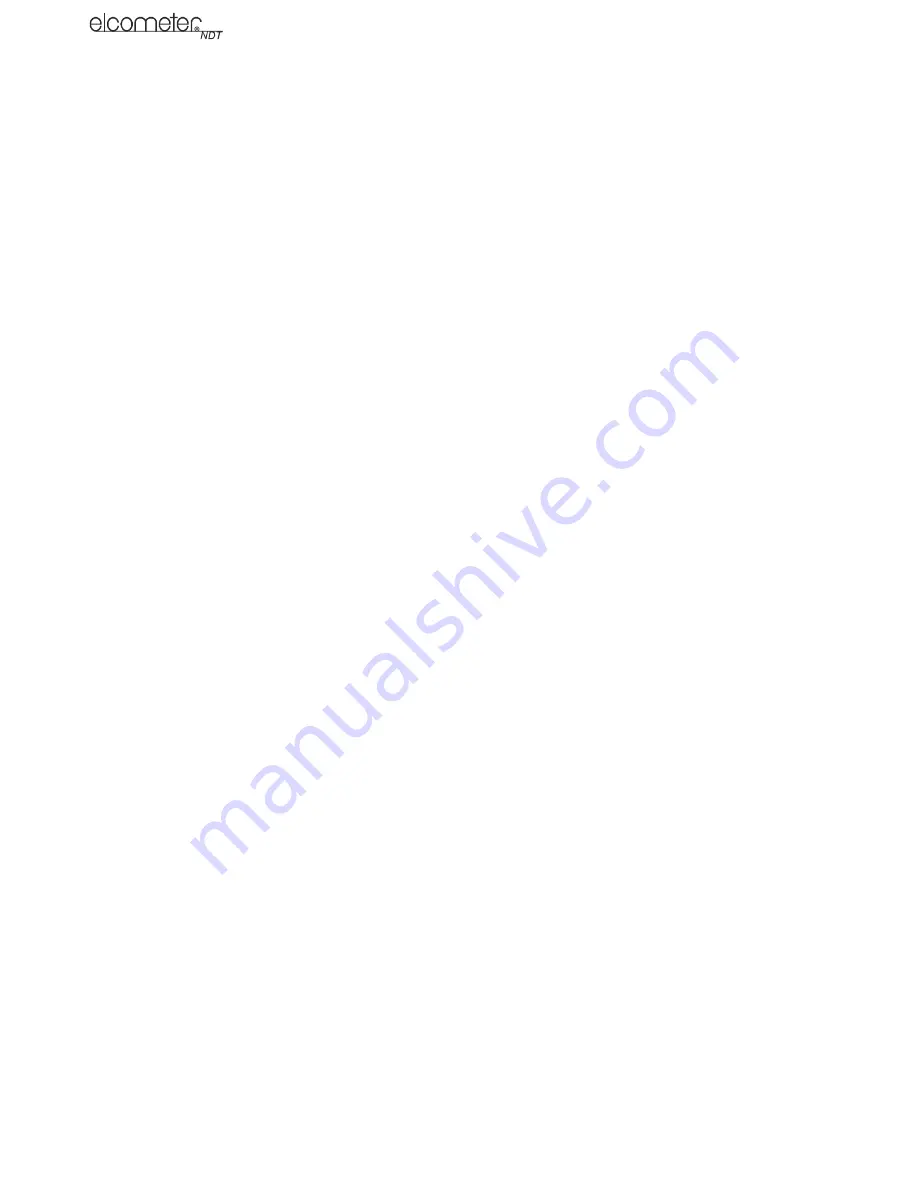
25
en
produce a best-fit line through the known loads, therefore minimising error.
The result is an added load offset (intercept), in the case of regression, and a load factor (slope) to correct
the ultrasonic measurements to the known loads. The regression produces a load offset and load factor,
while the vector sets the offset to zero and produces only a load factor. Why are both options needed? In
applications where a small amount of load is applied to the fastener, thus producing very little elongation,
the regression option can potentially produce non-linear results. In cases such as these, a vector may
sometimes produce better results as the offset is set at zero. It is recommended to use and compare both
results, following a field calibration, to determine which method is most suitable for the application and
produces the best results.
11.3 PERFORMING A FIELD CALIBRATION
This section outlines the procedure to perform a field calibration:
1.
Create a group in which to store field calibration data
2.
Select the calibration mode (vector or regression)
3.
Select the bolt material and conduct an auto set.
4.
Measure the length at each load and store these values in the group
5.
Calculate the load factor
Note: In the calibration procedure below, three sample bolts are used with three loads applied to each bolt
(1/3 load, 2/3 load, and maximum load). This should be considered the minimum requirement when
performing a field calibration.
11.3.1 Create a group in which to store field calibration data
You will save all the values and settings to a cell location in the group for easy recall at a later time. This will
allow you to easily verify the field calibration data.
To create a group, read the notes below and then follow the instructions given in “Creating a New Data
logger Group File” on page 32.
•
When you create the group, give it a NAME and NOTE which describe and make reference to the Field
Calibration data and bolt.
•
A group can contain up to 250 bolts. There must be at least one bolt in a group. You should specify a
minimum of three bolts in the group (this is the minimum sample size).
•
A bolt can have up to 51 possible measurements and one initial reference length. The initial reference
length is saved in a cell of column A of the group and other readings are stored in cells starting at
column B. There must be at least one reading per bolt. In the example used in this procedure, three
loads are applied to each bolt and therefore the measurements for these loads are saved in cells in
columns B, C and D.
11.3.2 Select the calibration mode (vector or regression)
Select MENU/CAL/LOAD CAL MODE and use LEFT and RIGHT to scroll between
•
OFF
•
VECTOR (zero offset)
•
REGRESSION
•
Press MEAS to return to the measurement screen
11.3.3 Select the bolt material and conduct an auto set
1.
Select MENU/GEOM/QUANTITY
2.
Use LEFT and RIGHT to change the QUANTITY value to ELONG
3.
Select MENU/MATL/TYPE press ENTER and select the material type from the list
4.
Press OK to confirm
5.
Set the value of ALEN/APPROX. LEN to the correct length of the fastener then conduce on AUTO
SET with the transducer attached to the fastener. See “Auto Set” on page 29.
11.3.4 Measure the length at each load and store these values in the group
1.
Place the first sample bolt in the load apparatus.