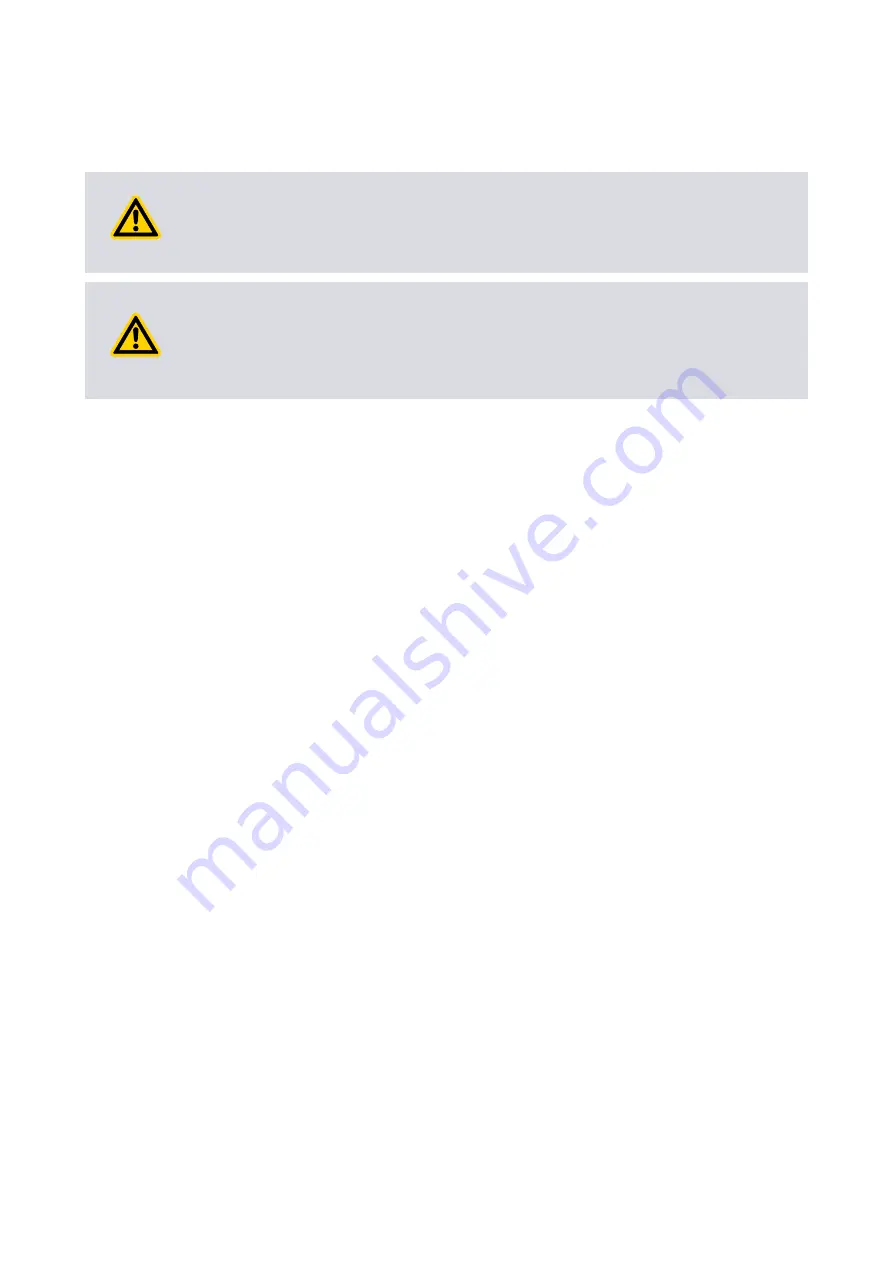
9. Storage
WARNING: INHALATION HAZARD
Risk of asphyxiation. Do not burn the fluoroelastomer seals and O-rings.
CAUTION: LUBRICATION TRANSFER
Risk of damage to equipment. Install blanking plates to seal the vacuum inlet and
outlet port. The pumps must be stored in a horizontal configuration to prevent
possible lubrication transfer.
To store the pump:
1.
Shut down the pump. Refer to
on page 35.
2.
Disconnect the pump from the electrical supply.
3.
Place and secure protective covers over the inlet and outlet ports.
4.
Store the pump in a clean and dry condition until required for use.
5.
When necessary, prepare and install the pump. Refer to
on page 19.
05/2021 - ©Edwards Limited
Page 45
A90301880_C
A90301880_C - Storage
Содержание nXR120i
Страница 53: ...This page has been intentionally left blank ...
Страница 54: ...This page has been intentionally left blank ...
Страница 55: ...This page has been intentionally left blank ...
Страница 56: ...edwardsvacuum com ...