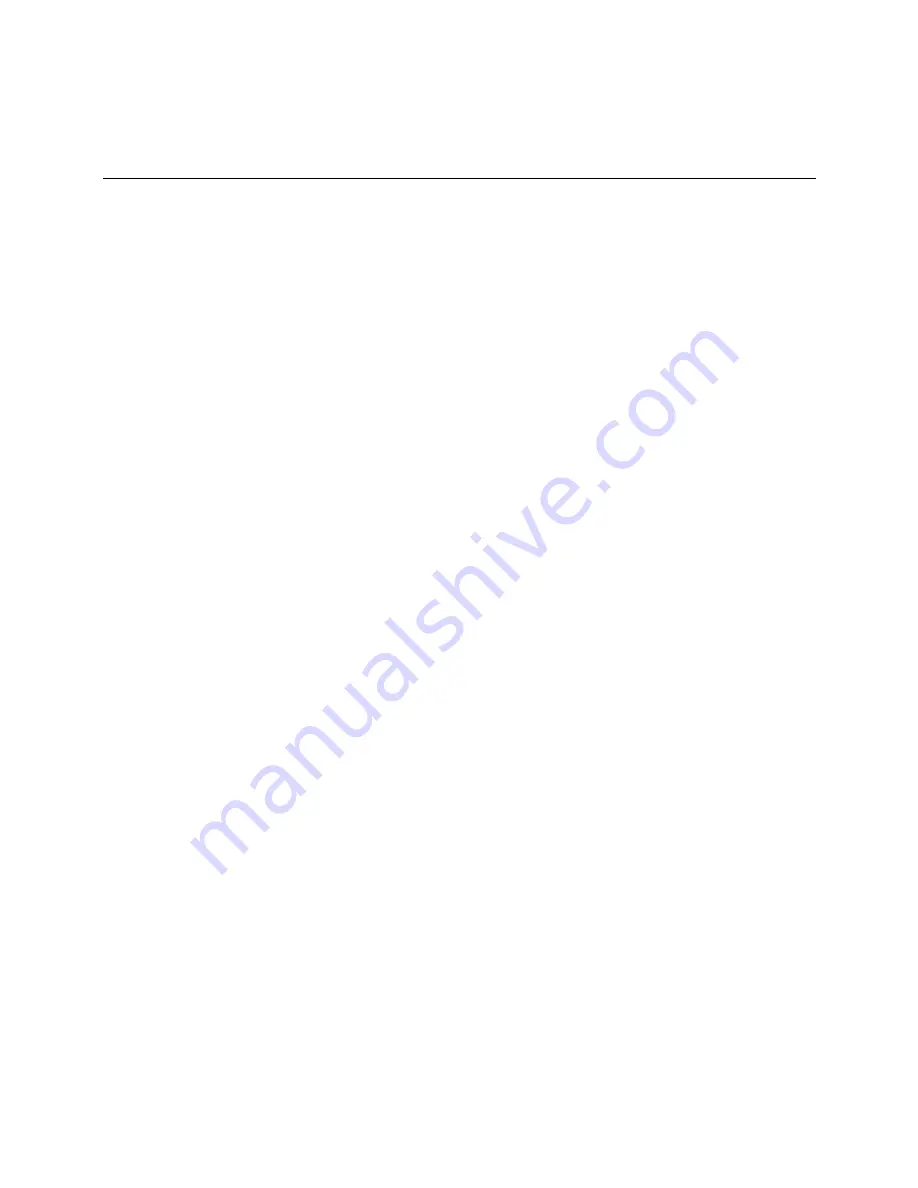
25
Oil Connection
Fuel Oil Supply
Oil connection
For the installation of a furnace system
care should be taken to observe the
applicable rules and regulations. When
installing an oil burner be sure to follow
the recommendations outlined for oil-
fired furnace systems (DIN 4787,
DIN 51603 Parts 1&2, TRD 411). DIN
4736 Parts 1 &2 describes the safety
requirements applicable to the oil sup-
ply systems of oil burners. DIN 4755
Part "Oil furnaces in heating installati-
ons (safety requirements)" outlines the
safety recommendations for oil furnace
systems of steam boilers.
The installer has the duty to inform
himself of the regulations applicable to
gas and oil furnace systems.
Fuel oil supply
Complete oil feeding groups are
available for the supply of the fur-
nace systems with fuel oil. A fuel oil
supply unit may consist of ball stop
valve, suction filter, pressure gauge,
pump with coupling and three-
phase rnotor. All units are all finis-
hed ready for connection and
mounted with anti-vibration ele-
ments on an oil collecting tray.
The oil supply lines must be slelec-
ted in accordance with the technical
instruction sheets and installed in
line with the applicable specificati-
ons. The total pipeline length is
understood to be the length of all
horizontal and vertical lines and
bends. The maximum permissible
vacuum at the suction port of the
pump may be -0.6 bar. A higher
vacuum will lead to the escaps of
gas resulting in an unsteady deli-
very and damage to the pump.
All connections must be tightened
to avoid leaks. The sealing rings
used should be of copper, alumi-
nium or plastic. In no case should
hemp or similar sealing material be
used. The pipelines must be clea-
ned before they are connected to
the pump.
Ring line operation
lf several burners and storage tanks are
installed in a system or if there is a large
distance between the burner and the
storage tank, a ring line system with
gas-air separater will be needed for
supplying the burners.
NOTE: In case of pressurized oil feed,
the suction pressure of the pump should
not exceed 5 bar. All lines must be
fixedly installed, welded to oil-tight stan-
dards or connected with oil-tight unions
or flanges.
Flexible tubes are allowed only as con-
necting pieces between the fixed line
and the burner. The flexible tubes
should be installed properly (in hanging
position) and free of sharp bends.
For the installation of the flexible
tubes take care these do not get
twisted. They should not be subject
to torsional stress neither at the
stage of installation nor during sub-
sequent movernents.
Oil pressure pump filling
Prior to initial oparation make sure to fill
the oil pressure pump and oil feed line
with oil to prevent the pump from dry
running and getting seized.
Oil filter
lt is recommended to install a filter
directly upstream of the pump to sepa-
rate dirt particles contained in the oil or
any other foreign matter produced
during installation. When a fuel oil unit is
mounted this will be fitted with an oil fil-
ter already.
Starting the oil pump
-
Make sure all stop valves are
open.
-
Check the pump for direction of
rotation.
-
The safety overflow valve in the
pump is preset at 40 bar and may
be readjusted by duly authorized
specialists only.
Pressure atomizer
The oil throughput rate of the nozzle
and thus the burner output is controlled
by an oil regulator valve installed in the
return line and coupled to the actuator
and compound controller.
The oil throughput rates and oil flow
pressures downstream of the nozzle rod
must be set according to the applicable
nozzle characteristic.
As the oil control valve is closed or ope-
ned the oil throughput rate of the nozzle
will be increased or reduced, respec-
tively.
The oil pressure upstream of the nozzle
rod must be set at 28 bar to 30 bar.
Depending on the version this can be
can be adjusted either on the fuel oil
station or on the oil control block of the
burner.