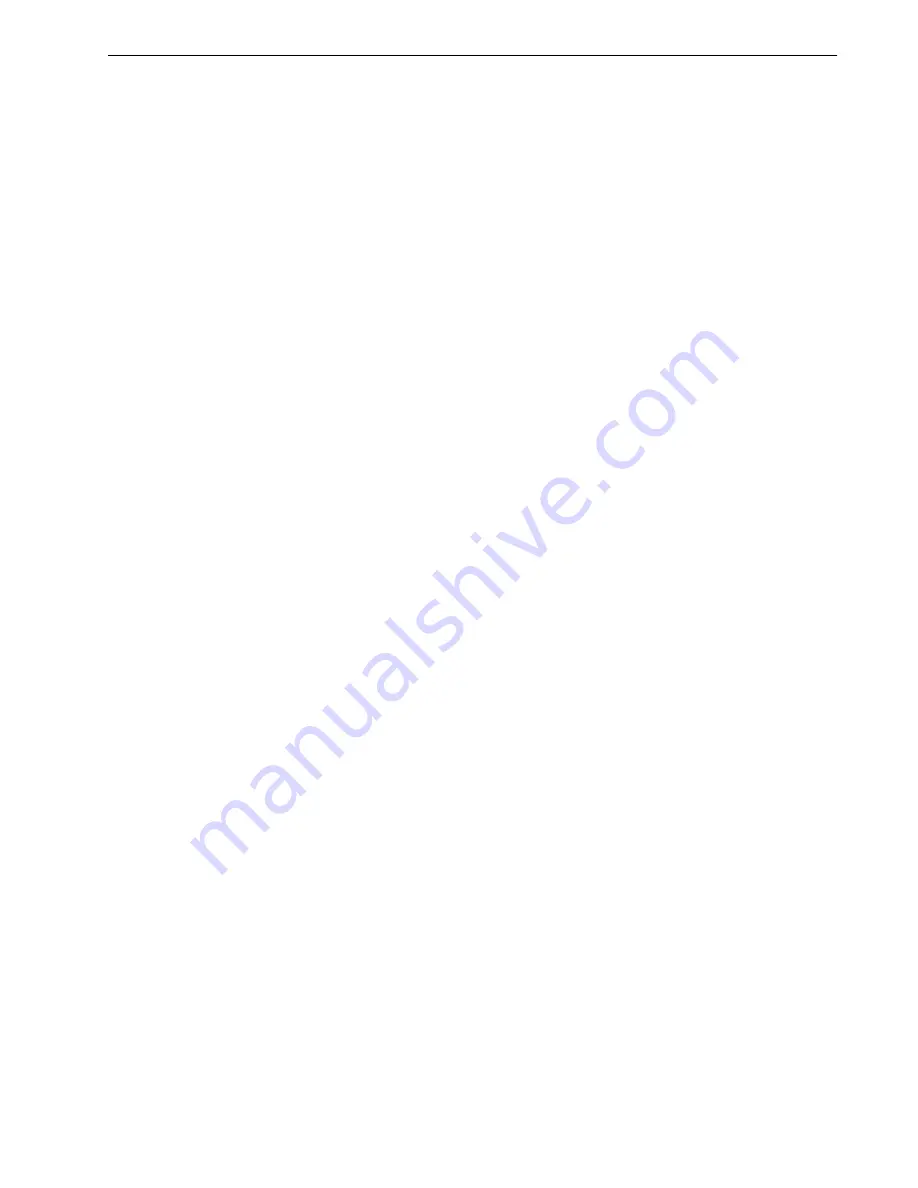
Applying Power for the First Time
3-3
Instruction Manual
13. Set the velocity command at approximately 0 VDC from the voltage source, and apply
power to the drive (with drive still enabled). Rotate the VCS gain potentiometer to the
full CW position.
14. Slowly increase the voltage applied at VCS+ from the velocity command voltage source
from 0 VDC to the maximum command (generally
±
10 VDC) and adjust the TACH gain
for the desired maximum motor RPM. The speed can be monitored by looking at the
voltage at the MVO output (P2 pin 8), or by using a hand held tach
15. Apply zero volts to VCS. If the motor is rotating slowly, readjust the BALance potenti-
ometer until the motor shaft remains stationary.
16. Disable the drive and connect the motor to the load.
17. Enable the drive and turn the COMP control CW until the motor shaft starts to oscillate,
then adjust it CCW until the oscillation stops.
Fine-tuning of the TACH pot and COMP pot may be required. Higher gain or faster
response is CW with both pots.
18. The motor/drive system is now ready for installation.
Remove power and remove setup wiring and jumpers.
19. Install drive and interface wiring to controller.
Internal Current Limit (ILIM)
4 turns CW = approximately 50% peak current (with no external current limit resistor)
8 turns CW = approximately 70% peak current (with no external current limit resistor)
16 turns CW = 100% peak current (with no external current limit resistor)
The average current limit will always be 50% of the peak current limit.
Balance Control (BAL)
With the drive enabled, the motor should not rotate when the drive is receiving a zero VCS
signal, but it may move slowly in either direction because of an offset in the drive circuits. This
potentiometer has control over the zero offset. Let the drive warm up to operating temperature
before adjusting the balance.
Servo Compensation (COMP)
The purpose of servo compensation circuits is to provide for an optimum servo system response
in a given application. This usually means an optimum velocity response to a step velocity
command signal (VCS), resulting in zero or negligible overshoot, proper damping, and mini-
mum response time. Refer to the “System Response to a Step VCS Input” on page 3-5. The COMP
network integrates the difference between VCS and tachometer feedback voltage signals (which
also improves the response and stability) but, at the same time, also slows down the response
of the entire system. An optimum COMP setting should be a compromise between system
stability and speed of response.
Tach Gain (TACH)
This potentiometer is used to scale the tachometer feedback voltage signal. This gain has no
effect on the scale of the MVO output signal.
Содержание MAX-430
Страница 33: ...Applying Power for the First Time 3 5 Instruction Manual Intro FIGURE 3 1 System Response to a Step VCS Input ...
Страница 36: ...3 8 Applying Power for the First Time P N 0013 1025 001 Rev F ...
Страница 42: ...4 6 Diagnostics Troubleshooting P N 0013 1025 001 Rev F ...
Страница 50: ...6 6 Component Ordering Information P N 0013 1025 001 Rev F ...
Страница 52: ...7 2 Reference Drawings P N 0013 1025 001 Rev F Intro FIGURE 7 2 Simplified Circuit Diagram ...
Страница 54: ...A 2 Differences from the MAX 400 P N 0013 1025 001 Rev F ...
Страница 58: ...Help 4 Documentation Improvement Form P N 0013 1025 001 Rev F Second Fold Tape First Fold ...