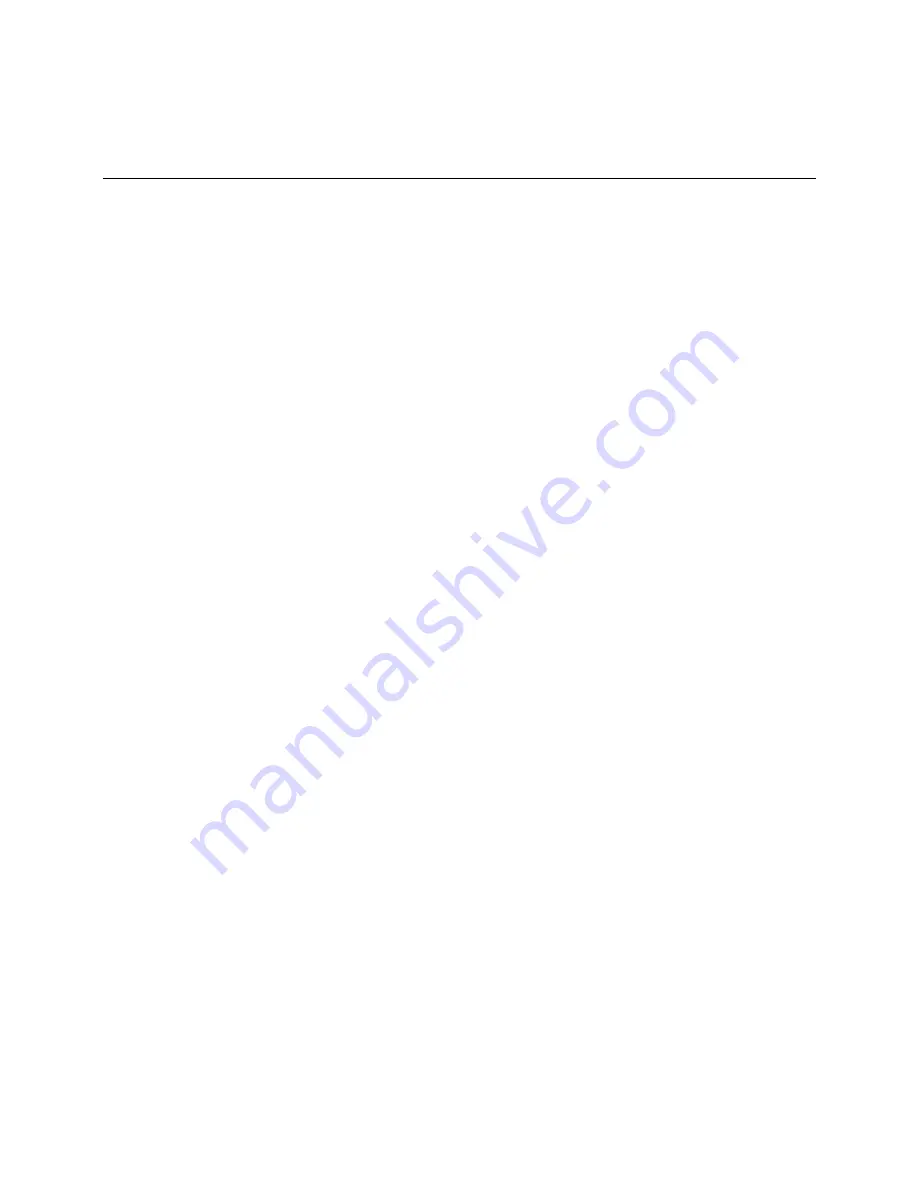
79
Start-up Light Oil
Checking Procedure
Function of the steplessly
controlling light oil burner
The light oil is supplied to the high-pres-
sure pump by an oil pump via ring line,
gas-air separator and service tank.
The light oil is flushed via the pressure
control valve on the oil control block.
When closing this flushing valve the oil
pressure will build up and open the
hydraulic ball-type valves in the feed
and return lines.
The pressure control valve (in oil control
block) installed downstream of the high-
pressure pump will keep the oil pres-
sure at the constant level of 28-30 bar in
accordance with an overflow principle.
The nozzle rod assembly has 2 connec-
tions, the oil feed and the oil return con-
nections. Two types of nozzle rods can
optionally be used, i.e. the RDG/RDN
and the MAT nozzle rods.
In the light oil mode it will be possible to
actuate, the feed and return valves at
the same time.
After the nozzle needle valve has ope-
ned in the nozzle rod the oil pressure
will be controlled via an oil controller in
the return line (minimum pressure
approx. 3-5 bar; maximum pressure
approx. 16-18 bar).
If the compound controller is increased
to maximum output, the oil pressure will
be brought to approx. 16-18 bar (maxi-
mum output of nozzle). This output
must correspond to the rated output of
the heat generator as shown in the
nozzle output diagram.
Simultaneously with the oil flow rate
control, the air flow rate control cam of
the compound control system will con-
trol the air flow rate required for the
combustion of the oil quantity supplied.
Check the following prior to the
initial operation of the boiler system:
- Take care to observe the operating
instructions supplied by the boiler
manufacturer. The boiler must be
mounted ready for operation.
- Ensure that the heating system is filled
with water.
- Check the complete system for correct
electrical wiring.
- Check the air fan and pump motor for
correct direction of rotation.
- For checking the direction of rotation
of the air fan and pump motors (direct
connection) shortly actuate or press
the contactor.
- In star-delta connection layouts it will
be necessary to actuate the mains and
star contactors at the same time.
- Check the correct direction of rotation
of the oil pump by comparison with the
direction-of-rotation arrow stamped to
the pump.
- Check for the proper setting of the
temperature and pressure controllers,
limiters, safety switches and electrical
limit switches.
- Bleed the fuel carrying lines, pumps
and pre-heaters (make sure no air is
contained).
- Check that the tank, lines and oil pump
are filled with oil and that the proper oil
nozzle has been fitted.
- Make a test of the hydraulic oil system
for absence of leaks.
- Check the exhaust gas ports are ope-
ned and sufficient fresh air is taken in.
- With the burner in starting position
check that air damper is closed.
- Check that the automatic furnace con-
troller is unlocked and in its original
position.
Oil start-up
- Open all stop valves of the oil supply
system; fill pumps with oil.
- Install feed pressure gauges, vacuum
gauges, pumps, etc.
- If a ring line is provided fill this with oil
and take it into operation. Check oil
temperature.
NOTE:
The hydraulic system is factory-
filled with test oil which might lead to
ignition trouble during initial start-up. To
protect the pump the oil pressure con-
troller is factory-set at a low pressure
only. When starting the burner make
sure to increase the oil pressure to ope-
rating level gradually.
Prior to initial fuel feed start make a
functional test of the burner program
flow.
Disconnect the lifting magnet of the
nozzle needle valve (solenoid valve) by
reference to the wiring diagram.
Start the burner and check the program
flow for correct sequence of start-up
operations.
1.
Flush via oil control block.
2.
Fan.
3.
Air damper pre-ventilation (check
limit switch setting).
4.
Check air pressure.
5.
Air damper starting load (check
limit switch setting).
6.
Ignition (ignition gas valves).
7.
Fuel valves.
8.
Shutdown on trouble after safety
time has run down (see automatic
furnace controller).
9.
Unlock automatic furnace control-
ler.