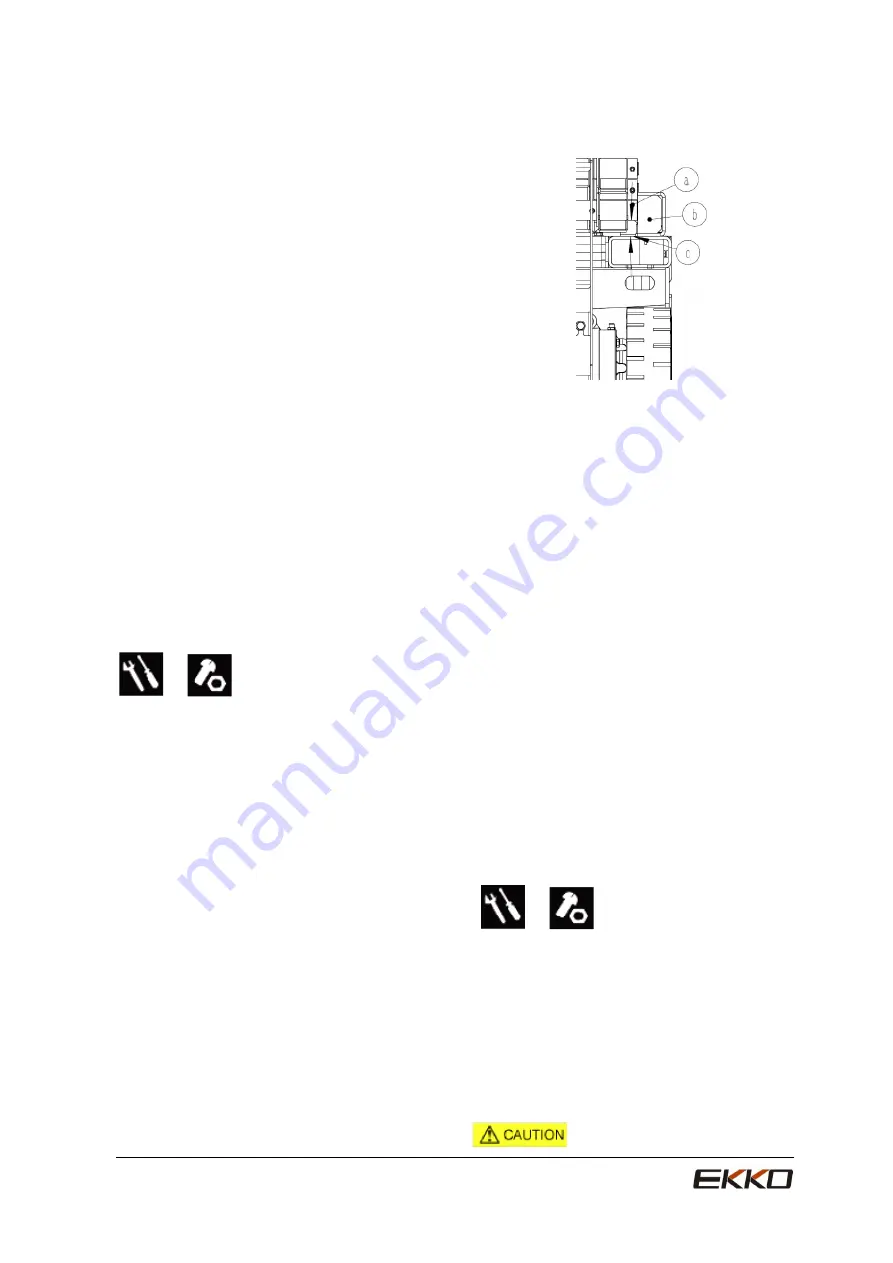
Maintenance
54
This procedure should be performed every
500 hours or six months, whichever comes
first.
The hydraulic tank is a vented-type tank. The
breather cap has an internal air filter that can
become clogged or, over time, can deteriorate.
If the breather cap is faulty or improperly
installed, impurities can enter the hydraulic
system which may cause component damage.
Extremely dirty conditions may require that the
cap be inspected more often.
1. Remove and discard the hydraulic tank
breather cap.
2. Install the new cap onto the tank.
Checklist D
D-1
Check the Scissor Arm Wear Pads
This procedure should be performed every
1000 hours or annually, whichever comes first.
Maintaining the condition of the scissor arm
wear pads is essential to safe machine
operation. Continued use of worn-out wear
pads may result in component damage and
unsafe operating conditions.
Perform this procedure with the machine on a
firm, level surface that is free of obstructions.
1. Measure the distance between the
number one inner arm cross tube and the
chassis deck at the ground controls side of
the non-steer end of the machine.
a. inner arm cross tube
b. wear pad
c.
chassis deck
⊙
Result: The measurement is not less than x
mm. (ZS07
:
x=34.5
,
ZS12
:
x=38) Refer to
Step2.
¤
Result: The measurement is less than x
mm. Replace the Scissor Arm Wear Pads
2. Measure the distance between the
number one inner arm cross tube and the
chassis deck at the battery pack side of
the non-steer end of the machine.
⊙
Result: The measurement is not less than x
mm. Refer to Step 3.
¤
Result: The measurement is less than x mm.
Replace the Scissor Arm Wear Pads
3. Apply a thin layer of dry film lubricant to
the area of the chassis where the scissor
arm wear pads make contact.
D-2
Replace the Hydraulic Tank Return
Filter Element
This procedure should be performed every
1000 hours or annually, whichever comes first.
Replacement of the hydraulic tank return filter
is essential for good machine performance
and service life. A dirty or clogged filter may
cause the machine to perform poorly and
continued use may cause component damage.
Extremely dirty conditions may require that the
filter be replaced more often.
Scalding danger
Содержание ES100E
Страница 5: ...Decals 3 ...
Страница 7: ...Decals 5 ...
Страница 9: ...Decals 7 ...
Страница 59: ...Electrical Schematic Diagram 57 ES40E ...
Страница 60: ...Electrical Schematic Diagram 58 ES60E ES80E ES100E ES120E ...
Страница 62: ...Hydraulic Schematic Diagram 60 ES80E Y7 Y7 G1 4 19 Y1 Y1 Y2 Y2 Y3 Y3 Y4 Y4 Y5 Y5 Y6 Y6 ...
Страница 63: ...Hydraulic Schematic Diagram 61 ES100E ES120E Y7 Y7 G1 4 19 Y1 Y1 Y2 Y2 Y3 Y3 Y4 Y4 Y5 Y5 Y6 Y6 ...
Страница 64: ...Hydraulic Schematic Diagram 62 Maintenance Record Date Note ...
Страница 65: ......